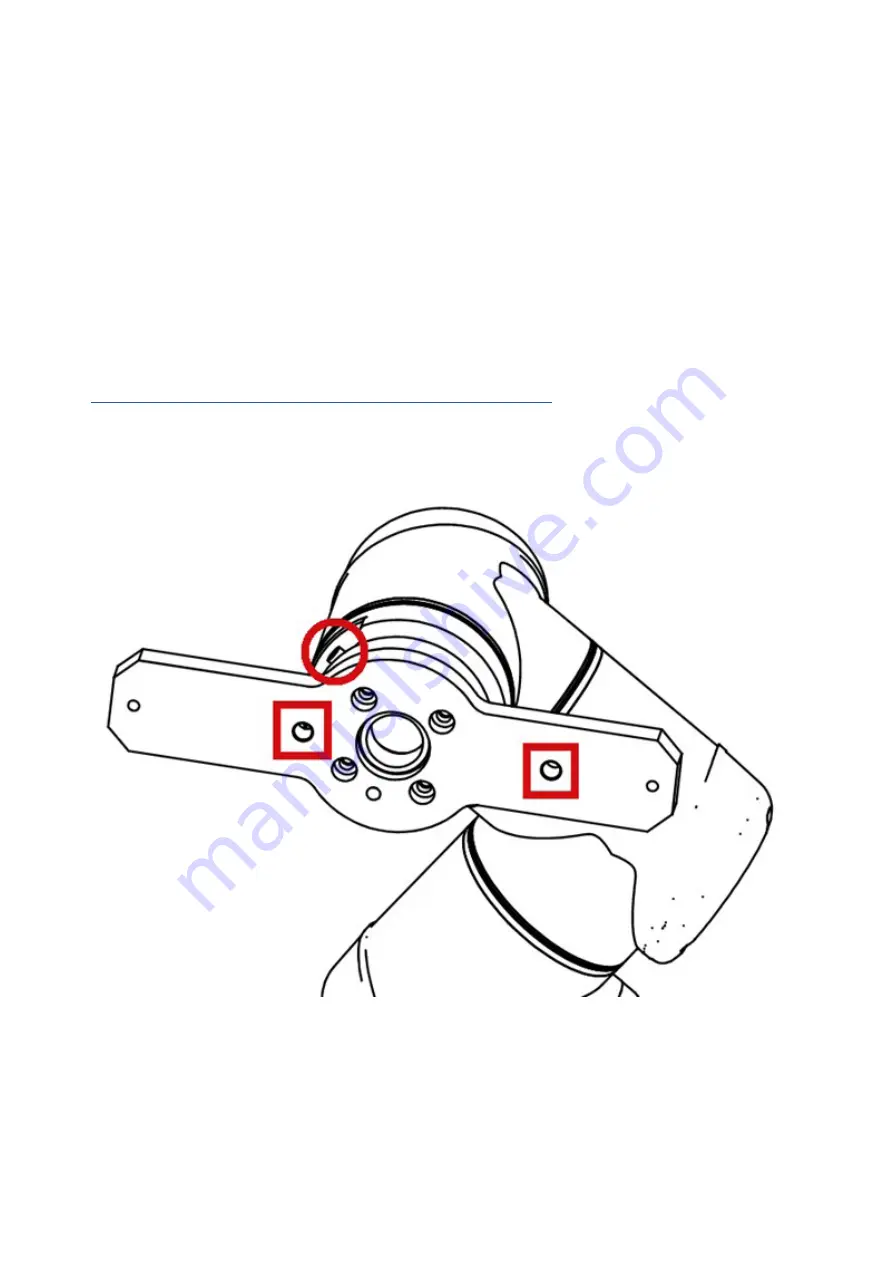
6
2.2. Hardware assembly
— Mount the UR robot to the required position. For SAN2 application the orientation of the robot may be arbitrary
regarding your particular setup. Connect the robot and UR Control box. During this step, please follow Universal Robots
instructions delivered together with the robot
— To connect and assemble the SAN2 system, please follow the document
Equipment Installation
for SAN 2.
—
The rivet charger has to be mounted in the fixed position
— The riveting head has to be mounted on the robot arm. The mounting plate between the robot TCP and riveting
head is provided as a special accessory. When mounting the flange if possible, please follow the orientation
showed in Figure 2. This orientation is considered when setting the TCP/Tool coordinates and orientation. In case
this orientation does not suit your application (e.g. robot violates its working envelope), different orientation is
possible. However, the TCP/Tool orientation has to be setup accordingly
— Note that if the technical support has been requested during the order, our team will help you with assembly
and first startup
— Connect the SANK2 control unit and UR Control box with the Ethernet cable
— Install the SAN2 URCap. For this step, you will need a USB storage device. Download the URCap available at
https://www.titgemeyer.com/en/tools-automation/service/download-center/
and save it to a USB storage device.
Figure 2 Standard orientation of the flange mounted on the robot arm
All t
echnic
al specific
ations c
ont
ained in this br
ochur
e ar
e appr
o
ximat
e and no g
uar
ant
ee is giv
en as t
o their ac
cur
acy
. De
signs ar
e subjec
t t
o chang
e.
Titgemeyer / 10273EN1120 / 1
Equipment Installation