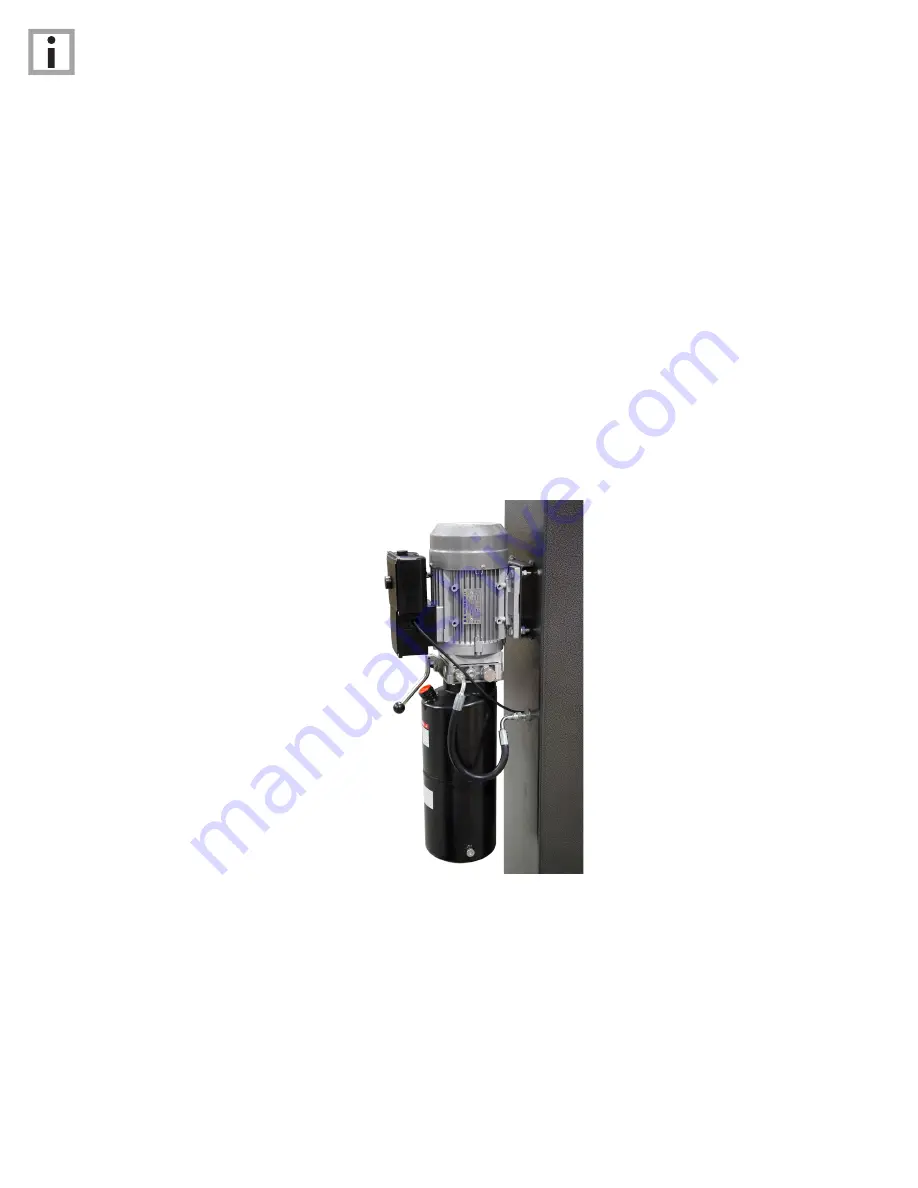
17
8.2 MAINTENANCE BY OPERATOR
8.2.1 HYDRAULIC SYSTEM
8.2.2 GREASING POINTS
All moving parts have been lubricated at the factory and should be re-lubricated before the
first use and at least once every six months to prevent damage.
IMPORTANT: AFTER CLEANING WORKSHOP FLOOR OR LIFT, TO MAINTAIN
HOIST EFFICIENCY WE ADVISE TO LUBRICATE LIFTING ARM LOCKING
MECHANISM, AND SAFETY LOCKING MECHANISM. CHECK SAFETY LOCKING
MECHANISM IS FUNCTIONING CORRECTLY.
FIG. 2
SLIDE TRACKS:
•
The carriage assembly slide tracks should be greased every six months (or more
frequently in case of noise generation).
•
Slightly grease the slide tracks over their whole length using a brush.
ARM PINS:
•
Grease the arm pins to prevent excessive wear
1.
Check the fluid level with the lift fully lowered and add fluid as required. Use premium
quality ISO-32, AW-32, or AW-46 hydraulic oil.
2. Visually check all hydraulic hoses and connections for tightness before each use to
ensure proper working condition.
3.
Lightly oil the cylinder rods at least once every six months or when they become dry.
Summary of Contents for HD2P-13KCL
Page 25: ...21 FIG 1 HD2P 13KCL 117 50 142 75 151 00 4 72 75 32 45 50 11 DIAGRAMS FIG 1 8...
Page 26: ...22 FIG 2 HD2P 13KCL Column Anchor Bolts 3 4 6 25 Column 6 Concrete 3000PSI min Torque Nut...
Page 32: ...28 FIG 8 CABLES HOSES...
Page 35: ...31 NOTES...
Page 38: ......
Page 39: ...NOTES...