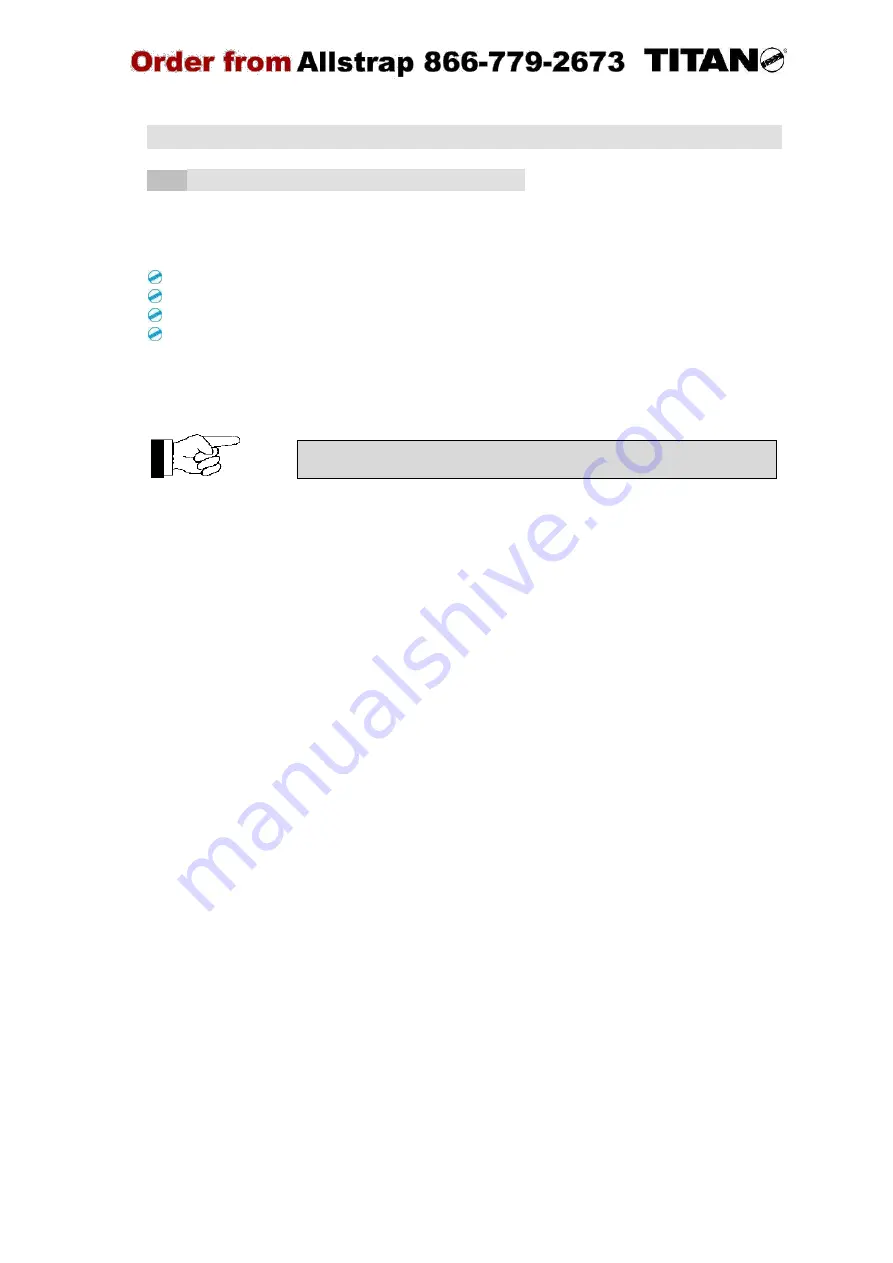
8. Maintenance
8.1. Cleaning and maintenance of the unit
Soil and debris hamper the proper functioning of the tool. For this reason, the following
areas should be cleaned once a week (blow off using compressed air if possible):
insertion slot,
cavities between the upper and lower knives,
tensioning wheel,
gripper plate
Lubricate with fine conventional spray oil afterwards.
Tool inspection!
Perform a
daily
visual inspection of the outside of the unit. The early detection of
damaged parts extends the life of the unit. Replace all damaged parts
immediately
with Original TITAN spare parts.
HPE
H 224 EU 07/10
Do not use any solvent containing cleaning agents for
reasons of health.