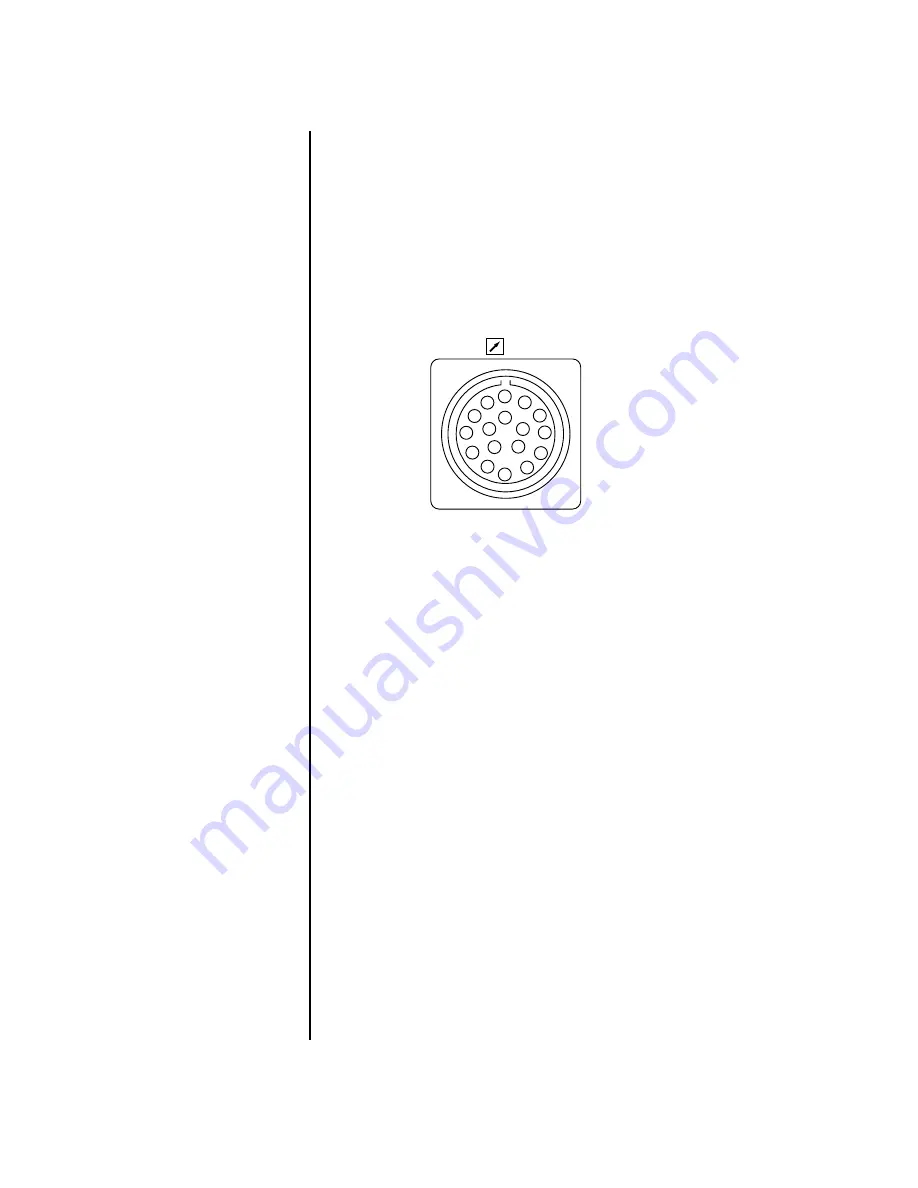
37
MANUAL 0-2510
BASIC TROUBLESHOOTING
4.03 REMOTE 17-Pin Connections
The REMOTE 17-Pin receptacle provides a junction point for connecting
various remote controls to the welding power source. The functions
available from this receptacle are:
•
Remote MIG synergic and Manual MIG Pulsers
•
Remote Control
•
Weld current and voltage signals for remote metering
To make connections, align keyway, insert plug, and rotate threaded collar
fully clockwise. The socket information is included in the event the
supplied cord is not suitable and it is necessary to wire a plug or cord to
interface with the REMOTE 17-Pin receptacle.
Socket
A
B
C
D
E
F
G
H
J
K
L
M
N
P
R
S
T
Amperage/voltage reference output signal; +10 volts;
for use with pulse controls
Amperage/voltage remote control input command
signal; +10 volts for machine maximum
Not used
Solid-state contactor remote control command signal;
+24 volts (operates above 13 volts) turns contactor on;
0 volts (open or ground) turns contactor off
Actual weld current signal; +1 volt per 100 amperes
of output current
PC board common; use as return for remote control
inputs/outputs only from terminals A, B, C, D, E, J and K
Not used
+24 volts unregulated; fused for 1/2 ampere
Not used
Remote amperage/voltage reference signal; 0 to
+10 volts (set by main rheostat) in CC and CV mode
-24 volts unregulated; fused for 1/2 ampere
Load voltage output signal; +1 volt per 10 volts of
load voltage
Not used
Circuit common (PC board common and internal
chassis ground) use as return (
±
) 18 volts logic
supply only (pins H and L)
Not used
Chassis ground
Not used
Function
17
A
B
C
D
E
F
G
H
P
J
K
L
M
N
T
S
R
Figure 8. REMOTE 17-Pin Connections
Summary of Contents for Thermal Arc 400GMS CC
Page 16: ...14 MANUAL 0 2510...