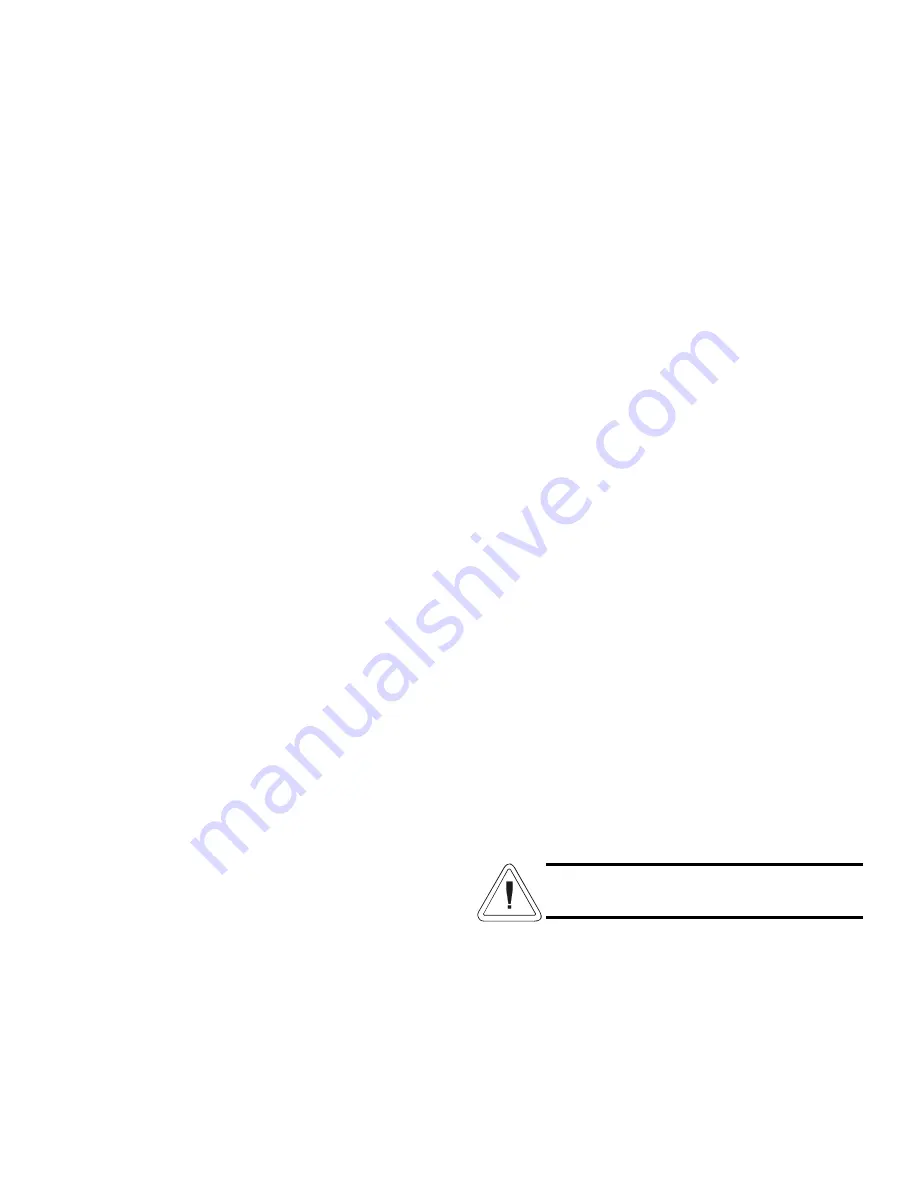
Section 3 - Operation
3.1 Description
The Steri-Cult Series CO
2
incubator provides perfect cul-
ture conditions in a state-of-the-art, microprocessor controlled
incubator. During operation, the chamber air is drawn through
the top diffuser pan and into the chamber outlet duct where it
passes over a temperature probe. The temperature controller
then cycles the heaters which surround the incubator chamber.
Next, the air passes through the blower and onto a micro-
biological filter. The filter scrubs the circulating air, trapping
spores and other airborne contaminants. The “scrubbed” air
exits the filter and continues along the sensing/conditioning
path. A sample of this air is routed through the infrared CO
2
sensing unit where precise CO
2
levels are monitored.
Periodically, the Air Inject solenoid opens, allowing fil-
tered outside air to pass across the IR sensor. This serves as an
Auto-Zero to eliminate possible sensor or electrical component
drift. During this time, the CO
2
inject solenoid will not cycle.
Signals from the IR sensor are sent to the CPU Board where
they are compared to the CO
2
setpoint. If a difference exists
between the actual value and the setpoint, the microprocessor
computes the appropriate solenoid on/off times. This creates a
proportional CO
2
controller when the actual value is within 1%
of setpoint.
The recirculated chamber air continues into the humidity
reservoir. The air passes below the water level and is humidi-
fied as it bubbles through the water. The microprocessor looks
at the air temperature and selected humidity level and calculates
the necessary water temperature required to obtain the desired
RH. Water in the reservoir is heated by an external heater and
the temperature is monitored by an immersed temperature
probe.
Note:
The Steri-Cult incubators are designed to minimize the
amount of condensation on the glass door. However, the units
are not condensate-free, specifically if the chamber interior is
operated above an absolute RH average of 85%. It is normal to
have a small amount of condensate form across the bottom and
in the corners of the glass door if the RH setpoint is equal to or
greater than 90% RH.
No attempt to control RH will occur until the chamber
temperature is within 1°C of setpoint. During this time the
value displayed in the RH Control module will be “—”. The
RH recorder output will be the RH setpoint value.
The humidified and CO
2
enhanced air then passes across
another heater which is controlled by a third temperature probe.
The purpose of this heater is to restore lost heat to the air before
entering the chamber.
Air enters the chamber beneath the bottom diffuser pan and
is forced up through the holes into the chamber.
When the outer door is opened, power to the heaters, CO
2
inject solenoid and humidity reservoir is interrupted.
When the outer door is closed, power is restored.
3.2 Power Control Panel (Figure 3-1)
The Power Control Panel houses the Main Power switch,
Program/Run key switch, Door Ajar light (red), Sample Port
and Adjustment Screwdriver.
a. Main Power Switch
The Main Power switch controls all electrical power to the
incubator. The switch must be on for any of the incubator sys-
tems to be functional.
b. Program/Run Key Switch
The Program/Run key switch determines the operating
mode of the incubator.
When the switch is set to Program, the operator may set
the chamber temperature, relative humidity and CO
2
.
When the switch is set to Run, the programmed setpoints
are locked. The setpoints may be viewed but not changed.
c. Door Ajar Light
The red Door Ajar light warns that the outer door is open
or has not been securely closed.
When the Door Ajar light is on, power to the heaters and
the CO
2
injection solenoid is interrupted.
d. Sample Port
The Sample Port is used to draw a sample of chamber
atmosphere so CO
2
content may be measured by an independent
source.
For proper operation and to prevent CO
2
loss, the
sample port must be capped when not in use.
Model 3033 and 3860 Series _______________________________________________________________Operation
3 - 1
Artisan Technology Group - Quality Instrumentation ... Guaranteed | (888) 88-SOURCE | www.artisantg.com
Summary of Contents for 3033
Page 6: ...Artisan Technology Group Quality Instrumentation Guaranteed 888 88 SOURCE www artisantg com ...
Page 8: ...Artisan Technology Group Quality Instrumentation Guaranteed 888 88 SOURCE www artisantg com ...
Page 33: ...Artisan Technology Group Quality Instrumentation Guaranteed 888 88 SOURCE www artisantg com ...
Page 37: ...Artisan Technology Group Quality Instrumentation Guaranteed 888 88 SOURCE www artisantg com ...
Page 41: ...Artisan Technology Group Quality Instrumentation Guaranteed 888 88 SOURCE www artisantg com ...
Page 45: ...Artisan Technology Group Quality Instrumentation Guaranteed 888 88 SOURCE www artisantg com ...