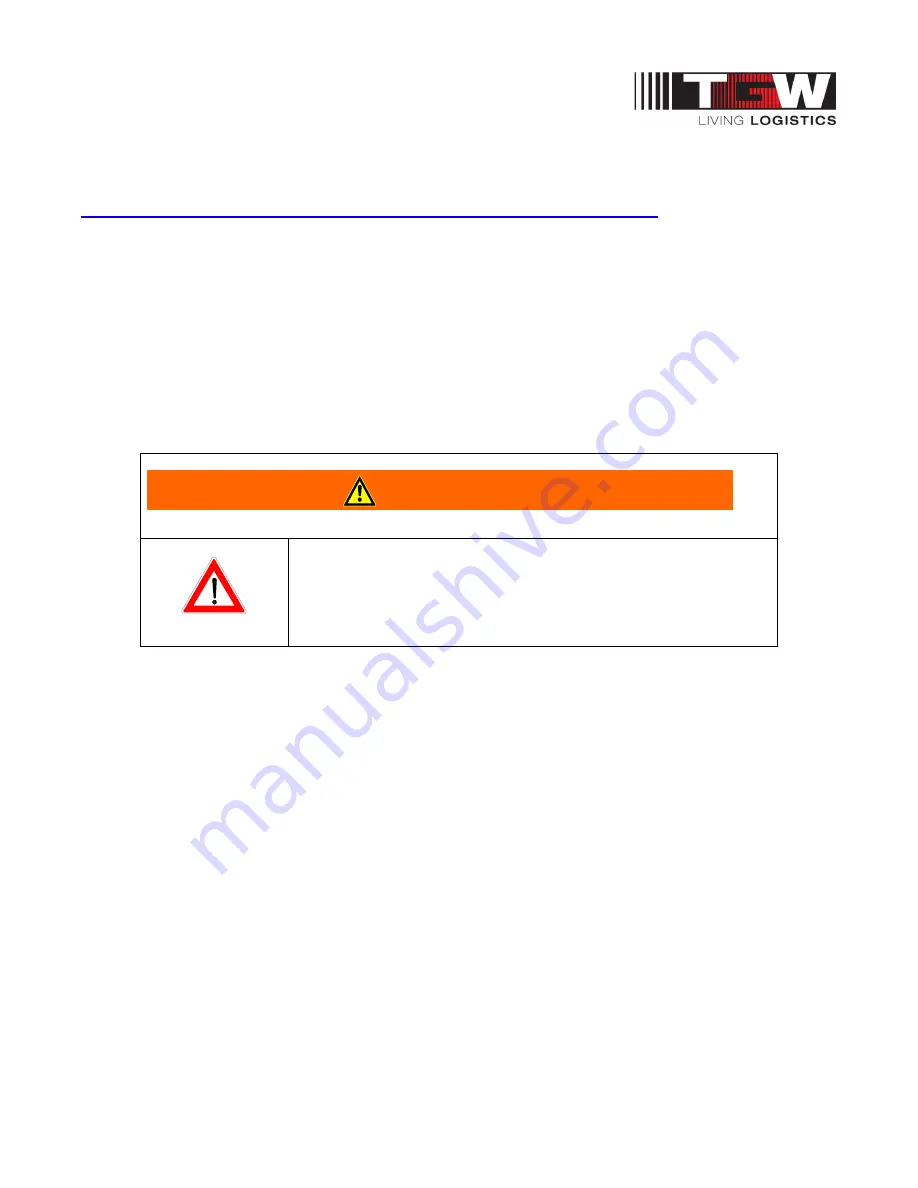
NBS®90 PolySort & SP IOM
P/N: 1193974
Revision Date: 4/25/2019
Page
41
of
83
8.7: NBS
S
UPPORTS
&
C
ONNECTIONS
For details on Supports & Connections, see Support & Connections IOM (#1200485) at
https://www.tgw-conveyor.com/support/iom-manuals/supports-and-connections
Anchoring
Anchoring in concrete floors is accomplished by drilling into the floor and inserting the suitable anchor
bolt. The hole diameter and depth must be in accordance with the anchor bolt manufacturer’s
instructions, and all applicable codes and requirements.
Anchor intermediate floor supports with two anchor bolts, one through each support foot plate using
minimum 3/8” diameter anchor bolts. Stagger anchors from front hole on one side to rear hole on
opposite side. For floor supports, over 5’ minimum use 1/2” diameter anchor bolts. Anchor bolts for
equipment subject to impact loads should be a minimum of 1/2” diameter or as superseded by any
other applicable code.
•
Place a bolt through the frame and support immediately with
finger tight nut. This will prevent the frame from falling off the
support, if bumped, and causing injury.
Bed/Support Connectors
NBS can
ONLY
be supported at bed joints. Install the sortation conveyor (drive bed thru end pulley) on
supports. Leave approximately 1/16″ gap between low friction rail joints. The conveyor must be level
and straight. Adjoining beds are connected using 3/8″ thick by 10″ nut plate, 3/16″ thick by 10″ clamping
plate and 3/8″ hardware. These parts are shipped with other loose parts. Insert 10″ nut plate halfway
into the formed channel end of each bed.
Mount standhead support with two 3/8-
16 x 1″ hex head bolts with flat
and lock washers. After that
mount 10″ clamp plate to channel ends with four 3/8
-
16 x 1″ hex head bolts with nut, flat and lock
washers (see picture below). It can be seen that a crossmember could be moved into the recessed
area of the standhead support bracket if needed.
Maintaining the rigidity and flatness of the conveying surface is the end result of proper support
installation.
WARNING