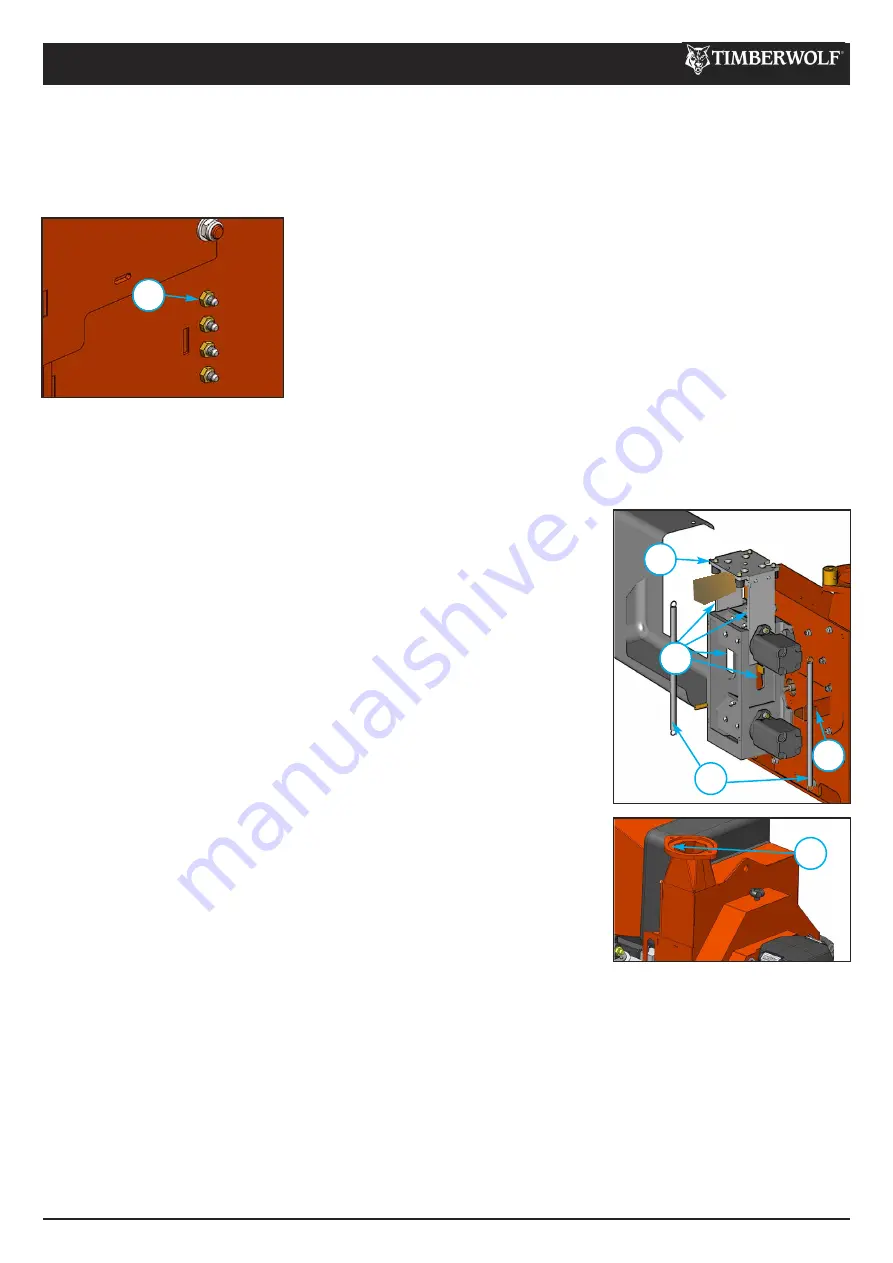
TW 160PH
SERVICE INSTRUCTIONS
20 / 51
C190-0013
11.04.2019
3
5
4
All the hydraulic hoses should be regularly inspected for chafing and leaks. The hydraulic system is pressurized to 150
Bar and thus the equipment containing it must be kept in good condition.
Identify the hoses that run to the top motor. These have the highest chance of damage as they are constantly moving.
If any hydraulic components are changed new seals should be installed during reassembly. Fittings should then be
retightened.
GREASE THE ROLLER BOX SLIDES
CHECK HOSES
All engine servicing must be performed in accordance with the Engine Manufacturer’s handbook provided with
the machine.
FAILURE TO ADHERE TO THIS MAY INVALIDATE WARRANTY AND/OR SHORTEN THE LIFE OF THE
ENGINE.
NOTE: This should be done regularly. In dirty and dusty conditions or during periods of hard work it should
be daily. If the bearings and splines are allowed to run dry premature wear will occur resulting in a
breakdown and the need for replacement parts. This failure is not warranty. Early signs of insufficient
grease includes squeaking or knocking rollers.
1
Locate the greasing panel.
1
Apply 4+ pumps of grease to each nipple.
2
It is recommended to grease all the nipples whilst the engine is running
3
and rollers are turning to distribute the grease evenly.
DO NOT USE
GRAPHITE BASED GREASE.
Both front and rear bearings are greased by nipples A and B. The top
4
and bottom roller splines are greased by nipples C and D.
GREASE THE ROLLER SPLINE AND ROTOR BEARINGS
A
B
C
D
NOTE: This should be done regularly. In dirty or dusty conditions or during periods of hard work it should be
done weekly. If the slides become dry the top roller will tend to hang up and the pulling-in power of the
rollers will be much reduced. Excessive wear will ensue.
Remove the discharge tube.
1
Apply multipurpose grease to surface shown.
2
Refit discharge tube.
3
GREASE THE DISCHARGE FLANGE
ENGINE SERVICING
Turn the chipper off and remove the ignition keys.
1
Ensure machine has come to a complete stop - remove battery leads.
2
Remove the bolt and washer retaining roller box guard and lift guard.
3
Remove the two springs on the roller box slide.
4
NOTE: Rollerbox slide weighs in excess of 20kg.
Lift the top roller and
5
wedge a suitably sized piece of wood to hold in place.
Apply thin grease with a brush to each slide on roller box and on inner
6
cheeks of slider.
DO NOT USE GRAPHITE BASED GREASE.
NOTE: Rollerbox slide weighs in excess of 20kg.
Remove wedge, lower
7
roller box slide and replace springs.
Close roller box guard making sure that it is located over the retaining
8
bracket, and ensure bolt and washer (as note 3) are tightened.
Refit battery leads
.
9
2
6
Summary of Contents for TW 160PH
Page 1: ...timberwolf uk com INSTRUCTIONMANUAL TW 160PH WOOD CHIPPER...
Page 25: ...TW 160PH DECLARATION OF CONFORMITY 22 51 C190 0013 11 04 2019...
Page 26: ...TW 160PH IDENTIFICATION PLATE 23 51 C190 0013 11 04 2019 EXAM PLE...
Page 37: ...TW 160PH 34 51 C190 0012 11 04 2019...
Page 38: ...35 51 C190 0012 11 04 2019 TW 160PH...
Page 39: ...36 51 C190 0012 11 04 2019 TW 160PH...
Page 40: ...TW 160PH 37 51 C190 0012 11 04 2019...
Page 41: ...TW 160PH 38 51 C190 0012 11 04 2019...
Page 42: ...TW 160PH 39 51 C190 0012 11 04 2019...
Page 44: ...TW 160PH 41 51 C190 0012 11 04 2019...
Page 45: ...TW 160PH 42 51 C190 0012 11 04 2019...
Page 46: ...TW 160PH 43 51 C190 0012 11 04 2019...
Page 47: ...TW 160PH 44 51 C190 0012 11 04 2019...
Page 48: ...TW 160PH 45 51 C190 0012 11 04 2019...
Page 49: ...TW 160PH 46 51 C190 0012 11 04 2019...
Page 50: ...TW 160PH 47 51 C190 0012 11 04 2019...
Page 51: ...TW 160PH 48 51 C190 0012 11 04 2019...