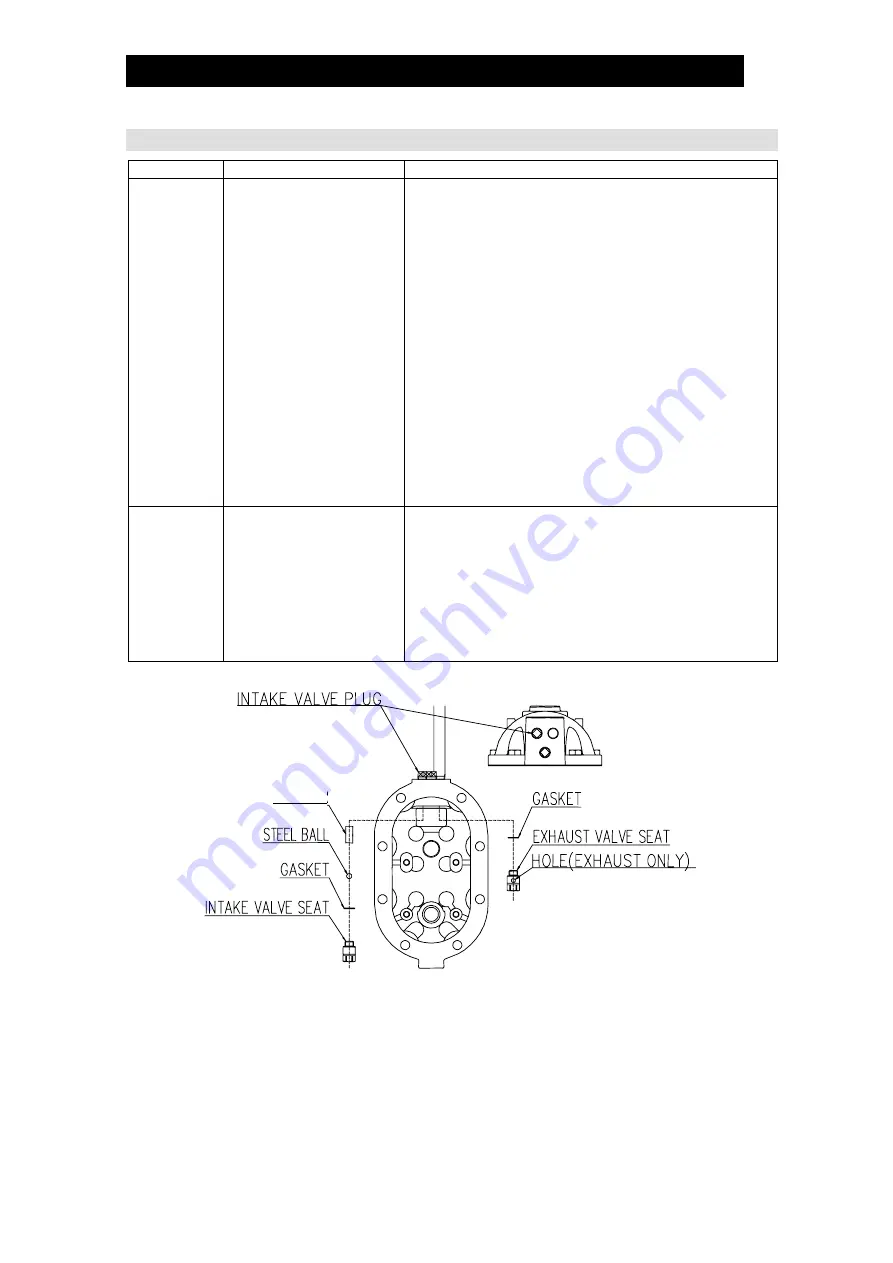
172-65043MA-02 (GP10L/GT10L
PowerTrap
) 9 Mar 2004
28
7. Removing / Reinstalling the Motive Medium Intake and Exhaust Valve Seats
Part / Step
Disassembly
Reassembly
Motive
Medium
Intake:
Valve Seat /
Steel Ball /
Screen /
Gasket
• Remove with a 22 mm
(
⅞
") socket wrench and
extension bar, being
very careful not to drop
the steel ball and screen
resting on top of the
valve seat.
• Be careful not to lose
the gasket.
• Make sure you are reinserting the intake (motive
medium) valve seat, which has no holes. (The seat
with the holes is the exhaust valve seat.)
• Make very sure you are reinserting the intake valve
seat into the left hole in the top of the cover. (It is the
hole with the plug in the top.)
• Insert the valve seat, with its gasket, from the bottom
of the hole, then hand tighten.
• Remove the plug from the top with a 300 mm (12")
adjustable wrench.
• Drop the screen straight into the hole, and then drop
in the ball.
• Wrap plug threads with 3 – 3.5 turns of sealing tape
or apply sealing compound.
• Check that the screen is seated straight, then reinsert
the plug.
• Tighten the plug to a torque of 30 N
⋅
m (22 ft
⋅
lb).
• Tighten the valve seat to a torque of 80 N
⋅
m
(59 ft
⋅
lb).
Exhaust:
Valve Seat /
Gasket
• Remove with a 22 mm
(
⅞
") socket wrench and
extension bar.
• Be careful not to lose
the gasket
• Make sure you are reinserting the exhaust valve seat,
which has holes. (The seat with no holes is the intake
valve seat.)
• Make very sure you are reinserting the exhaust valve
seat into the right hole in the top of the body. (It is the
hole with no plug in the top.)
• Insert the valve seat, with its gasket, from the bottom
of the hole, hand tighten, then tighten to a torque of
80 N
⋅
m (59 ft
⋅
lb).
1 N
⋅
m
≈
10 kg
⋅
cm
2
(MOTIVE MEDIUM)
(MOTIVE MEDIUM)
SCREEN
Summary of Contents for PowerTrap GP10L
Page 36: ......