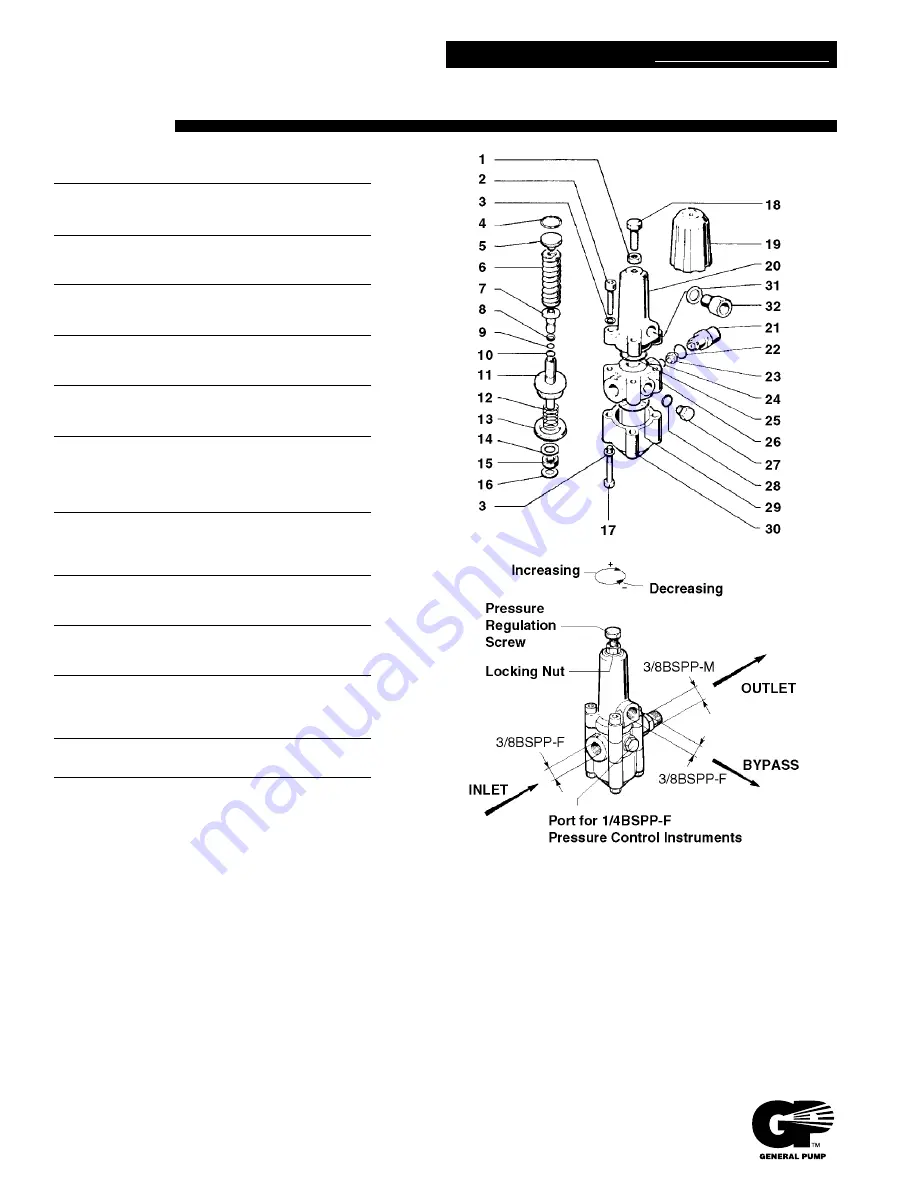
K7 Unloader Valve
NO.
PART NO.
DESCRIPTION
KIT NO.
QTY.
1.
92.2368.00
Nut
1
2.
99.3084.00
Screw
4
3.
96.7014.00
Washer
8
4.
90.3849.00
O-Ring
70
1
5.
36.3095.70
Spring Plate
1
6.
94.7466.00
Spring
1
7.
36.3094.66
Seat Valve
70
1
8.
90.5052.00
Anti-Extrusion Ring
70
1
9.
90.3820.00
O-Ring
70
1
10.
90.3582.00
O-Ring
70
1
11.
36.3097.02
Piston Assembly
70
1
12.
94.7464.00
Spring
70
1
13.
90.2766.00
Packing
70
1
14.
96.7215.00
Washer
1
15.
90.2565.00
Packing
70
1
16.
90.5063.00
Anti-Extrusion Ring
70
1
17.
99.3127.00
Screw
4
18.
99.3663.00
Screw
1
19.
36.3098.02
Optional Adjust. Knob
1
20.
36.3090.41
Upper Body
1
21.
Nipple
1
10.0078.70
K7.0, 3/8 BSPP, Ø3.0 mm
10.0078.70
K7.1, 3/8 BSPP, Ø3.0 mm
10.0160.70
K7.2, 3/8 BSPP, Ø3.25 mm
10.0161.70
K7.3, 3/8 BSPP, Ø3.5 mm
22.
90.3833.00
O-Ring
70
1
23.
Nozzle
1
10.0076.66
K7.0, Ø2.2 mm
10.0077.66
K7.1, Ø2.5 mm
10.0162.66
K7.2, Ø2.75 mm
10.0163.66
K7.3, Ø3.0 mm
24.
90.3823.00
O-Ring
70
1
25.
90.3863.00
O-Ring
70
1
26.
36.3091.41
Central Body
1
27.
98.2041.00
Cap Screw
2
28.
90.3585.00
O-Ring
70
2
29.
90.3871.00
O-Ring
70
1
30.
36.3092.41
Lower Body
1
31.
96.7380.00
Washer
1
32.
Nipple
1
36.3117.70
K7.0, 3/8 BSPP
36.3116.70
K7.1, 3/8 BSPP
36.3118.70
K7.2, 3/8 BSPP
36.3119.70
K7.3, 3/8 BSPP
Repair Kit 70
Includes No.'s:
4, 7, 8, 9, 10, 11, 12, 13,
15, 16, 22, 24, 25, 28, 29
INSTALLATION
Select an unloader appropriate for the
pressure and flow of your system (see
specification chart). This unloading valve is a
flow-through design and should be mounted
on the discharge line of the pump in any
position (horizontal or vertical) which allows
easy access to the adjusting bolt. A pressure
gauge should be installed on either side of the
port of the unloader to accurately read
pressure during adjustment. Minumum 5%
bypass is required for proper operation.
WARRANTY
General Pump accessories are warranted by the manufacturer to be free from
defects in material and workmanship Period of warranty shall be 90 days from
date product is received by original buyer. Liability of manufacturer under the
foregoing warranty is limited to repair or replacement at the option of
manufacturer of that product which according to the manufacturer's
investigation was deemed defective at time of shipment. Damage resulting
from neglect, abuse, tampering or misapplication voids this warranty. This
warranty is in lieu of all other warranties, expressed or implied, including any
warranty of merchantability and/or any and all other obligations or liabilities on
the part of the manufacturer.
PARTS LIST
K7
GENERAL PUMP
A member of the Interpump Group
300110 Rev. B
2-95
GENERAL PUMP
1174 N
ORTHLAND
D
RIVE
• M
ENDOTA
H
EIGHTS
, MN 55120
P
HONE
: (651)454-6500 • F
AX
: (651)454-4524 • e-mail: [email protected] • www.generalpump.com