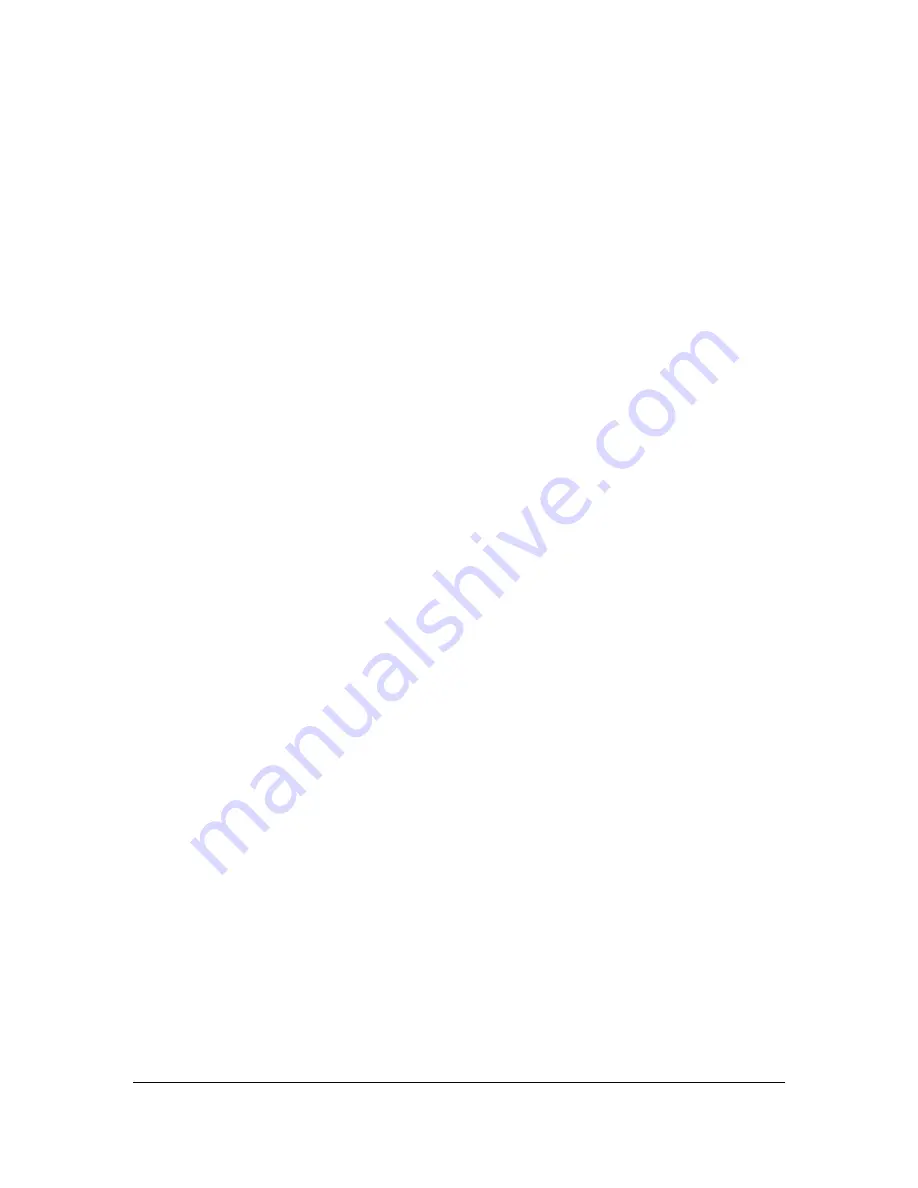
5
Undo the four screws at the corners of the housing. The control electronics are mounted on the
enclosure cover. Using proper fixing, the controller enclosure can be screwed to the wall with
cable entry grommets downwards.
Caution:
Controller wiring should only be done when the unit is not energized. It is possible to
damage the control unit if it is assembled under voltage. Miniaturized terminal blocks are used for
making wiring connections. The wire is held in place within the terminal with a screw that provides
excellent contact without damage to the wire.
Cable Connection:
A small blade screwdriver may be used to fasten miniaturized terminal
block screws while the corresponding wire is inserted.
Use up to an 18 AWG stranded wire to connect the sensor cables to the unit. The
KS
terminal
should be connected to the
collector sensor
(higher temperature); the
BS
terminal is designated
for the
return sensor
(lower temperature).
ower Connections:
A small blade screwdriver may be used to fasten miniaturized
terminal block screws while the corresponding wire is inserted.
NOTE 1:
Always disconnect the controller from power supply before opening the housing.
NOTE 2:
The controller should be properly grounded.
Flexible wires, 18/3 AWG
(gauge/conductor), simplify connection to the terminals.
The power terminal block will
accommodate wire sizes to 14 AWG. All other connections should be secured and adequately
tightened, as loose power connections will over-heat, and may cause fire.
NOTE 3: It is important that the specified output loads (245 Watts) are not exceeded. Where
these loads expect to exceed, external relays must be used. Always keep power cables away
from sensor cables and other low voltage signal cables.
NOTE 4: To protect against lightning damage, the system must be grounded according to local
regulations. Sensor failures due to the weather or electrostatic are mostly due to poor grounding.
ROUBLESHOOTING
Problem:
Nothing happens when unit is powered-up.
Cause/Remedy:
The fuse could be blown – check and replace if necessary. If the fuse blows
again, then the pump draws more current than the unit is design to supply. Use an auxiliary relay
or contact your product supplier.
Problem:
One or more LED’s is fluctuating.
Cause/Remedy:
This indicates a system alarm warning, which may be caused by a sensor fault:
•
Lower Collector LED blinks
è
Collector sensor cable is short circuited
•
Lower Storage Tank (70
o
F) LED blinks
è
Return sensor cable is short circuited
•
Upper Collector LED blinks
è
Collector sensor cable is open
•
Upper Storage Tank (200
o
F) LED blinks
è
Return sensor cable is open
P
T