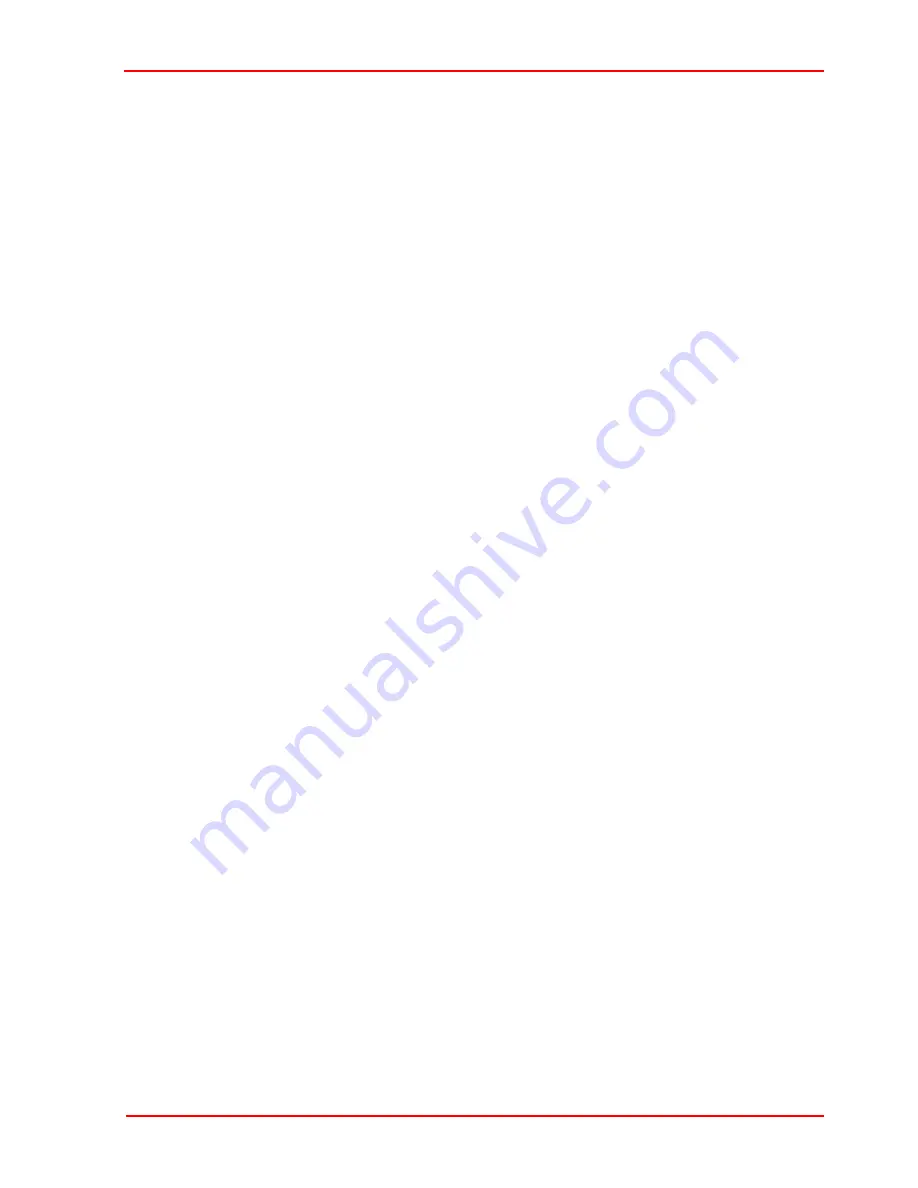
Rev 22 Feb 2019
Page 27
Chapter 5 Troubleshooting
Appendix B Calculating the Power Dissipation
B.1 Motor Heatsink
The power dissipated in the motor can be estimated by measuring the RMS current
drawn from the PSU and then using the following equation:
P
mot
= R
mot
x [(I
rms+
+ I
rms-
- I
q+
- I
q-
) / 2]
2
Where P
mot
is the power dissipated in the motor, R
mot
is the motor coil resistance
(2.2
Ω
), I
rms+
is the rms current drawn from the positive supply rail, I
rms-
is the rms
current drawn from the negative supply rail, I
q+
is the quiescent current drawn on the
+ve rail (0.15A under all circumstances) and I
q-
is the quiescent current drawn on the
-ve rail (0.10A under all circumstances).
The power dissipated in the driver boards can be calculated using the following equation:
P
drv
= (V
+
x I
rms+
) + (V
-
x I
rms-
) - Pmot
Where P
drv
is the power dissipated in the driver boards, V
+
is positive supply voltage
and V
-
is the negative supply voltage.
2.1.1 Calculating the Required Thermal Conductivity
The ability of a heatsink to transfer heat to its surroundings is parameterised either by
its thermal conductivity, k or its thermal resistance, Ø. The lower the thermal
resistance the more effectively the heatsink can transfer heat. The required thermal
resistance can be calculated from the following equation:
Ø = 1/k = (T
hs
- T
a
) / P
max
In the above equation T
hs
is the maximum permissible heatsink temperature, T
a
is the
ambient temperature and P
max
is the maxium power the device being cooled will
dissipate. For the motors it is desireable to keep T
hs
below 45°C.
The following equation can be used to calculate T
hs
for the driver IC:
T
hs
= T
j
- P
max
x Ø
jhs
Here, Ø
jhs
is the thermal resistance between the semiconductor junction of the power
amplifier IC and the heatsink. T
j
is the maximum temperature allowable at the
junction, about 150°C (although the lifetime of the driver IC will be longer if the junction
is kept at a lower temperature). The value of Ø
jhs
is 1.3 °C/W.
Summary of Contents for GVS001
Page 33: ...Rev 22 Feb 2019 Page 31 Chapter 5 Troubleshooting D 2 CE Certificates ...
Page 34: ...Page 32 18728 D01 Single and Dual Axis Scanning Galvo Systems for Small Beam Diameters ...
Page 35: ...Rev 22 Feb 2019 Page 33 Chapter 5 Troubleshooting ...
Page 36: ...Page 34 18728 D01 Single and Dual Axis Scanning Galvo Systems for Small Beam Diameters ...
Page 37: ...Rev 22 Feb 2019 Page 35 Chapter 5 Troubleshooting ...
Page 38: ...Page 36 18728 D01 Single and Dual Axis Scanning Galvo Systems for Small Beam Diameters ...
Page 39: ...Rev 22 Feb 2019 Page 37 Chapter 5 Troubleshooting ...
Page 41: ...www thorlabs com ...