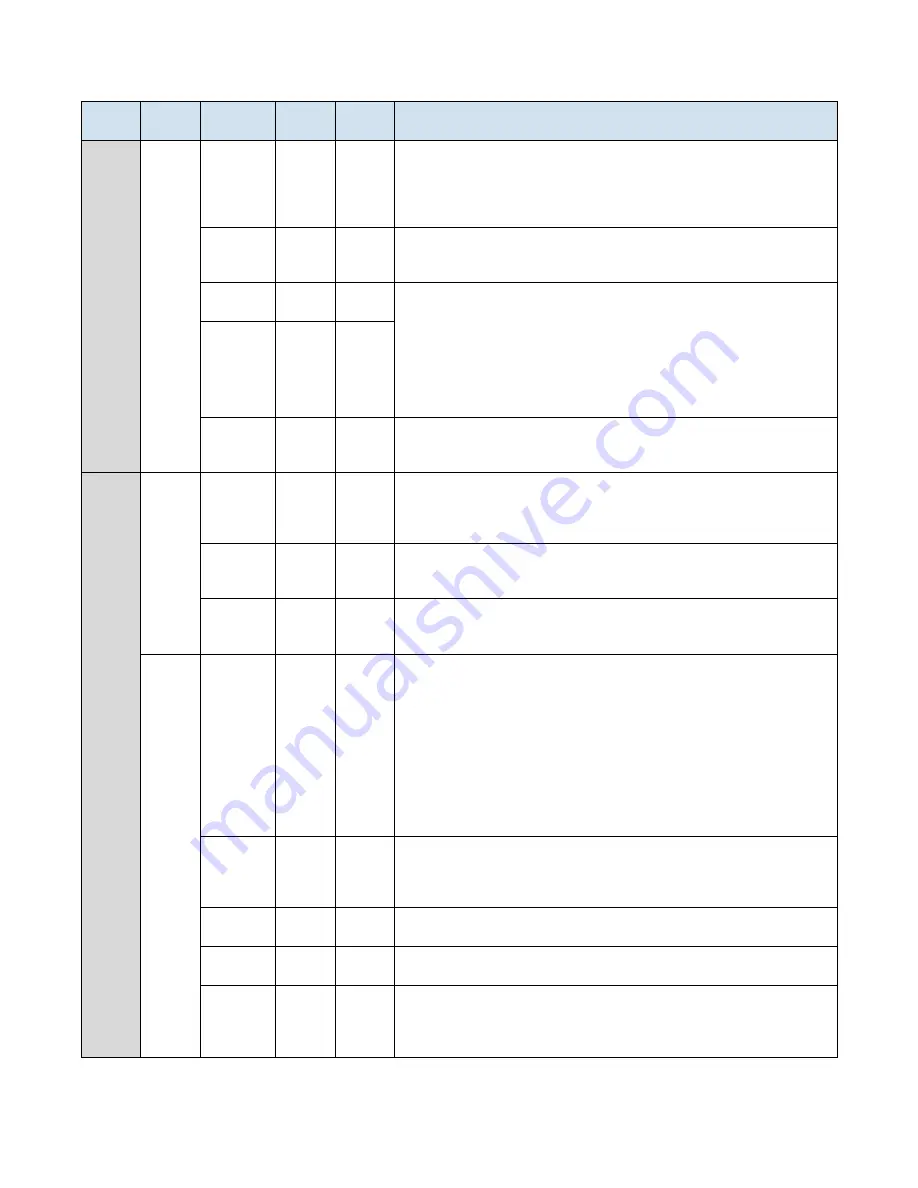
6
Table 1 - User Parameters (continued)
Category Screen
Number
Parameter
Default
Value
Range
Description
TCU
Setup
3/6
PV Source
To Proc
To Proc
From
Proc
To/From
Average
Allows the user to select which RTD temperature sensor is used for temperature
regulation. The selected signal is used by the control loop where it will attempt to
reach setpoint.
PV
Smoothing
5 sec
0 to 720 Used to smooth the RTD temperature probe signal. Normally, this should remain
in the 0-10 sec range, but can be increased if process fluid is not an equal
temperature throughout.
Low Pres
Count
3
1 to 25
Both of these parameters work hand-in-hand to define the TCU’s reaction to
multiple process fluid low-pressure events while the TCU is in operation. By
default, the TCU will tolerate up to 3 process fluid low-pressure events every 15
minutes; the TCU temporarily shuts down during the low-pressure event, and
automatically restart when the pressure returns. Because excessive, frequent
starting/stopping of the TCU can cause motor/pump damage, the purpose of
these parameters is to protect the TCU if operating in an environment with
unstable fluid pressure.
Low Pres
Time
15 min
1 to 999
Units
°F
°F or °C
Used to select the desired temperature unit of measure. After changing, the
controller will automatically reboot. Note that this parameter is NOT automatically
set to default if the user executes a “Load Defaults” to reset to default parameters.
Venting
4/6
Valve Vent
30 sec
5 to 180 Upon cold startup, the TCU will flush the process loop with fresh fluid to remove
air. The pump will not run during this time. Once finished, it will start the pump
and continue to flush with the pump’s assistance. No loop-temperature regulation
occurs in this state. Increase this value if you have an excessively long fluid loop.
Valve/Pmp
Vent
30 sec
5 to 180 Upon cold startup, and after the “Valve Vent” parameter’s time has expired, the
TCU will start the pump to assist in deaeration. No loop-temperature regulation
occurs in this state. Increase this value if you have an excessively long fluid loop.
Vent Bypass 120°F
32 to 260 If the process loop is above this temperature, the “Valve Vent” and “Valve/Pmp
Vent” will not occur. This makes the TCU restarts quickly, while still deaerating if
the machine starts from a cold state.
Control
Loop
5/6
System Size ---
Small
Medium
Large
This setting quickly selects factory-suggested parameters below for P-Band, I-
Gain, D-Gain, and Deadband. Select the setting that best describes your system.
“Large” is for a slow setting for systems with more than 80 gallons of fluid volume
and more than 5,600 lbs of steel mold mass. This setting has a proportional band
of 3ºF to allow a slower response. “Normal” is the factory default tuning setting
and covers the majority of applications with 10 to 80 gallons of fluid volume and
700 to 5,600 lbs of steel mold mass. This setting has a proportional band of 7ºF.
“Small” is for fast setting for systems with less than 10 gallons of fluid volume and
less than 700 lbs of steel mold mass. This setting has a proportional band of 15ºF
to allow a fast response. Alternatively, you can also directly edit the PID settings as
described below.
P-Band
10 Δ°F
0.2 to
999.7
Proportional Band for PID temperature control. A smaller number will promote a
more aggressive proportional response. At the default 10 Δ⁰F, this means that the
proportional response will be at 100% when the temperature is 10 Δ⁰F from
setpoint.
I-Gain
50
0 to 999 Integral Gain for PID temperature control. A smaller number will promote a more
aggressive integral response. Zero will disable all integral responses.
D-Gain
10
0 to 999 Derivative Gain for PID temperature control. A larger number will promote a more
aggressive derivative response. Zero will disable all derivative responses.
Deadband
0.5 Δ°F
0 to 99.9 Defines a region of process temperature deviation that will have no effect in PID
control loop. By having a deadband, wear-and-tear on the TCU is minimized
because it does not have to try as hard to maintain the process temperature
perfectly to setpoint.
Summary of Contents for Aquatherm RQE
Page 1: ......
Page 2: ......
Page 4: ...Page Intentionally Blank...
Page 20: ...16 Notes...
Page 21: ...17 Notes...
Page 22: ...18 Notes...
Page 23: ......