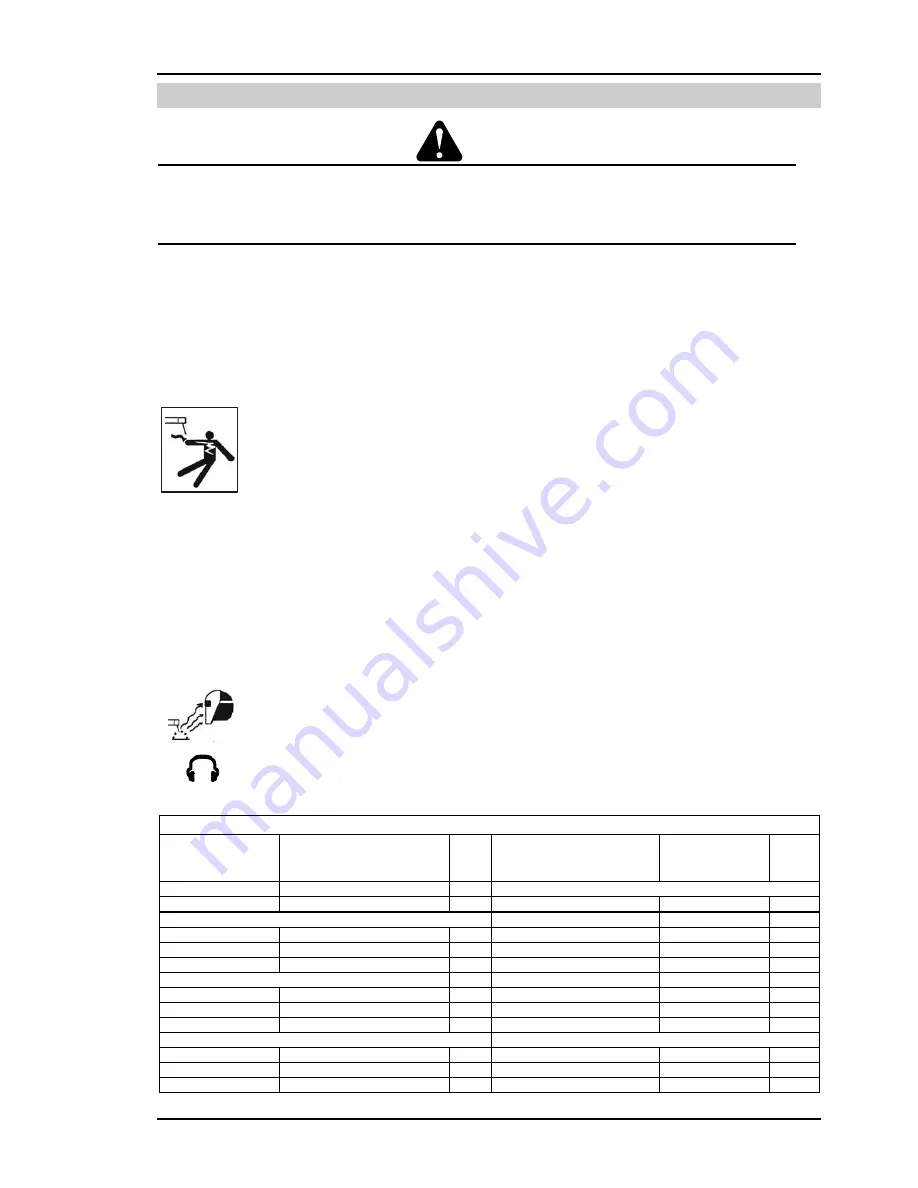
SECTION 1:
Safety Instructions and Warnings
WARNING
ARC WELDING can be hazardous.
Protect yourself and others from possible serious injury or death. Keep children away. Pace maker wearers keep away until
consulting your doctor. Do not lose these instructions. Read operating / instruction manual before installing, operating or
servicing this equipment.
Welding products and welding processes can cause serious injury or death, or damage to other equipment or property, if the operator does not
strictly observe all safety rules and take precautionary actions.
Safe practices have developed from past experience in the use of welding and cutting. These practices must be learned through study and
training before using this equipment. Anyone not having extensive training in welding and cutting practices should not attempt to weld. Certain
practices apply to equipment connected to power lines; other practices apply to engine driven equipment.
Safe practices are out lined in the American National Standard Z49.1 entitled: SAFETY IN WELDING AND CUTTING. This publication and other
guides to what you should learn before operating this equipment are listed at the end of these safety precautions.
HAVE ALL INSTALLATION, OPERATION, MAINTENANCE, AND REPAIR WORK PERFORMED ONLY BY QUALIFIED PEOPLE.
ELECTRIC SHOCK can kill.
Touching live electrical parts can cause fatal
shocks or severe burns. The electrode and work
circuit is electrically live whenever the output is on.
The input power circuit and machine terminal
circuits are also live when power is on. In
semiautomatic or automatic wire welding, the wire,
wire reel, drive roll housing, and all metal parts touching the welding
wire are electrically live. Incorrectly installed or improperly grounded
equipment is a hazard.
1.
Do not touch live electrical parts.
2.
Wear dry, hole-free insulating gloves and body protection.
3.
Insulate yourself from work and ground using dry insulating
mats or covers.
4.
Disconnect input power or stop engine before installing or
servicing this equipment. Lock input power disconnect switch
open, or remove line fuses so power cannot be turned on
accidentally.
5.
Properly install and ground this equipment according to its
Owner's Manual and national, state, and 10 cal codes.
6.
Turn off all equipment when not in use. Disconnect power to
equipment if it will be left unattended or out of service.
7.
Use fully insulated electrode holders. Never dip holder in water to
cool it or lay it down on the ground or the work surface. Do not
touch holders connected to two welding machines at the same
time or touch other people with the holder or electrode.
8.
Do not use worn, damaged, under sized or poorly spliced cables.
9.
Do not wrap cables around your body.
10.
Ground the workpiece to a good electrical (earth) ground.
11.
Do not touch electrode while in contact with the work (ground)
circuit.
12.
Use only well-maintained equipment. Repair or replace damaged
parts at once.
13.
In confined spaces or damp locations, do not use a welder with
AC output unless it is equipped with a voltage reducer. Use
equipment with DC output.
14.
Wear a safety harness to prevent falling if working above floor
level.
15.
Keep all panels and covers securely in place.
ARC RAYS can burn eyes and skin;
NOISE can damage hearing.
Arc rays from the welding process produce intense
heat and strong ultraviolet rays that can burn eyes
and skin. Noise from some processes can damage
hearing.
1.
Wear a welding helmet fitted with a proper shade of filter (see
ANSI 249.1 listed in Safety Standards) to protect your face and
eyes when welding or watching.
2.
Wear approved safety glasses. Side shields recommended.
3.
Use protective screens or barriers to protect others from flash
and glare; warn others not to watch the arc.
4.
Wear protective clothing made from durable, flame-resistant
material (wool and leather) and foot protection.
5.
Use approved earplugs or earmuffs if noise level is high.
Eye protection filter shade selector for welding or cutting (goggles or helmet), from AWS A 8.2-73
Welding or Cutting
operation
Electrode size Metal Thickness or
Welding Current
Filter
shade
no.
Welding or Cutting operation
Electrode size Metal
Thickness or Welding
Current
Filter
shade no.
Torch soldering
All
2
Gas metal arc welding
Torch brazing
All
2 or 3
Non Ferrous base metal
All
11
Oxygen cutting
Ferrous base metal
All
12
Light
Under 1 in., 25 mm
3 or 4 Gas tungsten arc welding (TIG)
All
12
Medium
1 – 6 in., 25 – 150 mm
4 or 5 Atomic Hydrogen welding
All
12
Heavy
Over 6 in., 150 mm
5 or 6 Carbon Arc welding
All
12
Gas welding
Plasma arc Welding
All
12
Light
Under 1/8 in., 3 mm
4 or 5 Carbon Arc Gouging
Medium
1/8 – 1/2 in., 3 – 12 mm
5 or 6
Light
12
Heavy
Over 1/2 in., 12 mm
6 or 8
Heavy
14
Shielded metal-arc welding (stick) electrodes
Plasma arc cutting
Under 5/32 in., 4 mm
10
Light
Under 300 Amp
9
Under 5/32 to ¼ in., 4 to 6.4mm
12
Medium
300 to 400 Amp
12
Over ¼ in., 6.4 mm
14
Heavy
Over 400 Amp
14
1
Summary of Contents for C/W VFE 4C HS III
Page 10: ...Page left blank intentionally 4...
Page 13: ...1 04 SYMBOL LEGEND Figure 2 7...
Page 27: ...This page has been left blank intentionally 21...
Page 53: ...This page has been left blank intentionally 47...
Page 54: ...SECTION 11 SPARE PARTS 11 01 Parts Description Fabricator 250C 320C Figure 26 48...
Page 57: ...11 02 Parts Description Fabricator 320S 400S Figure 27 51...
Page 62: ...11 04 Parts Description Fabricator 500S Figure 29 56...
Page 69: ...12 02 Power Source Schematic Fabricator 320S III 400S III Figure 33 63...
Page 70: ...12 03 Power Source Schematic Fabricator 500S III Figure 34 64...
Page 71: ...12 04 Wire Feed Unit Schematic VFE 4C III VFE 4C HS III WFU Figure 35 65...
Page 73: ...This page has been left blank intentionally 67...