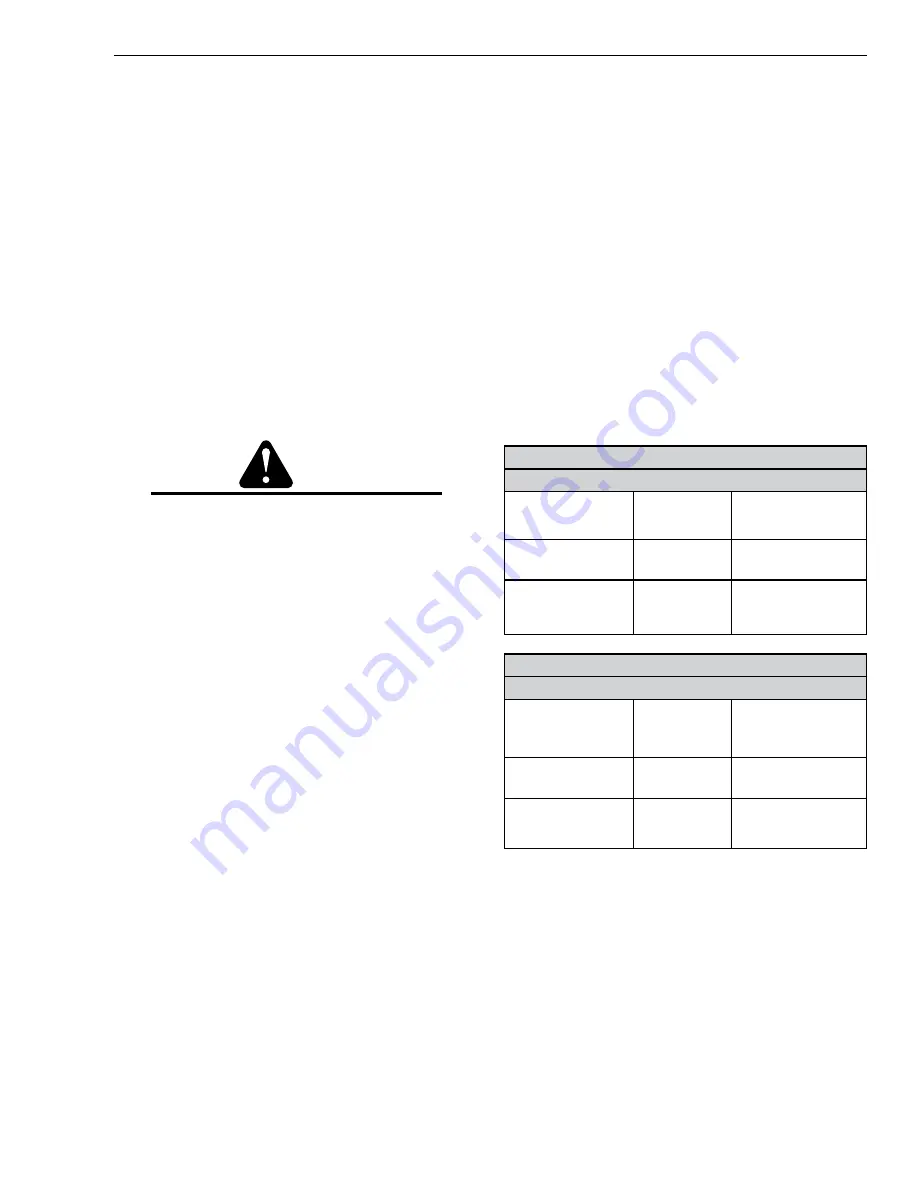
CUTMASTER 12mm
Manual 0-5077
5-9
SERVICE
C. Pre Power Up Tests
Prior to applying primary line power to the unit,
perform the following checks to prevent component
failure or blowing primary fuses. The troubleshoot-
ing guide will assume these tests were done and no
failure was found or that any failures found were
corrected.
1. Main Contactor (W1) Check – Section 5.12-A.
2. Input Diode Module Test – Section 5.12-B.
3. Input Capacitor PCB Test –Section 5.12-C.
4. IGBT Modules Test – Section 5.12-D.
5. Output Diode Module Test – Section 5.12-E.
6. Pilot IGBT Test – Section 5.12-F.
If all of the Pre Power-Up Tests are OK, proceed with
the trouble shooting guide.
CAUTION
Due to the close proximity of the Main PCB to the
Capacitor PCB, It is recommended to use an insu-
lated meter probe when making measurements on
the J2 connector on the Main PCB. Do not short
between the pins. Do not short to the Capacitor
PCB connections.
D. Initial Set up Conditions
This section is to help isolate the defective circuit
before troubleshooting, identify symptoms, and test
the unit for proper operation. Follow the instructions
as given to identify the possible symptom(s) and the
defective circuit. After repairs are complete, run the
following tests again to verify that the unit is fully
operational.
1. Connect gas supply to rear of Power Supply.
2. Turn ON gas supply and set operating pressure
per pressure setting label on power supply.
3. Set the Power Supply controls as follows:
• ON/OFF SWITCH to OFF position
• Turn FUNCTION CONTROL SWITCH to SET
position
• CURRENT CONTROL POTENTIOMETER to
MAXIMUM position, fully clockwise.
E. Main Input and Internal Power Test
1. Connect Primary Line power to the unit.
2. Turn the ON/OFF SWITCH (SW1) to ON position
and observe the following:
• Software version is displayed (See section 5.04
Fault Indicators)
After approximately three (3) seconds
• Inrush relay on PCB 1 energizes, starting pre-
charging of working capacitors.
• W1 energizes
• AC and GAS Indicators come ON
• Gas flows
• Fans turn ON
3. Adjust the pressure regulator to set the gas pres-
sure as specified in charts.
STANDOFF
CutMaster 12mm Gas Pressure Settings
Leads
Length
SL60
(Hand Torch)
SL100
(Mechanized Torch)
Up to 25'
(7.6 m)
75 psi
5.2 bar
70 psi
4.8 bar
Each additional
25' (7.6 m)
Add 5 psi
0.4 bar
Add 5 psi
0.4 bar
DRAG
CutMaster 12mm Gas Pressure Settings
Leads
Length
SL60
(Hand Torch)
SL100
(Mechanized Torch)
Up to 25'
(7.6 m)
80 psi
5.5 bar
75 psi
5.2 bar
Each additional
25' (7.6 m)
Add 5 psi
0.4 bar
Add 5 psi
0.4 bar
4. Turn FUNCTION CONTROL SWITCH to RUN
position
• Solenoid turns OFF, gas stops flowing (pres-
sure display may increase slightly when gas
is not flowing)
This completes the Main Input and Internal Power Test. If
the above are all correct then proceed to the next section
"F. Pilot Arc Test". If the unit does not function as stated
above, then note the symptom and proceed to Section
"5.07, Main Input and Internal Power Problems".
Summary of Contents for A-08950
Page 4: ...This Page Intentionally Blank ...
Page 8: ...This Page Intentionally Blank ...
Page 16: ...CUTMASTER 12mm GENERAL INFORMATION 1 8 Manual 0 5077 This Page Intentionally Blank ...
Page 24: ...CUTMASTER 12mm INTRODUCTION 2T 4 Manual 0 5077 This Page Intentionally Blank ...
Page 34: ...CUTMASTER 12mm OPERATION 4 4 Manual 0 5077 This Page Intentionally Blank ...
Page 48: ...CUTMASTER 12mm OPERATION 4T 14 Manual 0 5077 This Page Intentionally Blank ...
Page 69: ...CUTMASTER 12mm Manual 0 5077 5 21 SERVICE This Page Intentionally Blank ...
Page 73: ...CUTMASTER 12mm Manual 0 5077 5 25 SERVICE This Page Intentionally Blank ...
Page 77: ...CUTMASTER 12mm Manual 0 5077 5 29 SERVICE This Page Intentionally Blank ...
Page 78: ...CUTMASTER 12mm SERVICE 5 30 Manual 0 5077 This Page Intentionally Blank ...
Page 89: ...CUTMASTER 12mm Manual 0 5077 6 9 PARTS LIST A 07994_AB 1 4 2 3 5 6 7 8 9 10 12 11 10 13 ...
Page 98: ...CUTMASTER 12mm PARTS REPLACEMENT 7 8 Manual 0 5077 This Page Intentionally Blank ...
Page 107: ...This Page Intentionally Blank ...