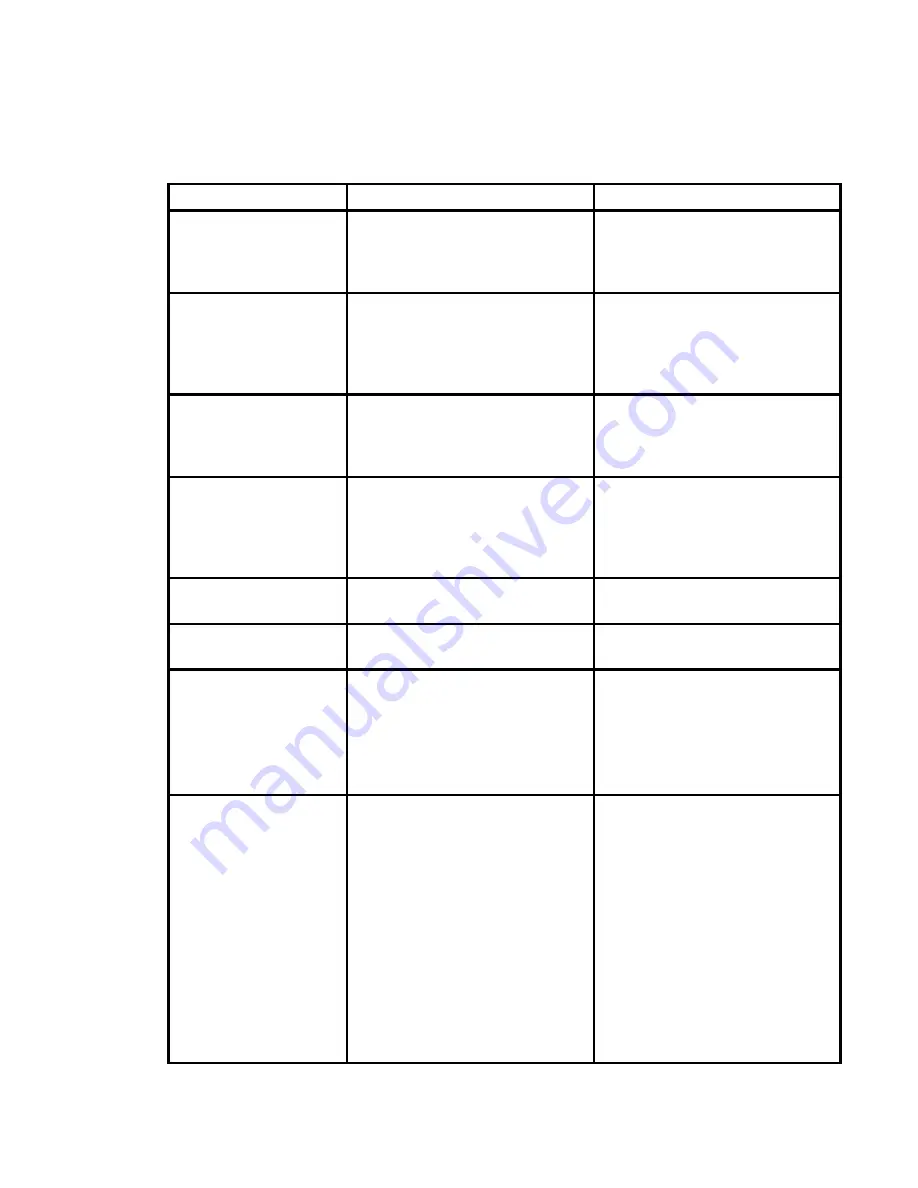
41
9.03 TIG Welding Problems
Weld quality is dependent on the selection of the correct consumables, maintenance of equipment and
proper welding technique.
Description
Possible
Cause
Remedy
1 Excessive beard build-
up or poor penetration
or poor fusion at edges
of weld.
Welding current is too low.
Increase weld current and/or faulty
joint preparation.
2 Weld bead too wide
and flat or undercut at
edges of weld
or excessive
burn through.
Welding current is too high.
Decrease
weld
current.
3 Weld bead too small or
insufficient penetration
or ripples in bead are
widely spaced apart.
Travel speed too fast.
Reduce travel speed.
4 Weld bead too wide or
excessive bead build up
or excessive penetra-
tion in
butt joint.
Travel speed too slow.
Increase travel speed.
5 Uneven leg length in
fillet joint.
Wrong placement of filler rod.
Re-position filler rod.
6 Electrode melts when
arc is struck.
Electrode is connected to the
‘+’ terminal.
Connect the electrode to the
‘
−
’ terminal.
7 Dirty weld pool.
A Electrode contaminated through
contact with work piece or filler
rod material.
A Clean the electrode by grinding off
the contaminates.
B Gas contaminated with air.
B Check gas lines for cuts
and loose fitting or change
gas cylinder.
8 Electrode melts or
oxidizes when an arc is
struck.
A No gas flowing to
welding region.
A Check the gas lines for kinks
or breaks and gas
cylinder contents.
B Torch is clogged with dust.
B Clean torch
C Gas hose is cut.
C Replace gas hose.
D Gas passage contains impurities.
D Disconnect gas hose from torch
then raise gas pressure and blow
out impurities.
E Gas regulator turned OFF.
E Turn ON.
F Torch valve is turned OFF.
F Turn ON.
G
The electrode is too small for
the welding current.
G Increase electrode diameter or
reduce the welding current.