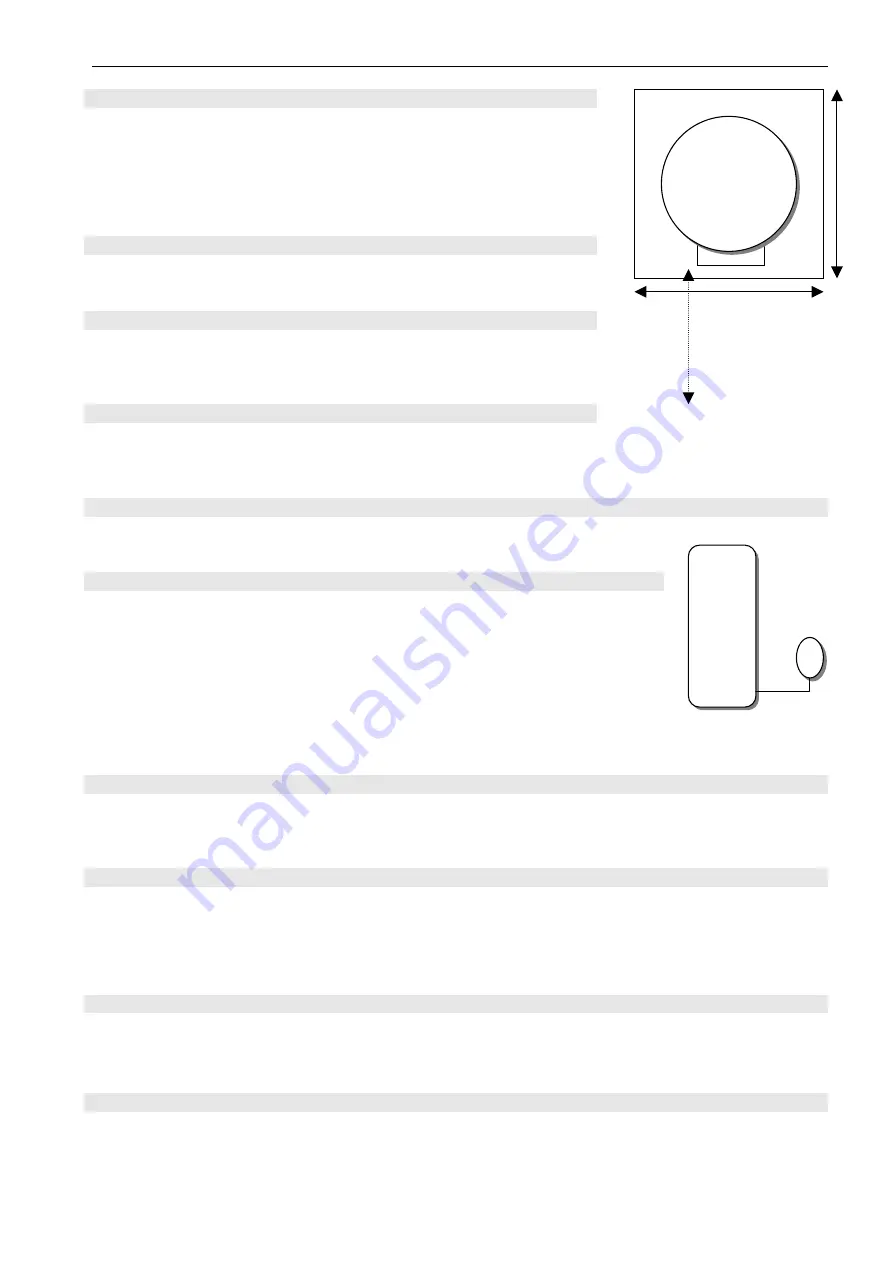
THERMAL INNOVATIONS (UK) LTD | THERMAFLOW® ELECTRIC COMBINATION BOILER |
Tel: 0870 850 5207
14
2.2.3 Clearances
The boiler should be positioned so that at least the minimum
operational and servicing clearances are provided, see diagram
2.2.3 additional clearances may be required around the boiler for
installation. A clearance of 600mm is required at the front of the
boiler for maintenance and installation.
2.3.1 General notes
The boiler is intended for use in a sealed system only.
2.3.2 Safety valve
The safety relief valve is an integral part of the boiler. It cannot
be adjusted but has a manual test device.
2.3.3 Pressure Gauge
A pressure gauge is incorporated into the boiler to indicate the system pressure.
The gauge has a cold fill set pointer.
2.3.4 Pump
The circulation pump is integral with the boiler.
2.3.5 Expansion vessel
The
TSL9/140U & TSL12/140U,
TSL12/170 & TSL12/170U
are all supplied
with an expansion vessel with a capacity of
25
litres. If the system water
content exceeds the maximum quoted in
table 1
,
[Data]
an additional vessel
should be connected into the system as close as possible to the central
heating return connection of the boiler.
Ref. Di
agram 2.3.5
The charge pressure shall not be less than the static head at the point of
connection, which is the height of the top point of the system above the expansion vessel.
2.3.6 By- pass
An automatic by- pass valve should be incorporated in the system for maximum system
efficiency. (A By-Pass MUST be fitted on all models).
2.3.7 Filling sealed systems
The boiler has a filling loop incorporated within it, and pressure gauge to register the fill pressure.
There must be no permanent connection to the mains water supply; even though a non return valve
is supplied.
Disconnect filling loop and seal both valves with suitable caps.
2.3.8 Corrosion inhibitor
The maintenance of sufficient concentration of corrosion inhibitor in your Thermaflow system is vital
to prevent corrosion. We would recommend
Sentinel X100, or equivalent
. Dose appropriately
according to the size of the Thermaflow and central heating system volume combined.
2.3.9 Draining
A draining tap must be provided at the lowest points of the system, which will allow the
entire system to be drained. The boiler has one drain tap fitted to it for the primary circuit.
Thermaflow ®
Expansion
Vessel
front
Diagram 2.2.3
- Clearances
600mm
Thermaflow
Unit
500mm
600mm
Diagram 2.3.5