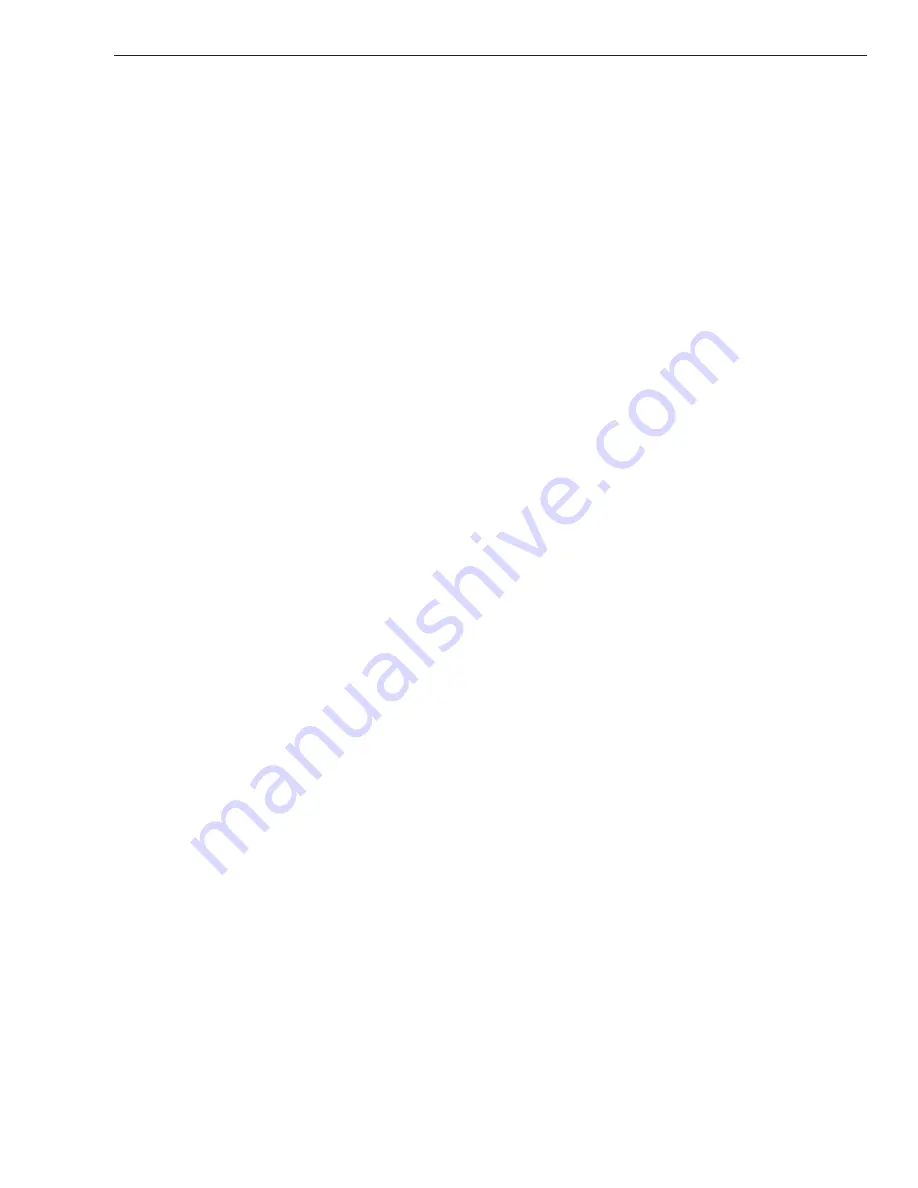
cutmaster 82
Manual 0-4980
5-11
SERVICE
9. Close torch switch (Pendant switch or activate
CNC Start) to establish a pilot arc. Bring torch to
within 1/8” – 3/8” of the work piece to establish
main cutting arc.
10. While cutting keep the torch switch closed and
bring the torch off the edge of the material.
• Pilot Arc re-ignites immediately
11. Open the torch switch
• DC LED turns off
After 20 second post flow time
• Gas solenoid closes
• Gas flow stops
12. Set the FUNCTION CONTROL SWITCH to
LATCH mode
13. Start a cut, and release the torch switch
• Main cutting arc will remain on until the torch
is lifted away from the plate approx ¾” or until
the torch is brought off the edge of the metal
Once the arc has extinguished
• DC LED turns off
After 20 second post flow time
• Gas solenoid closes
• Gas flow stops
This completes the Main Arc and Controls Test. If the
above are all correct then proceed to the next section
"H CNC Interface Test." If the unit does not function as
stated above, then note the symptom and proceed to
Section "5.09, Main Arc and Controls Problems".
H. CNC INTERFACE TEST
If the unit has one of the two factory supplied options
for CNC interface installed, proceed with this section,
otherwise the tests are complete.
1. Connect an ohmmeter between J2-12 to J2-14
(START signal). Position the torch to pilot. Check
the OK-TO-MOVE signal by connecting a jumper
between J2-3 and J2-4 (START signal).
• Pilot arc is established
2. Bring the torch to the work piece and transfer to
cutting arc.
• OK-TO-MOVE signal is present. (Meter shows
continuity)
3. Remove jumper from J6.
• OK-TO-MOVE signal off (Meter shows no
continuity)
• Gas continues to flow
• DC LED goes off
After 20 second Post flow time
• Gas solenoid closes
• Gas flow stops
If the unit has the Basic CNC Interface harness the
test is complete. If the unit does not function as
stated above, then note the symptom and proceed
to Section "5.10 CNC Interface Problems".If the unit
has the Automation Interface PCB installed, continue
with this section.
4. There are three (3) ARC VOLTs signals available
from the J6 connector.
a) J2-9 (+) to J2-7 (-)
b) J2-5 (+) to J2-6 (-) (Auto Interface pcb J3 con-
nector with jumper installed between pins 1
and 2) = ARC VOLTS divided by 50
c) J2-5 (+) to J2-6 (-) (Auto Interface pcb J3 con-
nector with jumper installed between pins 2
and 3) = ARC VOLTS divided by 16
Measure the voltage between these points while pi-
loting (Open Circuit Voltage) and while cutting. The
voltages should approx as listed below
Open Circuit Voltage
Cutting Voltage
a) 300 VDC
100 VDC
b) 6 VDC
2 VDC
c) 19 DVC
6 VDC
This completes the CNC Interface Test. If the above are all
correct then the unit is functioning correctly. If the unit
does not function as stated, then note the symptom and
proceed to Section "5.10, CNC Interface Problems".
Summary of Contents for Cutmaster 82
Page 2: ......
Page 4: ...This Page Intentionally Blank...
Page 8: ...TABLE OF CONTENTS...
Page 16: ...cutmaster 82 GENERAL INFORMATION 1 8 Manual 0 4980...
Page 24: ...CutMaster 82 INTRODUCTION 2T 4 Manual 0 4980 This Page Intentionally Blank...
Page 36: ...CutMaster 82 OPERATION 4 4 Manual 0 4980 This Page Intentionally Blank...
Page 54: ...CutMaster 82 OPERATION 4T 18 Manual 0 4980 This Page Intentionally Blank...
Page 55: ...cutmaster 82 Manual 0 4980 5 1 SERVICE SECTION 5 SYSTEM SERVICE 5 01 General Maintenance...
Page 79: ...cutmaster 82 Manual 0 4980 5 25 SERVICE This Page Intentionally Blank...
Page 82: ...CutMaster 82 SERVICE 5 28 Manual 0 4980 This Page Intentionally Blank...
Page 93: ...cutmaster 82 Manual 0 4980 6 9 PARTS LIST A 07994 6 1 4 2 3 5 7 8 9 10 12 11 10...
Page 102: ...CutMaster 82 PARTS REPLACEMENT 7 8 Manual 0 4980 This Page Intentionally Blank...
Page 107: ...cutmaster 82 Manual 0 4980 A 5 APPENDIX This Page Intentionally Blank...
Page 110: ...CutMaster 82 APPENDIX A 8 Manual 0 4980 APPENDIX 6 SYSTEM SCHEMATIC 600V UNITS...