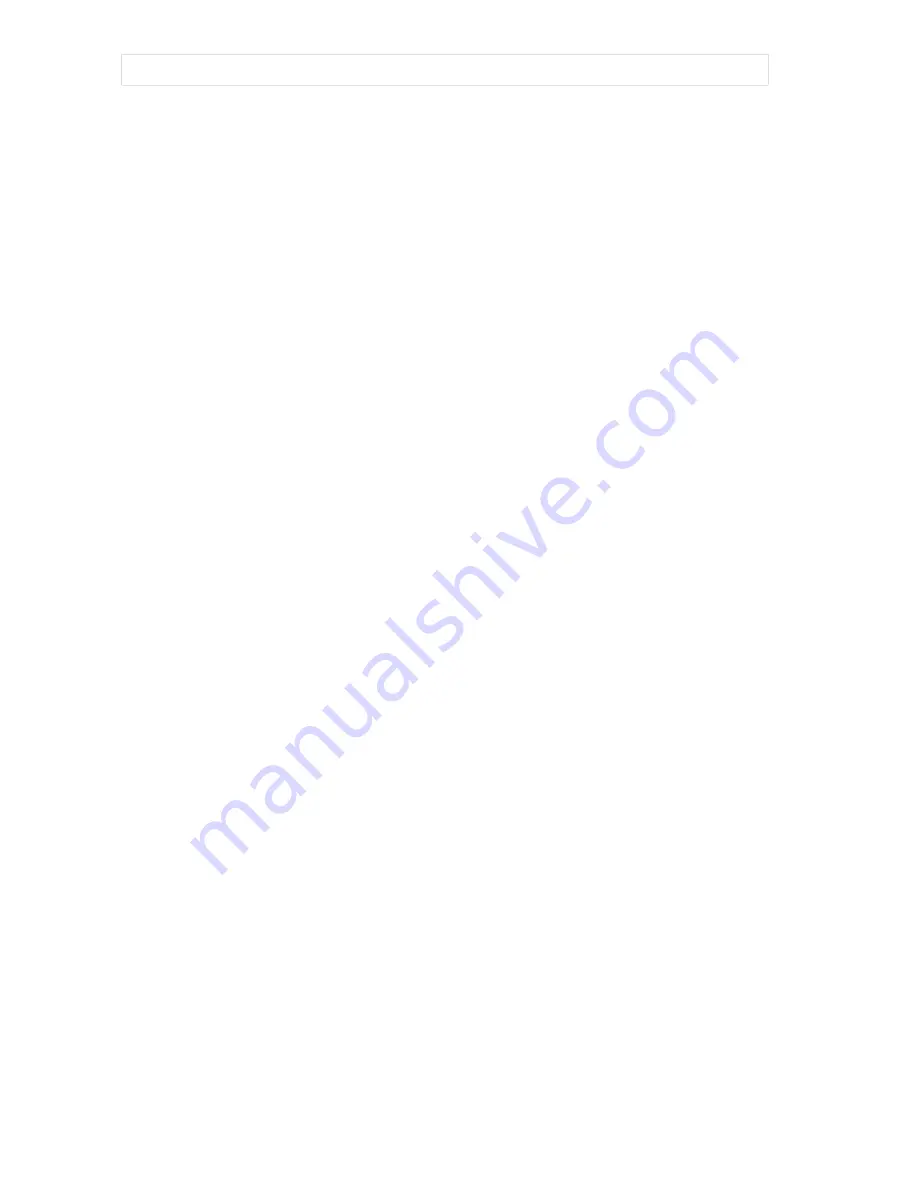
Thoreson-McCosh Inc
EDITION 05/07/10
21
IB201001.doc
SECTION 10 MAINTENANCE
SECTION 10.1 FILTERS
The process and regeneration filters should be checked weekly and cleaned with
compressed air or replaced if necessary.
Remember to check the filter gasket and fix or replace as needed.
SECTION 10.2 LUBRICATION
The regeneration blower motor bearings may be lubricated every 6 months to extend
blower life. A couple drops of S.A.E. 20 motor oil at each of the two motor bearings is
recommended.
SECTION 10.3 MOLECULAR SIEVE TEST
When it is suspected that the molecular sieve needs replacement, there is a simple test
that can be performed. A positive test does not ensure that the molecular sieve is in good
condition. If there is a large percentage of broken pellets or dust, contamination from
foreign matter, or most of the pellets are discolored, the desiccant should be replaced.
New desiccant is light tan in color.
To test the desiccant’s effectiveness, a sample should be regenerated in an oven at 600°F/
316°C for about two hours. At the end of that period, place the desiccant into an air tight jar
and allow it to cool down to room temperature for a minimum of 12 hours. Pour 30ml of
water into a small glass. Determine and record the temperature of the water using a
mercury thermometer. Into a similar dry glass, pour a quantity of desiccant that is 10%
greater by volume than the water (33ml). Dry the thermometer and place it into the glass
containing molecular sieve. W ith one quick motion, pour the water into the glass of
desiccant. Observe the increase in temperature of the mixture while stirring with the
thermometer and record the peak temperature. This will occur in about 20 to 30 seconds.
Subtract the water temperature from peak temperature observed. If the temperature
difference is 40°F/ 4°C or greater, the sieve is in satisfactory condition.