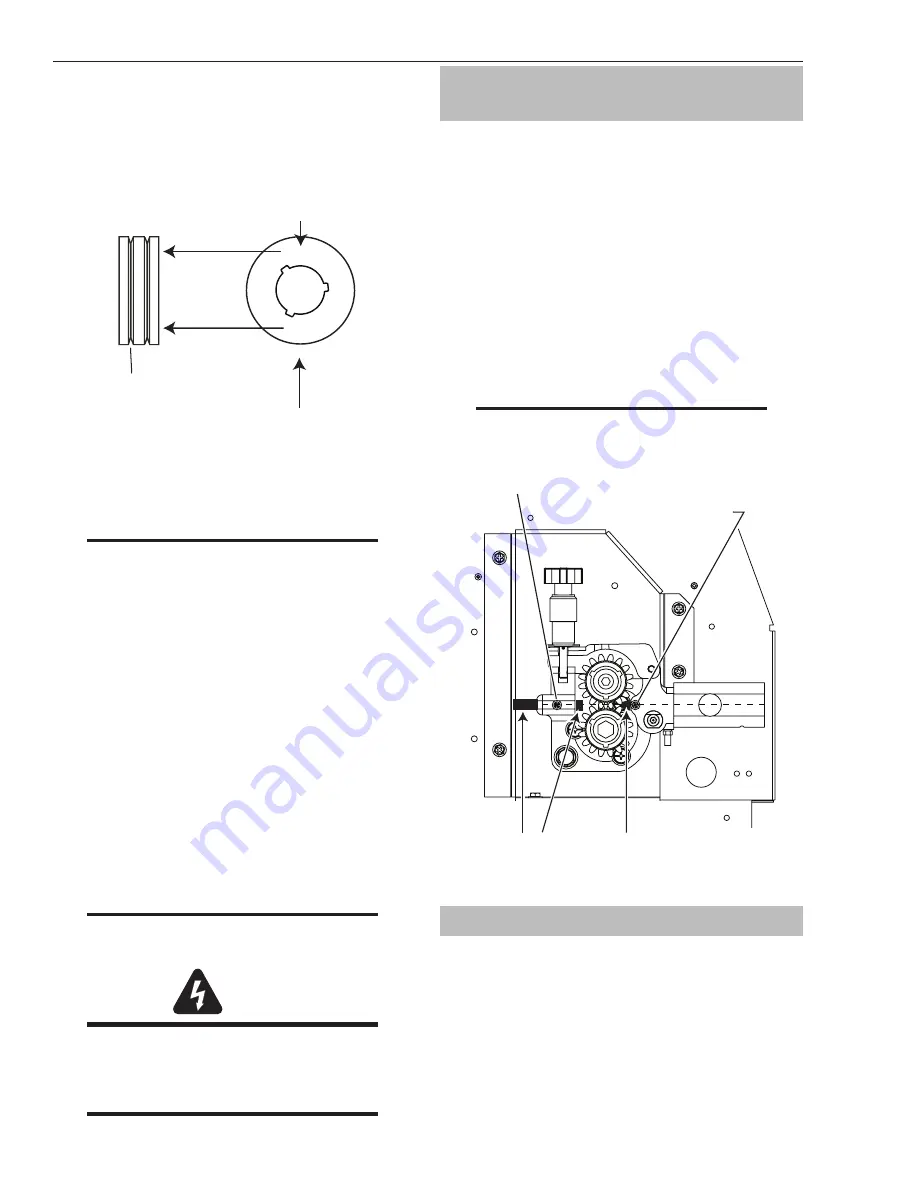
FABRICATOR 281
INSTALLATION
-10
Manual No. 0-4880B
3.11 Input And Output Wire Guide
Installation
Refer to Figure 3-10.
Install the input wire guide (the longer one) by
loosening the input guide lockscrew and inserting
the guide into the hole in the feedhead assembly. The
recessed end of the guide should be toward the wire
spool. Adjust the guide so that it is clear of the feed
rolls and tighten the input guide lockscrew.
Install the output wire guide in the same manner,
with the conical end toward the feed rolls. The tip of
the conical end should be as close to the feedrolls as
practical. Tighten the output guide lockscrew.
NOTE
Before tightening the input and output guide
lockscrews, install the feedroll to help in the
alignment of the wire guides.
Output Wire Guide
Input Guide Lockscrew
Input Wire Guide
Output Guide Lockscrew
Art # A-07445
Figure 3-10: Wire Guide Installation
3.12 Installing Wire Spool on the Remote
As delivered from the factory, the unit is set for a 33/44
lb. or 12" (300mm) spool.
Installation of wire spool
1. Remove Wire Spool Hub Nut by turning counter
clock wise (to the left).
2. Remove the spring from the hub.
The stamped marking on the feedroll refers to the
groove furthest from the stamped marking. When
mounted, that will be the groove closest to the motor
and the one to thread.
To ensure proper wire feed, the groove closest to the
motor must match the electrode wire size being used.
.045” (1.2mm) Groove
Art: A-07150
The size that is visible when
fitting the feedroll is the groove
size in use.
.045
1.2
.045” (1.2mm) Stamping
Figure 3-9: Feedroll Example
NOTE
All grooved feed rolls have their wire size
or range stamped on the side of the roll. On
rolls with different size grooves, the outer
(visible when installed) stamped wire size
indicates the groove in use.
Refer to feed roll kit #375980 in the Appendix for the
proper selection and ordering of feed roll kits. Kit
includes feedrolls, an input wire guide and an output
wire guide for a specific wire type and size.
Feed rolls are removed by twisting the tight-fitting feed
roll retainer cap and aligning the retaining knob splines/
tabs with the drive gear splines. Feedrolls are installed
by putting the feedroll onto the drive gear splines and
twisting the feedroll retainer cap so that the splines/tabs
rest against the face of the feedroll where they will click
into place.
NOTE
Installation of all styles of feed rolls for the
Fabricator 281 are identical.
WARNING
The welding wire is electrically Hot if it is fed
by depressing gun switch. Electrode contact
to work piece will cause an arc with gun
switch depressed.
Summary of Contents for 281 FABRICATOR
Page 54: ...fabricator 281 OPERATION 4 18 Manual No 0 4880B NOTES ...
Page 80: ...Fabricator 281 CIRCUIT OPERATION 8 Manual No 0 4880B ...
Page 98: ...fabricator 281 APPENDIX A Manual No 0 4880B APPENDIX 4 SPOT TIMER CIRCUIT DIAGRAM Art A 07521 ...
Page 104: ...fabricator 281 APPENDIX A 12 Manual No 0 4880B ...
Page 105: ......