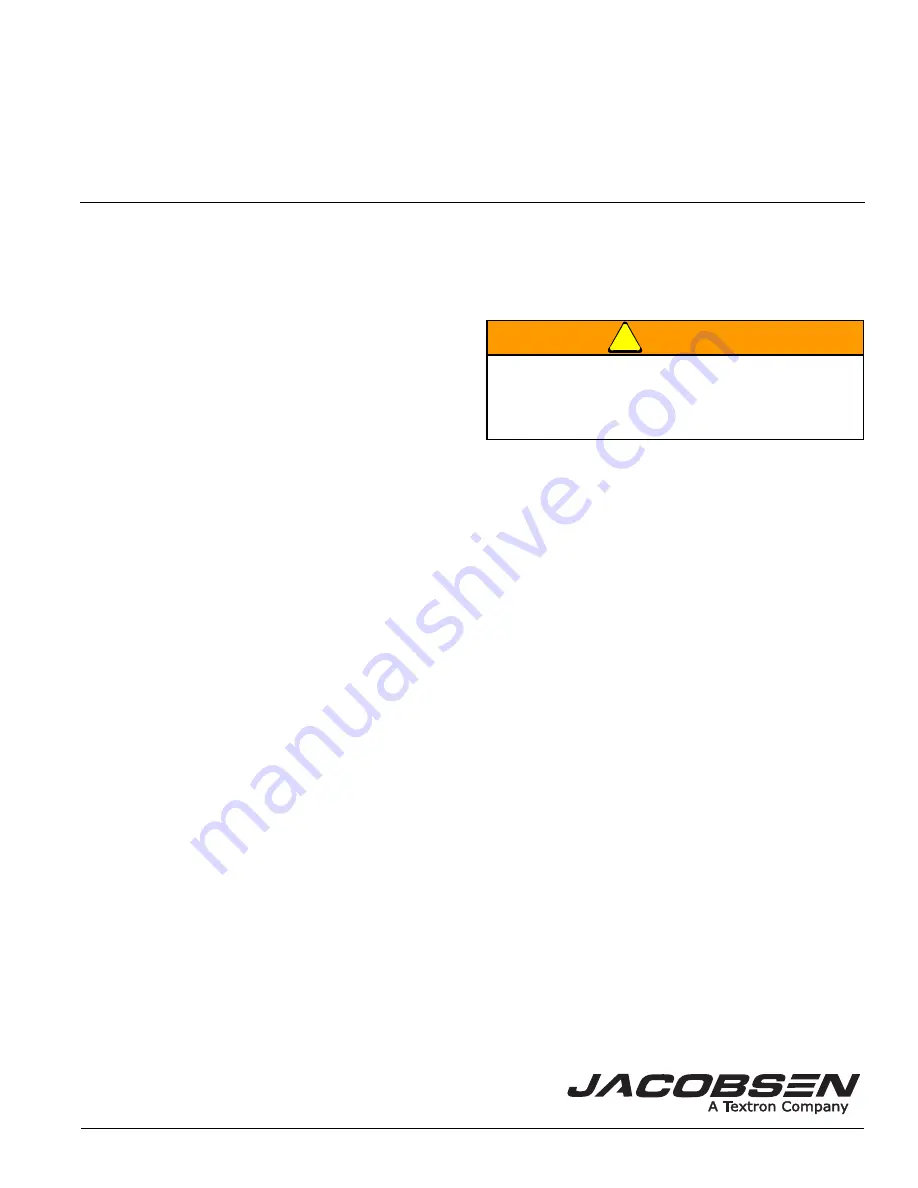
4203781 First Edition
3
Foreword
General
This manual provides detailed information and
procedures to safely repair and maintain the following:
Jacobsen
R-311 rotary mowers and associated
accessory attachments
This manual is intended to introduce and guide the user
through the latest factory-approved troubleshooting and
repair techniques and practices.
Before you attempt to troubleshoot or make repairs, you
must be familiar with the operation of this machine. Refer
to the operator’s manual and parts manual for specific
information on these topics.
THE INFORMATION CONTAINED IN THIS MANUAL IS
BASED ON MACHINES MANUFACTURED UP TO THE
TIME OF PUBLICATION. JACOBSEN RESERVES THE
RIGHT TO CHANGE ANY OF THIS INFORMATION
WITHOUT NOTICE.
California
Proposition 65 Warning
!
WARNING
Trademark Acknowledgement
Jacobsen acknowledges the following trademarks for
company names or products mentioned within this
publication:
Lubriplate
®
is a trademark of Fiske Brothers Refining Co.
Loctite
®
and Permatex
®
are trademarks of Henkel
Corporation.
Certain vehicle components contain or emit
chemicals known to the State of California to
cause cancer and birth defects or other
reproductive harm.
Summary of Contents for JACOBSEN R-311 69166
Page 1: ...R 311 Rotary Mower Technical Repair Manual 69166...
Page 3: ......
Page 7: ......
Page 10: ...SAFETY 4203781 First Edition 1 3 1 Figure 1 1 TN2166 TN2167 6 7 8 9 2 5 4 10 1 2 3...
Page 29: ...2 12 4203781 First Edition SPECIFICATIONS AND GENERAL INFORMATION 2 Page Intentionally Blank...
Page 51: ...3 22 4203781 First Edition ENGINE 3 Page Intentionally Blank...
Page 68: ...ELECTRICAL 4203781 First Edition 4 17 4 Page Intentionally Blank...
Page 84: ...ELECTRICAL 4203781 First Edition 4 33 4 Page Intentionally Blank...
Page 87: ...4 36 4203781 First Edition ELECTRICAL 4 Page Intentionally Blank...
Page 91: ...4 40 4203781 First Edition ELECTRICAL 4 Page Intentionally Blank...
Page 95: ...4 44 4203781 First Edition ELECTRICAL 4 Page Intentionally Blank...
Page 101: ...4 50 4203781 First Edition ELECTRICAL 4 Page Intentionally Blank...
Page 163: ...4 112 4203781 First Edition ELECTRICAL 4 Page Intentionally Blank...
Page 173: ...5 10 4203781 First Edition HYDROSTATIC POWER TRAIN 5 Page Intentionally Blank...
Page 177: ...5 14 4203781 First Edition HYDROSTATIC POWER TRAIN 5 Page Intentionally Blank...
Page 181: ...5 18 4203781 First Edition HYDROSTATIC POWER TRAIN 5 Page Intentionally Blank...
Page 185: ...5 22 4203781 First Edition HYDROSTATIC POWER TRAIN 5 Page Intentionally Blank...
Page 242: ...HYDRAULICS 4203781 First Edition 6 11 6 Page Intentionally Blank...
Page 335: ...7 26 4203781 First Edition STEERING 7 Page Intentionally Blank...
Page 387: ...9 22 4203781 First Edition ACCESSORIES AND MISCELLANEOUS REPAIR 9 Page Intentionally Blank...
Page 400: ......
Page 402: ......