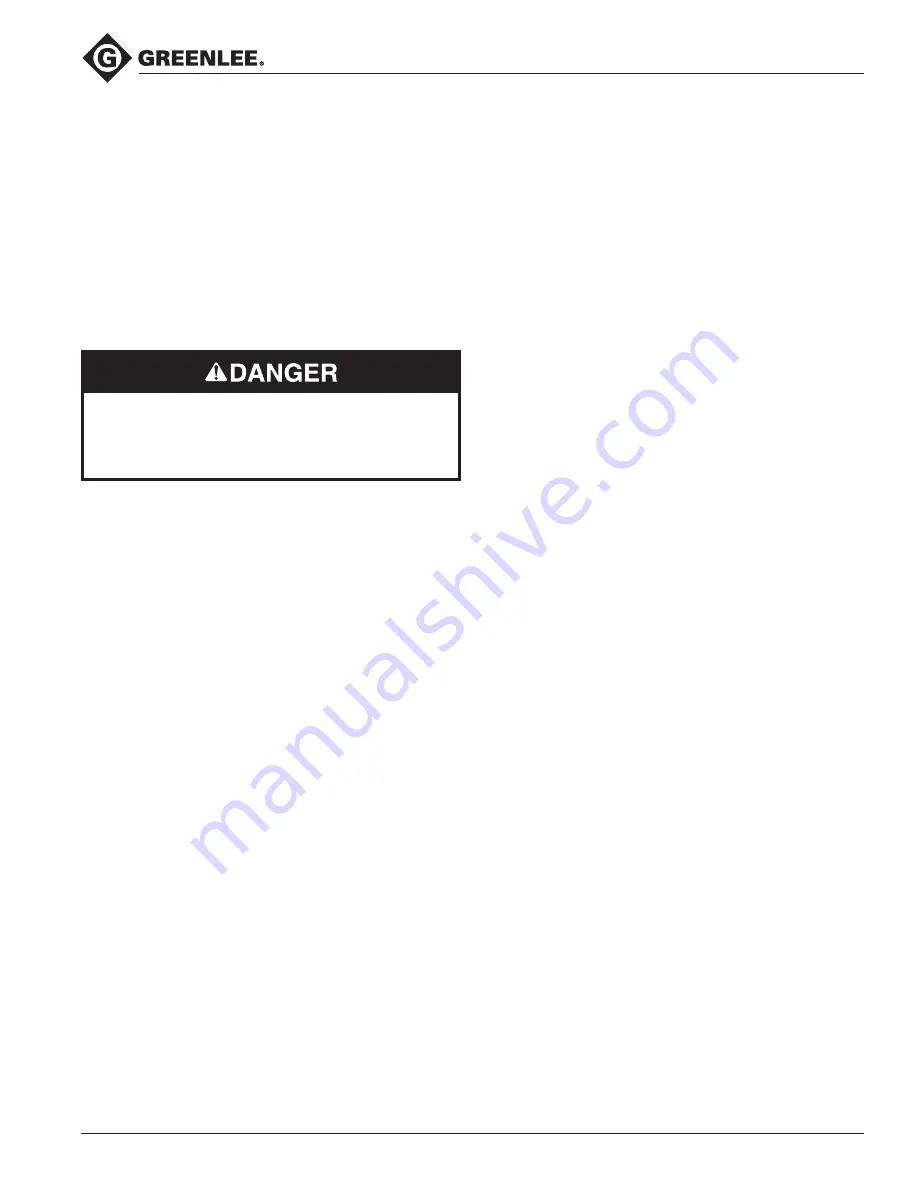
G3 Tugger
®
System
Greenlee / A Textron Company
4455 Boeing Dr. • Rockford, IL 61109-2988 USA • 815-397-7070
15
Tool service must be performed only by qualified
repair personnel.
Service or maintenance performed by
unqualified personnel could result in a risk of injury.
When servicing a tool, use only identical replace-
ment parts. Follow instructions in the “Maintenance”
section of this manual.
Use of unauthorized parts or
failure to follow maintenance instructions may create a
risk of electric shock or injury.
Maintenance
Shut off motor and unplug unit before dismantling or
servicing.
Failure to observe this warning will result in severe
injury or death.
Drive Chains
Removal
Remove the 6 screws securing the chain guards. Slide
out the chain guards—motor end first—and remove.
Remove the bolt securing the capstan to the puller and
the screw securing the drive sprocket to the motor.
Remove all the washers, noting their proper order for
reassembly. Pry off the drive sprocket while pulling out
on the capstan unit and remove both. Pull off the drive
chain. Reassemble with the connecting link retainer
facing outward.
Wear
Check to make sure all the links pivot freely without
binding. Replace the chain if any resistance is felt.
Alternately load the links in tension and compression
along the length to check for any perceptible free play.
There should be a barely detectable amount of free
play. If any joint has enough free play to be easily seen
(about 1/64"), replace the chain. Always replace the
entire chain, including the connecting link as a whole
unit.
Lubrication
Lubricate the drive chains after every 40 hours of
operation. Lubricate between the chain plates from the
inside of the loop with any high quality chain lube or an
80W–90W gear oil.
Adjustment
Loosen the 4 screws securing the motor. Push the
motor away from the capstan while retightening the
motor screws.
Capstan
Removal
See drive chain removal.
Wear
Check for wear on the outside of the capstan. If the
rope has worn a groove on the 2" diameter portion of
the capstan, replace it. Check for bearing wear. If the
brass bearing ID exceeds 1.020" or if there is visible
radial free play between the capstan and shaft, replace
the capstan and bearing assembly.
Lubrication
Lubricate the capstan shaft after every 20 hours of
operation. Liberally apply a multipurpose NLGI grade 2
grease to the capstan shaft and bearing.
Adjustment
If the capstan or puller frame is replaced, adjust the
axial free play to less than 1/32". Assemble the inner
thrust washers and capstan to the frame without the
chain. Attach with the bolt and retaining flat washer.
If the capstan binds, add 52023123 shim washers one
at a time until it rotates freely. If it has more than 1/32"
of axial free play, add 50179160 fiber washers to set the
free play at less than 1/32".
Motor
Commutator Brushes
Check the commutator brushes after every 40 hours of
operation. Remove the motor brush caps and brushes.
Measure the brush lengths. If length of either brush is
less than 3/8", replace both brushes.
Other
Anti-Reverse Pawl
Check that the pawl pivots freely on its shaft. Clean any
rust or debris from the shaft or pawl bore.
SERVICE