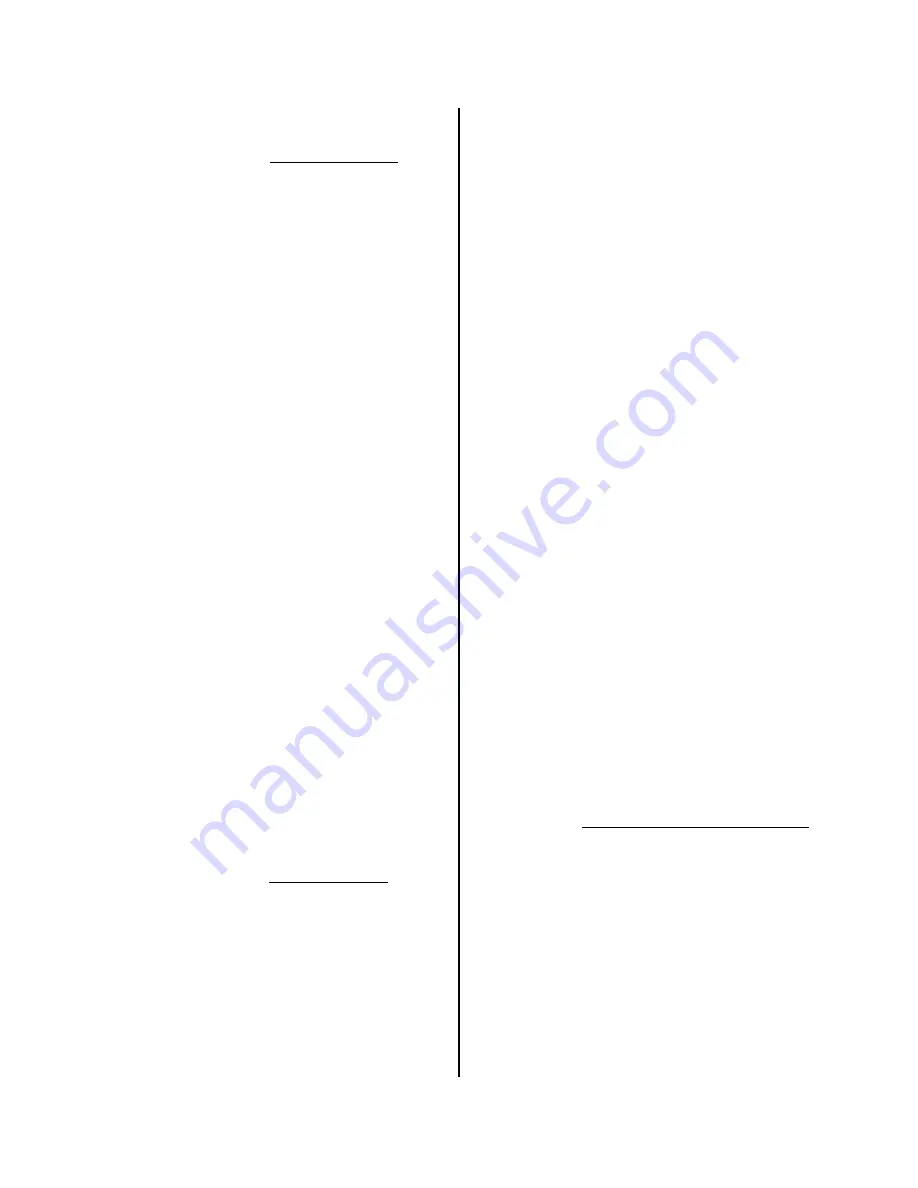
All installations and services must be performed by qualified service personnel.
6
Piping from the propane tank to the furnace must follow
the recommendations of the gas supplier. In the
absence of local codes governing gas piping selection
and installation, follow the National Fuel Gas Code,
ANSI Z223.1 / NFPA 54-1999, or latest edition.
A readily accessible, manual gas shutoff valve (design-
certified for the applicable gas) with a non-displaceable
rotor member shall be installed within six (6) feet of the
furnace.
A pipe union, or flanged connection, shall be provided
directly up stream of the burner to allow burner removal.
Unions must be of a ground joint type or flange-jointed
type using a gasket resistant to the corrosive effects of
LP gases. Pipe dope or sealant design-certified to be
resistant to the action of the LP gases should be used on
all threaded joints.
The burner is setup to be piped to the gas supply
through the right or left-hand side of the furnace. For
service purposes, it is recommended the gas union be
located inside the furnace.
A drip leg must be used on both propane and natural
gas installations immediately upstream of the furnace in
order to trap oil, condensate, and other impurities which
might otherwise lodge in the gas valve, or plug the main
burner orifice. A drip leg shall be provided at the outlet
of the gas meter when there is excessive condensation
between the gas meter and the furnace.
Failure to install drip leg(s) may void the manufacturer’s
limited warranty on the furnace.
For natural gas, the maximum supply pressure is 14.0 in.
W.G. and the minimum supply pressure, for purposes of
input adjustment, is 5.5 in. W.G.
For propane gas, the maximum supply pressure is 14.0
in. W.G. and the minimum supply pressure, for
purposes of input adjustment, is 11.0 in. W.G.
ELECTRICAL WIRING
c
CAUTION:
When testing electrical equipment,
always follow standard electrical procedures and
precautions.
A Separate power supply from all other circuits is
needed, it should be no smaller than 14 Ga., insulated
copper wire with a temperature rating of 60ºC, or
greater. Install current protection and disconnect. All
electrical wiring must be installed in strict accordance
with local ordinances and codes. In the absence of local
ordinances and codes, all electrical wiring must conform
to the requirements of the National Electric Code,
ANSI/NFPA 70- latest edition.
Remove the Furnace Control Box Cover. Route the
Power Supply Lines through the knock out in the left side
casing with a conduit connector or proper connection.
Connect the power supply L1 (Hot) line to the Black wire
labeled LI. Connect the power supply L2 (Neutral) to the
white wire labeled L2. Connect the Power Supply
Ground wire to the Green Wire. Secure all connections
with the yellow wire nuts provided.
Refer to the electrical diagrams contained in Appendix B
of this manual for an electrical schematic, a connection
diagram, and operating instructions.
Room Thermostat
A room thermostat must be connected to the Furnace
control. This is typically a low voltage (24 VAC) circuit.
Consult the National Electrical Code, ANSI/NFPA 70-
2017, or latest edition for guidelines for proper wiring
methods and materials for this circuit. The room
thermostat should be located on an interior wall in the
natural circulating path of the room air.
The thermostat should
not
be installed in a location
where it is directly exposed to,
cold air infiltration, i.e. drafts from outside
openings such as windows and doors,
air currents produced by supply air
registers, and
heat from a nearby source, such as a
fireplace, electrical appliances, lamps, solar
radiation, a wall enclosing warm air ducts, a
chimney, or a flue gas vent.
Most room thermostats are equipped with an
adjustable heat anticipator, set the thermostat
heat anticipator to match the control current of
the furnace as indicted on the furnace wiring
diagram.
INITIAL START UP:
This furnace does not have a pilot. It is
equipped with a hot surface igniter, which
automatically lights the burner. Do not attempt
to light the burner by hand. Check the following
items before the initial start-up.
1. Check all wiring for proper hook up. Tighten
any loose connections.
2. Using a soap solution, leak test gas piping
connections.
3. Check all tubing connections to the pressure
switch, inducer, burner box, and gas valve
and make sure they are connected firmly at
all their connection points.
4. Check flue pipe, combustion air inlet, and all
joints for tightness and to make sure there
is no blockage.
5. Make sure air filter is in place.
6. Make sure the outside vent and air intakes
are installed according to instructions and
are free from blockage.
INTIAL OPERATION OF THE FURNACE:
INTIAL START UP
c
WARNING:
Turn off power to furnace before it is
placed into service. The gas piping system must
have been leak tested by a qualified heating
contractor.
c
WARNING:
It may be necessary to purge the air
out of the gas line for initial start-up of the furnace
after installation. A qualified heating contractor
should do this. If excessive gas escapes when
purging the gas supply at the union, allow the area
to ventilate for at least 15 minutes before attempting
to start the furnace. Propane gas is especially
dangerous because the specific gravity of propane
gas allows it to accumulate at floor level at a
dangerous concentration.
Summary of Contents for GMA1-60D48N
Page 2: ......
Page 19: ...All installations and services must be performed by qualified service personnel 17 GMA1 SERIES...
Page 20: ...All installations and services must be performed by qualified service personnel 18 GMC1 SERIES...
Page 21: ...All installations and services must be performed by qualified service personnel 19 GMC1 SERIES...