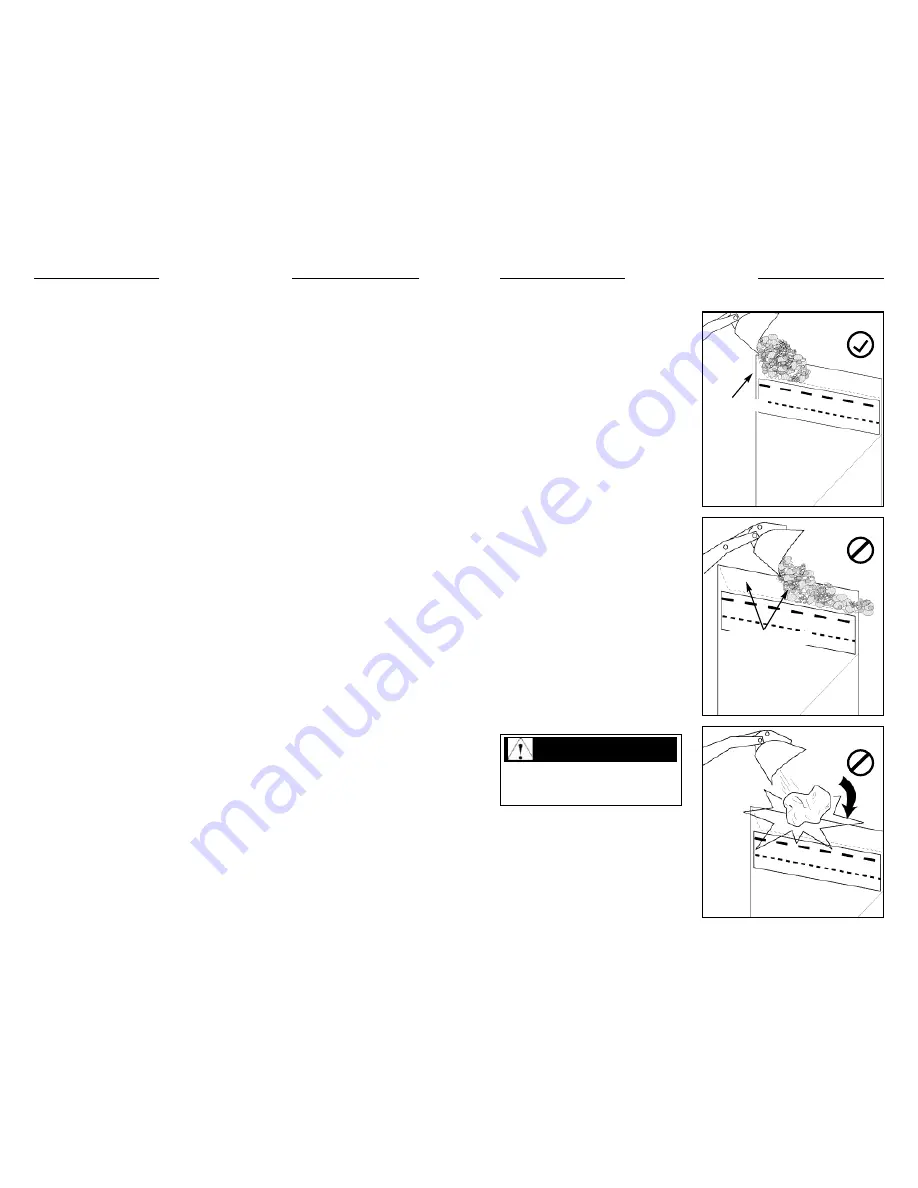
23
22
3.5B Loading Procedure
When loading material into the hopper,
keep the bucket as low as possible (fig.
S0010). Allow the material to slide down
the high side of the hopper plate onto the
top screen deck.
Check tailings for size. If you find good
material mixed in with the tailings, try
slowing the feed rate (dump) into the hop-
per.
Dumping the material further down the
deck wastes processing area (fig. S0011).
This will allow good material to flow off
with the tailings.
Use extra care when placing large
heavy objects on the top screen deck. Make
sure smaller material is in front of the load
before lowering onto the top screen deck.
This will provide some cushion effect.
Never drop large heavy objects directly
onto the top screen deck (fig. S0012).
Immediate damage to the wire screen cloth
or shaker assembly may occur.
Keep an eye on tailings and finished
product. Do not allow to build up around
the shaker deck area. Retrieve product
before excessive build up around the shaker
area.
S0010
S0011
S0012
Hopper high side
Wasted processing area
Large objects may roll uncon-
trollably off the top screen deck.
Assure the area where tailings are
being discharged has adequate run off
area.
WARNING
3.5 OPERATING PROCEDURES
Follow the set up procedures outlined
previous to this section.
This section contains important infor-
mation for getting the best performance
and efficiency from your machine.
3.5A. General
The shakerhead assembly contains two
sorting surfaces called screens. Certain
application will require you to change
screen sizes for best results. There are a
number of screen sizes, and multiple com-
binations are available to sort varied mater-
ial. Proper screen sizing makes this a truly
multipurpose and efficient machine, able to
handle fine sands, rock, wood product
refuse, etc.
The basic rule of thumb for screen siz-
ing is a 3 to 1 ratio, top to bottom respec-
tively. Example: 3’’ (76mm) top screen,
1’’ (25mm) bottom screen. However, in
some cases, it may be more efficient to run
the material through a larger screen combi-
nation first, then changing the screens to
obtain the final product size. This would be
desirable when the material being sized
clogs the screens or feed rate becomes
excessively slow.
The most common type of screen mate-
rial is called “wire cloth”. Various diame-
ters of wire are overlaid together to make
varied openings. The actual diameter of the
wire used dictates the surface area of the
hole.
Example: A screen 2’’ square, using a
0.25 wire diameter would have a larger
hole opening than a 2’’ square using 0.50
wire diameter. The smaller diameter screen
will be more efficient, due to the larger
open area, but screen life will also be short-
er. A larger wire diameter material will
wear longer.
Wire cloth screens may be ordered in
square or rectangular (slotted) pattern.
Select the proper screen for your applica-
tion. A slotted pattern will process material
faster, though larger material will slip
through.
See Section 6 for more screen size
information.
3. OPERATION
3. OPERATION
Summary of Contents for ProTough 300 Screener
Page 1: ...Owner s Operator s Service and Parts Manual Publication No 52812 September 2005 300 Screener...
Page 7: ...11 2 CONTROLS 10 Engine Controls 2 1 Hydraulic and Axle Controls 2 2...
Page 39: ...75 74 7 WARRANTY INFORMATION Machines Purchased Through Thomas Dealers 7 1...
Page 63: ...123 122 8 4 ELECTRICAL Engine Electrical 8 4 1 Chassis Electrical 8 4 2...