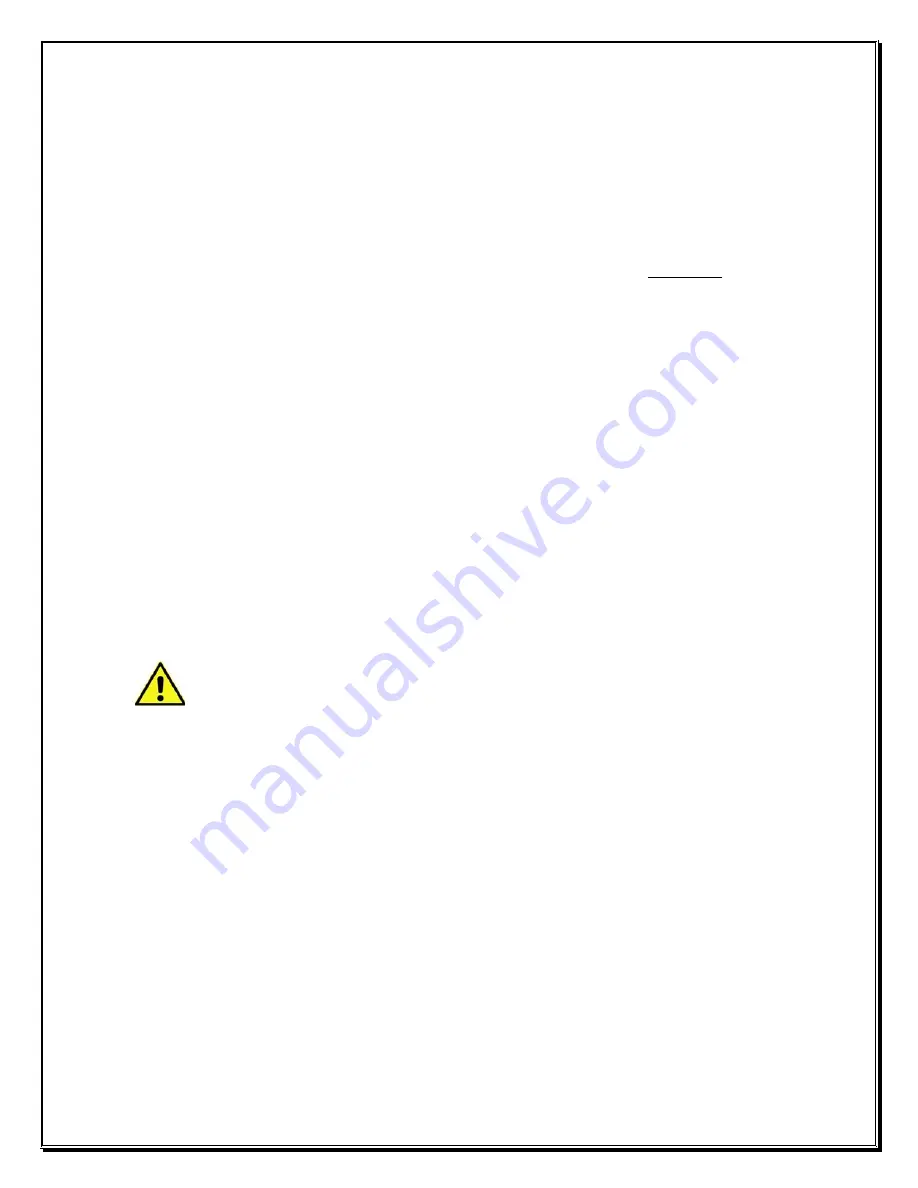
AIR FLOW PATTERN
An Oven Air Flow Pattern drawing for this oven is included in this manual. The exhaust
is top and bottom with the inlet in the middle. The main plenum protects the working
chamber from direct radiation from the heating elements. The secondary plenum adds
turbulence and prevents the air from directly recirculating. The secondary plenum also
protects the operator from coming in direct contact with the blower wheel.
Air uniformity will be affected by large specimens and/or load trains. The amount of air
reaching the front of the oven will be reduced by larger specimens. CAUTION: Do not
block the air flow inlet or exhaust. This will restrict air flow and affect the uniformity of
the oven and may damage the elements.
COOLING OPTION
1.
C02 systems have a single injector assembly. An extra injector assembly will be
present at the bottom if conversion to LN2 medium is required. The solenoid
valve provided will be set up for either 300 or 1000 psi service per your order. A
1/4" compression fitting is provided for your connection. This can be found on
the rear feed through panel.
2.
LN2 systems have dual injectors plumbed from one solenoid valve. The dual
injectors allow the lower pressured LN2 to be distributed evenly. Normal supply
pressure from a 160 liter liquid exceller tank is approximately 25 psi.
VENTILATION
It is
IMPORTANT
to have adequate ventilation when using C02 or LN2.
A vent hood may be necessary.
SHUT DOWN PROCEDURES FOR OVENS WITH COOL DOWN BLOWERS:
CAUTION!
Do not shut the blower off until the oven has cooled down.
Change to the controller set point down to 100° F. Allow the oven to cool down to
100° F then switch the power button to the off position.
For conducting service work, follow your companies log out/ tag out procedure.