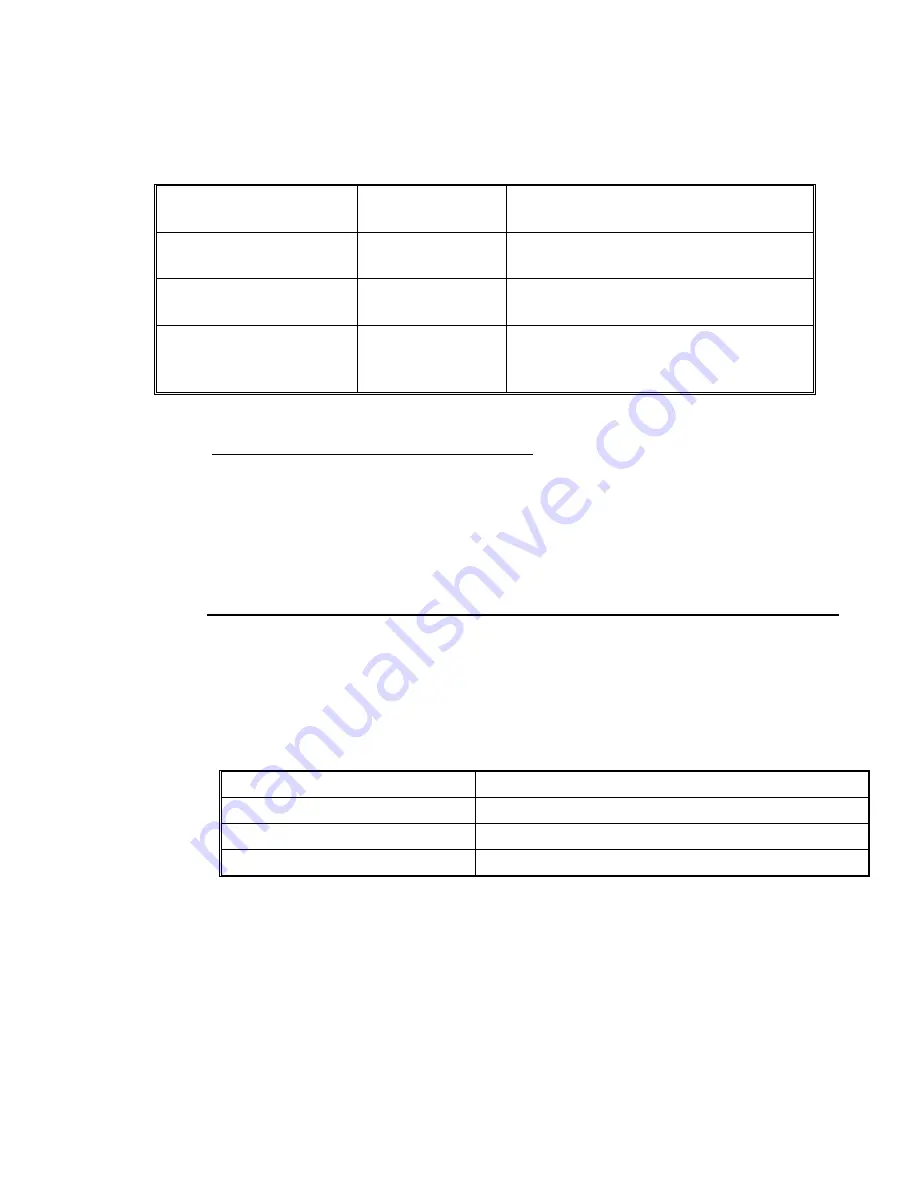
49
11.0 Voltage Reduction Device (VRD
)
11.01 VRD Specification
Description
Pro-Wave
185TSW
Notes
VRD Open Circuit Voltage
15.3 to 19.8V
Open circuit voltage between welding
terminals.
VRD Resistance
148 to 193 ohms
The required resistance between welding
terminals to turn ON the welding power.
VRD Turn OFF Time
0.2 to 0.3 seconds The time taken to turn OFF the welding
power once the welding current has
stopped.
11.02 VRD Maintenance
Routine inspection and testing (power source)
An inspection of the power source, an insulation resistance test and an earth resistance test
should be carried out
a)
For transportable equipment, at least once every 3 months; and
b)
For fixed equipment, at least once every 12 months.
The owners of the equipment shall keep a suitable record of the periodic tests.
Note 7
A transportable power source is any equipment that is not permanently connected and
fixed in the position in which it is operated.
In addition to the above tests and specifically in relation to the VRD fitted to this machine,
the following periodic tests should also be conducted by an accredited Thermal Arc service
agent.
Description
IEC 60974-1 Requirements
VRD Open Circuit Voltage
Less than 20V; at Vin=230V
VRD Turn ON Resistance
Less than 200 ohms
VRD Turn OFF Time
Less than 0.3 seconds
If this equipment is used in a hazardous location or environments with a high risk of
electrocution then the above tests should be carried out prior to installation at this location.
Summary of Contents for Thermal Arc 185TSW
Page 2: ......
Page 4: ...4 13 0 PARTS LIST 53 APPENDIX A INTERCONNECT DIAGRAM 56 APPENDIX B AUTOMATION 58...
Page 22: ...22 PAGE LEFT INTENTIONALLY BLANK...
Page 30: ...30 PAGE LEFT INTENTIONALLY BLANK...
Page 56: ...56 APPENDIX A INTERCONNECT DIAGRAM...
Page 57: ...57...