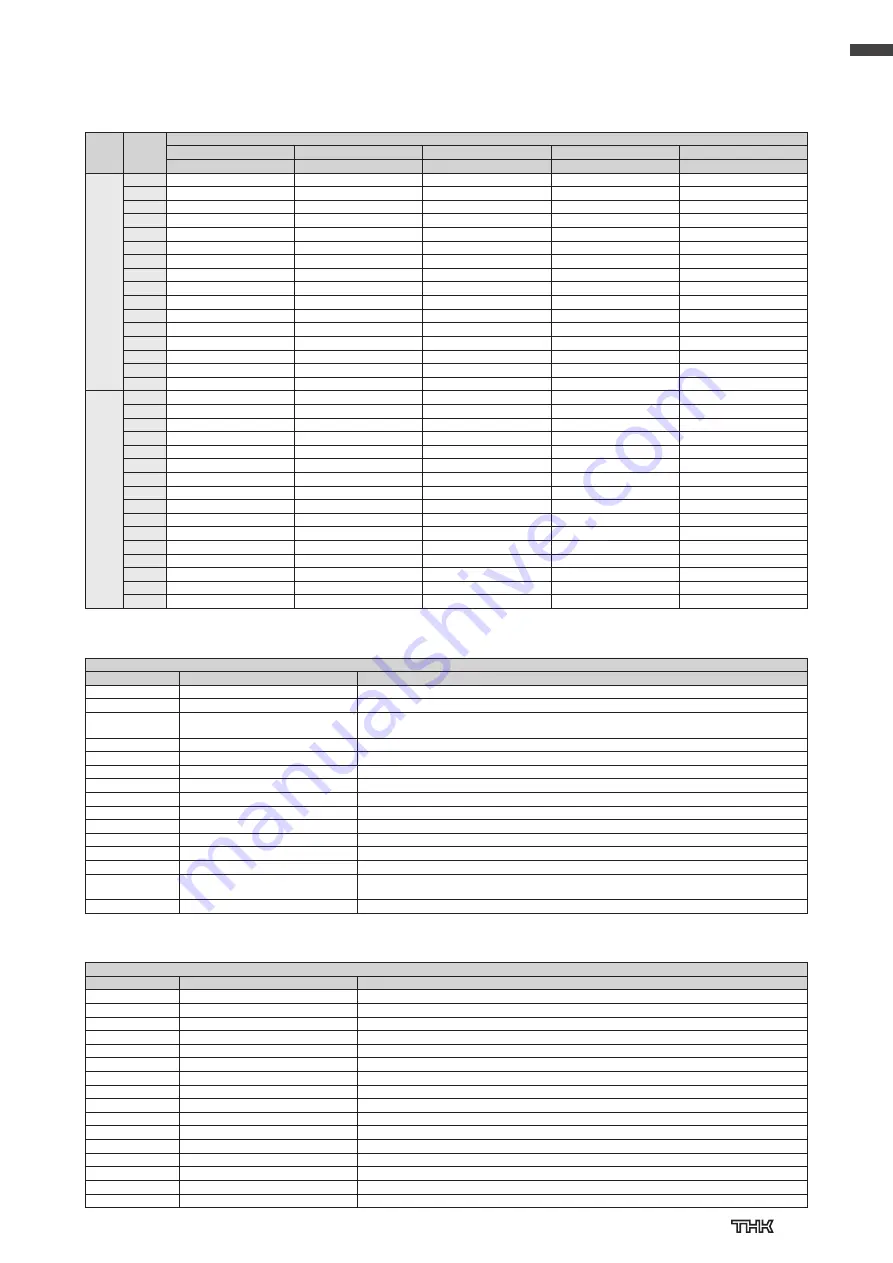
TSC
I/O
CN1
pin
number
Signal name
Function mode 0
Function mode 1
Function mode 2
Function mode 4
Function mode 5
64-position mode
External input teaching
256-position mode
Solenoid mode 1
Solenoid mode 2
Input
3
PI 0
PI 0
PI 0
ST 0
ST 0
4
PI 1
PI 1
PI 1
ST 1
ST 1
5
PI 2
PI 2
PI 2
ST 2
ST 2
6
PI 3
PI 3
PI 3
ST 3
—
7
PI 4
PI 4
PI 4
ST 4
—
8
PI 5
PI 5
PI 5
ST 5
—
9
—
MODE
PI 6
ST 6
—
10
—
JOG/INCHING
PI 7
—
-
11
SENSOR
SENSOR
SENSOR
SENSOR
SENSOR
12
BKRL
JOG N
BKRL
BKRL
BKRL
13
STRT
STRT/PWRT
STRT
—
-
14
MANU
MANU
MANU
MANU
MANU
15
HOME
HOME
HOME
HOME
HOME
16
PAUSE
PAUSE
PAUSE
PAUSE
PAUSE
17
REST
REST
REST
REST
REST
18
SV–ON
SV–ON
SV–ON
SV–ON
SV–ON
Output
19
PO 0
PO 0
PO 0
PE 0
LS 0
20
PO 1
PO 1
PO 1
PE 1
LS 1
21
PO 2
PO 2
PO 2
PE 2
LS 2
22
PO 3
PO 3
PO 3
PE 3
—
23
PO 4
PO 4
PO 4
PE 4
—
24
PO 5
PO 5
PO 5
PE 5
—
25
MOVE
MOVE
PO 6
PE 6
—
26
AREA
MODES
PO 7
AREA
AREA
27
P AREA
P AREA
P AREA
P AREA
P AREA
28
MANU S
MANU S
MANU S
MANU S
MANU S
29
HEND
HEND
HEND
HEND
HEND
30
INPS
INPS
INPS
INPS
—
31
LOAD/TRQS
WEND
LOAD/TRQS
LOAD/TRQS
—
32
SVRDY
SVRDY
SVRDY
SVRDY
SVRDY
33
EMGS
EMGS
EMGS
EMGS
EMGS
34
ALM
ALM
ALM
ALM
ALM
Pin Assignment by TSC Function Mode
Input
Signal name
Details
Notes
MANU
Run mode
Switch between AUTO/MANUAL from I/O. ON for MANUAL, OFF for AUTO.
STRT
Start
Program step start signal. ON to start program.
PI 0 to PI 7
Command position number
Input for position number designation. Program designation by signal level.
Select program step and start program with “STRT” signal.
PAUSE
Temporary stop
Temporarily suspend operation. OFF for PAUSE input state (N.C. contact specification).
HOME
Home return
Start home return operation. ON to start home return.
SV–ON
Servo ON
Turn servo on and off. ON to turn servo on, OFF to turn servo off.
REST
Alarm reset
Reset the alarm. Reset remaining travel amount when paused. ON to reset.
BKRL
Break release
Force release the brake. ON to release brake.
MODE
External input teaching mode
Change to teaching mode. ON for teaching mode.
PWRT
In external input teaching mode: Write current position Designate the position and turn this signal on for 20 ms or more while in teaching mode to write position.
JOG/INCHING
In external input teaching mode: Switch manual movement Switch manual movement mode while in teaching mode. Movement is INCHING when ON, movement is JOG when OFF.
JOG P
In external input teaching mode: Movement dir Movement direction and start signal when in teaching mode. ON to move to each soft limit in + direction, OFF when moving for deceleration stop.
JOG N
In external input teaching mode: Movement direction - Movement direction and start signal when in teaching mode. ON to move to each soft limit in - direction, OFF when moving for deceleration stop.
ST 0 to ST 6
Cylinder type START
Program start signal for position numbers ST 0 through ST 6. You can select level or edge for signal with Parameter No. 13
“Movement command method.” Furthermore, when two or more signals are ON simultaneously, the lesser value will be prioritized.
SENSOR
Sensor input
The input signal when sensor input is selected for home return method.
Input Signal Function Details
Output
Signal name
Details
Notes
MANU S
Run mode status
Run mode output (AUTO/MANUAL) ON for MANUAL, OFF for AUTO.
PO 1 to PO 7
Complete position number
Outputs position number after positioning is completed (binary output).
MOVE
Moving
Signal output when motor is running.
INPS
Positioning finished
This is output when the motor enters the positioning completion boundary.
SVRDY
Run prep complete
This signal is output when the servo is ON.
ALM
Alarm
Alarm output signal.
MODES
External input teaching mode status Teaching mode/normal run mode output judgment signal. ON for teaching mode. OFF for normal run mode.
WEND
Write completed
Once writing through PWRT signal is complete, this signal turns on for 30 ms.
HEND
Home return completed
Output signal when home return operation is completed.
AREA
Area upper limit/lower limit
ON when actuator’s current position is within the set range of the parameter.
P AREA
Position area
ON when actuator’s current position is within the set range of the program step.
EMGS
Emergency stop state
Judgment output for emergency stop input. ON when in normal state, OFF when emergency stop circuit is broken.
LOAD
Load output judgment status
ON when specified torque exceeds threshold for a set amount of time within judgment range.
TRQS
Torque level status
ON when load threshold is reached while moving. OFF when below load threshold.
PE 0 to PE 6
Cylinder type arrival complete output This signal is output after position number operation is completed.
LS 0 to LS 2
Cylinder type position detection output This signal is output once all current positions (3 points) enter the positioning range.
Output Signal Function Details
22
Summary of Contents for ET20 Series
Page 26: ...MEMO 25...