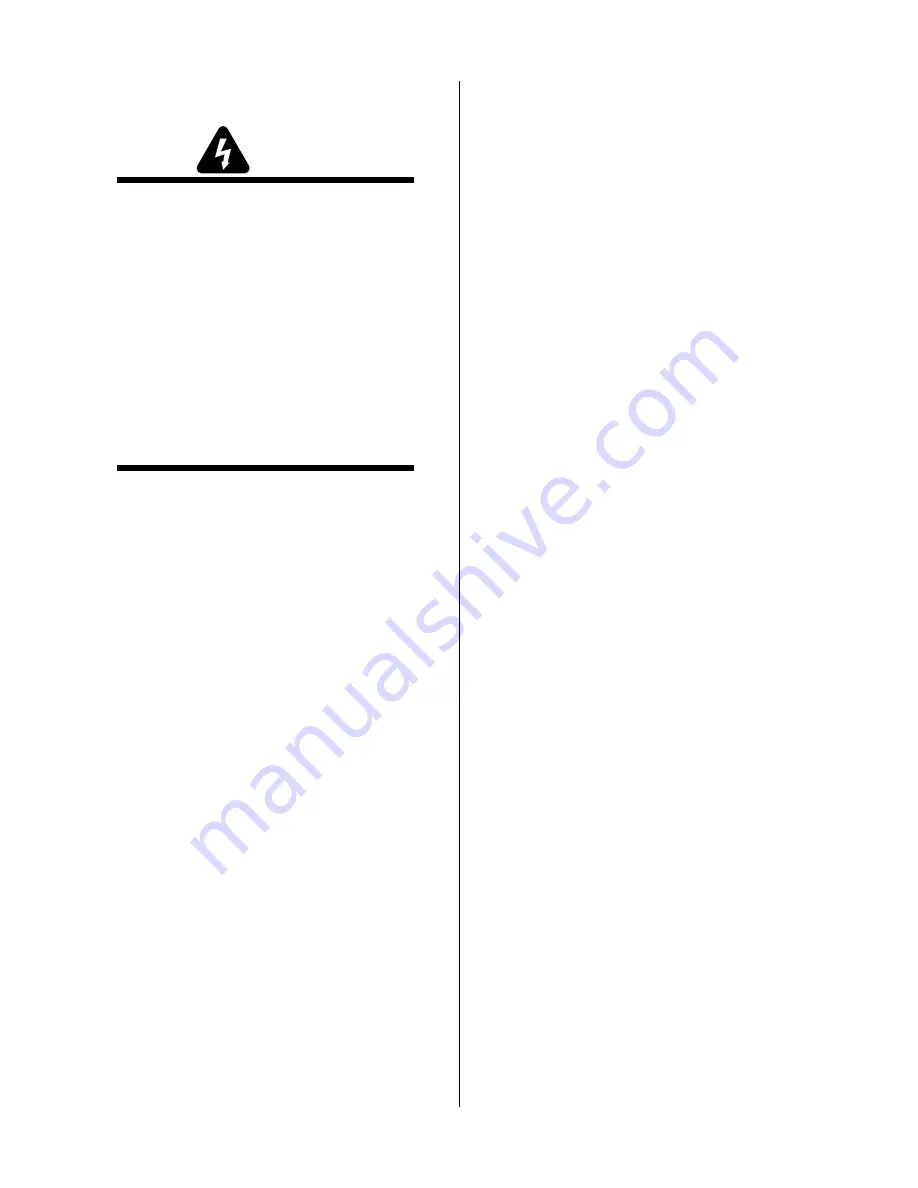
TROUBLESHOOTING
4-2
Manual 0-2957
4.04 Common Operating Problems
WARNINGS
Disconnect primary power at the source before dis-
assembling the power supply, torch, or torch leads.
Frequently review the Important Safety Precau-
tions in Section 1. Be sure the operator is equipped
with proper gloves, clothing, and eye and ear pro-
tection. Make sure no part of the operator's body
comes into contact with the workpiece while the
torch is activated.
Sparks from the cutting process can cause damage
to coated, painted, and other surfaces such as glass,
plastic and metal.
Handle torch leads with care and protect them from
damage.
A. Piloting
Piloting is harder on parts life than actual cutting be-
cause the pilot arc is directed from the electrode to
the tip rather than to a workpiece. Whenever pos-
sible, avoid excessive pilot arc time to improve parts
life.
B. Torch Standoff
Improper standoff (the distance between the torch tip
and workpiece) can adversely affect tip life as well as
shield cup life. Standoff may also significantly affect
the bevel angle. Reducing standoff generally results
in a more square cut.
C. Edge Starting
For edge starts, hold the torch perpendicular to the
workpiece with the front of the torch tip at the edge
of the workpiece, not touching, at the point where the
cut is to start. When starting at the edge of the plate,
do not pause at the edge and force the arc to “reach”
for the edge of the metal. Establish the cutting arc as
quickly as possible.
D. Direction of Cut
The plasma gas stream swirls as it leaves the torch.
The purpose of the swirl is to maintain a smooth col-
umn of gas. The swirl effect results in one side of a
cut being more square than the other. Viewed along
the direction of travel, the right side of the cut is more
square than the left.
E. Dross
When dross is present on carbon steel, it is commonly
referred to as either “high speed, slow speed, or top
dross”. Dross present on top of the plate is normally
caused by too great a torch to plate distance. "Top
dross" is normally very easy to remove and can often
be wiped off with a welding glove. "Slow speed dross"
is normally present on the bottom edge of the plate.
It can vary from a light to heavy bead, but does not
adhere tightly to the cut edge, and can be easily
scraped off. "High speed dross" usually forms a nar-
row bead along the bottom of the cut edge and is very
difficult to remove. When cutting a troublesome steel,
it is sometimes useful to reduce the cutting speed to
produce "slow speed dross". Any resultant cleanup
can be accomplished by scraping, not grinding.
F. Parts - In - Place Circuit
The power supply connects to Models SL60 or SL100
Torches. Parts-In-Place circuitry in the power supply
checks for the presence of torch consumable parts in
the torch head. When the shield cup is properly in-
stalled, there is a slight gap between the shield cup
and the torch handle. Gas vents through this gap as
part of normal operation. Do not attempt to force the
shield cup to close this gap. Forcing the shield cup
against the torch head or torch handle can damage
torch components.
G. Common Cutting Faults
1. Insufficient Penetration
a. Cutting speed too fast
b. Torch tilted too much
c. Metal too thick
d. Worn torch parts
e. Cutting current too low
f.
Non-Genuine Thermal Dynamics parts used
2. Main Arc Extinguishes
a. Cutting speed too slow
b. Torch standoff too high from workpiece
c. Cutting current too high
d. Work cable disconnected
e. Worn torch parts
f.
Non-Genuine Thermal Dynamics parts used
Summary of Contents for CUTMASTER 81
Page 2: ......
Page 4: ......
Page 16: ...INTRODUCTION 2 2 Manual 0 2957 This Page Left Blank...
Page 20: ...DESCRIPTION 3 4 Manual 0 2957 This Page Left Blank...
Page 40: ...TROUBLESHOOTING 4 20 Manual 0 2957 This Page Left Blank...
Page 62: ...PARTS LISTS 6 10 Manual 0 2957 This Page Left Blank...