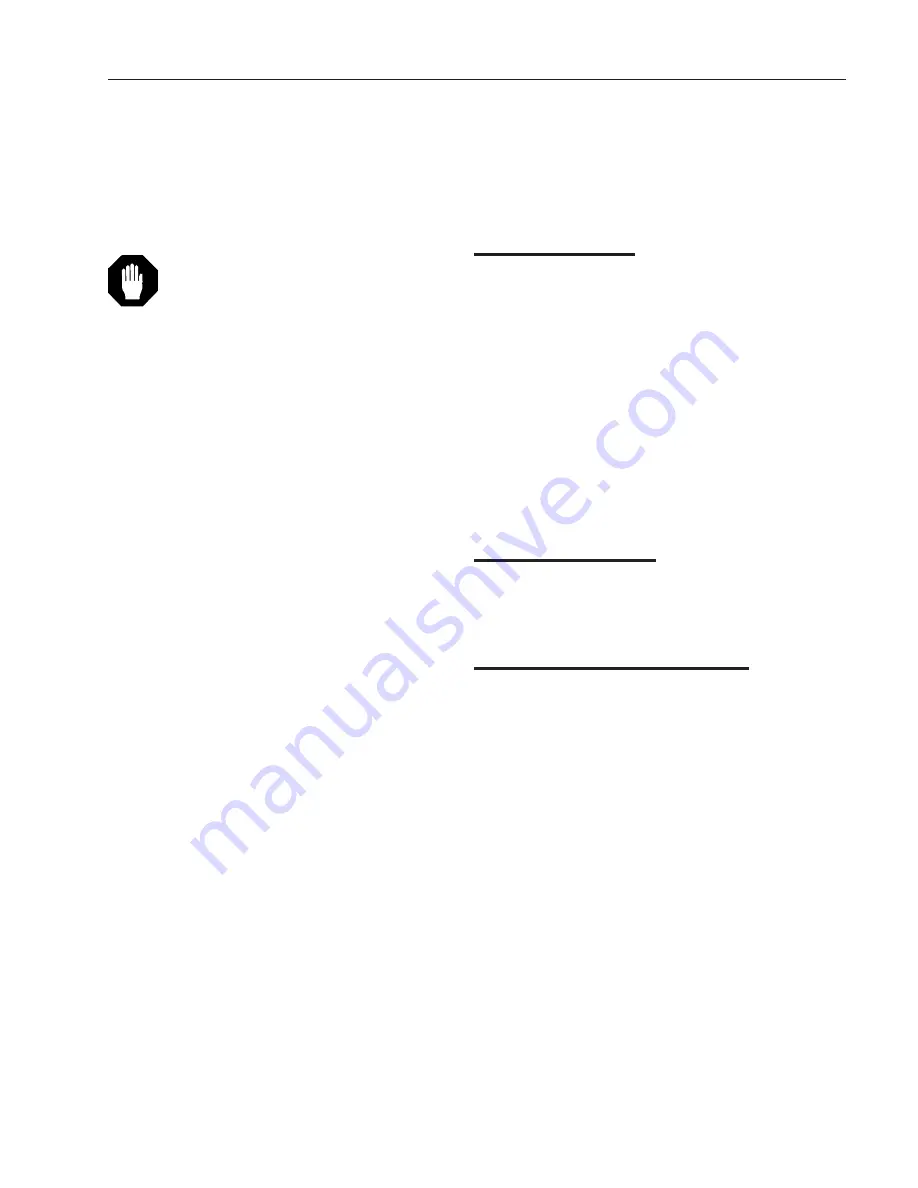
Intended Use
The 5300A20/F48025-TS or 5300A25/F48025-80-TS
furnace is a general purpose laboratory and heat treat-
ing furnace. For optimum element life, Thomas
Scientific recommends observing these temperature
ranges: from 100°C (212°F) to 1093°C (2000°F) contin-
uous use or from 1093°C (2000°F) to 1200C (2192°F)
for intermittent use. Continuous use is operating the
furnace for more than 3 hours and intermittent use is
operating the furnace for less than 3 hours.
All furnaces consist of: 1) a vented heating chamber;
2) a temperature controller; and 3) a door safety switch
for operator safety.
General Usage
Do not use this product for anything other than its
intended usage.
Principles of Operation
The furnace chamber is heated by open coil electric
resistance elements and is insulated with ceramic fiber
insulation. The controller is located under the furnace
chamber and is well insulated from the heat generated
in the furnace chamber. A door safety switch removes
power to the heating elements whenever the furnace
door is opened. The temperature is controlled by one
of three types of controllers.
5
Introduction
Caution
Do not exceed operating temperatures
shown in “General Specifications.”
Exceeding these limits will result in
severely reduced element life.
Summary of Contents for 5300A20/F48025-TS
Page 40: ...40 Wiring Diagrams SINGLE SETPOINT CONTROL W OTP...
Page 41: ...41 WIRING DIAGRAMS 8 SEGMENT PROGRAMMABLE CONTROL...
Page 42: ...42...
Page 43: ...43...