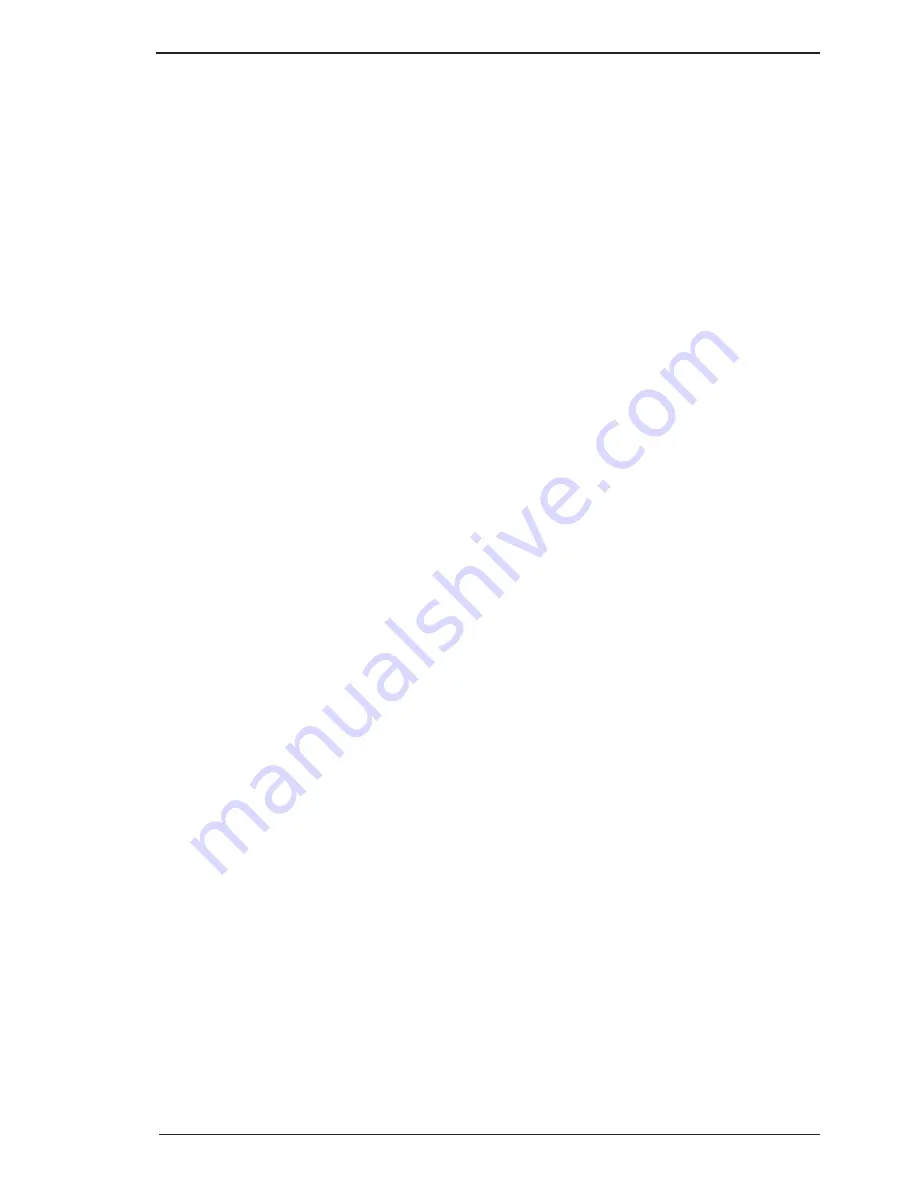
INSTALLATION/SETUP 202 AC/DC INVERTER
Manual 0-5239
3-3
INSTALLATION, OPERATION AND SETUP
3. Computer and other control equipment.
4. Safety critical equipment, e.g. guarding of industrial equipment.
5. The health of people around, e.g. the use of pacemakers and hearing aids.
6. Equipment used for calibration and measurement.
7. The time of day that welding or other activities are to be carried out.
8. The immunity of other equipment in the environment: the user shall ensure that other equipment being
used in the environment is compatible: this may require additional protection measures.
The size of the surrounding area to be considered will depend on the structure of the building and other
activities that are taking place. The surrounding area may extend beyond the boundaries of the premises.
C. Methods of Reducing Electromagnetic Emissions
1. Mains Supply
Welding equipment should be connected to the mains supply according to the manufacturer’s
recommendations. If interference occurs, it may be necessary to take additional precautions such as
filtering of the mains supply. Consideration should be given to shielding the supply cable of permanently
installed welding equipment in metallic conduit or equivalent. Shielding should be electrically continuous
throughout its length. The shielding should be connected to the Welding Power Source so that good
electrical contact is maintained between the conduit and the Welding Power Source enclosure.
2. Maintenance of Welding Equipment
The welding equipment should be routinely maintained according to the manufacturer’s recommendations.
All access and service doors and covers should be closed and properly fastened when the welding
equipment is in operation. The welding equipment should not be modified in any way except for those
changes and adjustments covered in the manufacturer’s instructions. In particular, the spark gaps of
arc striking and stabilising devices should be adjusted and maintained according to the manufacturer’s
recommendations.
3. Welding Cables
The welding cables should be kept as short as possible and should be positioned close together, running
at or close to the floor level.
4. Equipotential Bonding
Bonding of all metallic components in the welding installation and adjacent to it should be considered.
However. Metallic components bonded to the work piece will increase the risk that the operator could
receive a shock by touching the metallic components and the electrode at the same time. The operator
should be insulated from all such bonded metallic components.
5. Earthing of the Workpiece
Where the workpiece is not bonded to earth for electrical safety, nor connected to earth because of it’s
size and position, e.g. ship’s hull or building steelwork, a connection bonding the workpiece to earth
may reduce emissions in some, but not all instances. Care should be taken to prevent the earthing of
the workpiece increasing the risk of injury to users, or damage to other electrical equipment. Where
necessary, the connection of the workpiece to earth should be made by direct connection to the
workpiece, but in some countries where direct connection is not permitted, the bonding should be
achieved by suitable capacitance, selected according to national regulations.
6. Screening and Shielding
Selective screening and shielding of other cables and equipment in the surrounding area may alleviate
problems of interference. Screening the entire welding installation may be considered for special
applications.