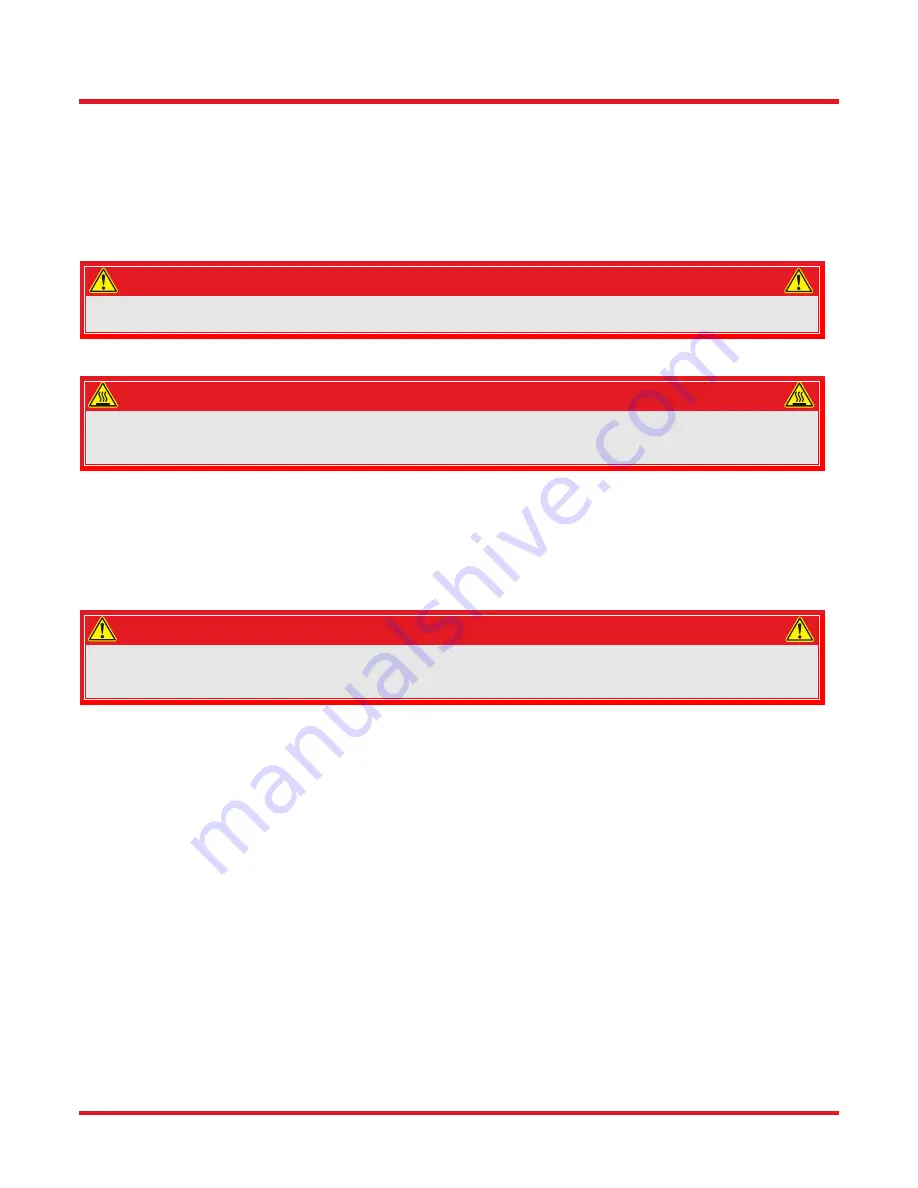
LFS4100
Chapter 6: Fusion Splicing
Page 24
TTN047498-D01
Chapter 6
Fusion Splicing
Fusion splicing is a process of joining two optical fibers end-to-end using heat. The goal is to fuse the two fibers
together in such a way that light passing through the fibers is not scattered or reflected back by the splice, and the
splice and the region surrounding it are almost as strong as the virgin fiber itself. This chapter will deal exclusively
with the manner in which the LFS4100 can be used to perform high-quality fusion splices.
6.1. Filament Fusion
WARNING
The filament in the LFS4100 furnace generates intense light when it is in operation. It is strongly
advised that the user NOT look directly at it during splicing or tapering operations.
CAUTION: HOT SURFACE
The furnace gets extremely hot when the filament turns on. Touching the furnace immediately after
the filament has been on for a few seconds, such as after a splicing or tapering operation, is
STRONGLY ADVISED AGAINST
The LFS4100 uses a graphite or iridium filament to provide the heat necessary to fuse fibers together. The
filament is a resistive heater typically shaped like an upside-down omega that is open at the top. In the beginning
of the process, the fibers are roughly positioned in the center of the camera viewing area. Depending on the
alignment method selected, the LFS4100 software will use inputs from the CCD camera or an external optical
power meter to precisely align the fibers. Computer-controlled stepper motors are used to position the fibers
during alignment and to push the fibers together during the filament fusion.
WARNING
The fiber handlers and the splice head can exert a fair amount of force as they move from side to
side. It is strongly advised that users NOT put their fingers between them, or between the fiber
handlers and the slot end walls, while the machine is in operation.
After the software aligns the fibers, the splice head is repositioned to center the filament under the fiber ends.
Power is then applied to the filament to raise its temperature to a level hot enough to fuse the fibers together,
typically about 2000 °C. Because the filament would oxidize (burn up) if brought up to such a high temperature in
air, an inert gas (argon) is used to purge the splice chamber of oxygen. In order to keep the fibers clean and
improve splice strength, the purging gas is set to flow over the fibers at a fairly high rate during the fusion process.
The fiber ends are allowed to heat up before they are pushed together. This smoothes over any discontinuities in
the fiber ends and also increases the plasticity of the glass. The hot fibers are then pushed together, producing a
splice with low loss and high strength. The splice properties can be edited in the Splice Property window, which
can be accessed through Menu Bar, Splice, Splice Parameters, or by right-clicking on Splice Parameters.
Summary of Contents for Vytran LFS4100
Page 1: ...LFS4100 Fiber Splicer User Guide...
Page 44: ...www thorlabs com...