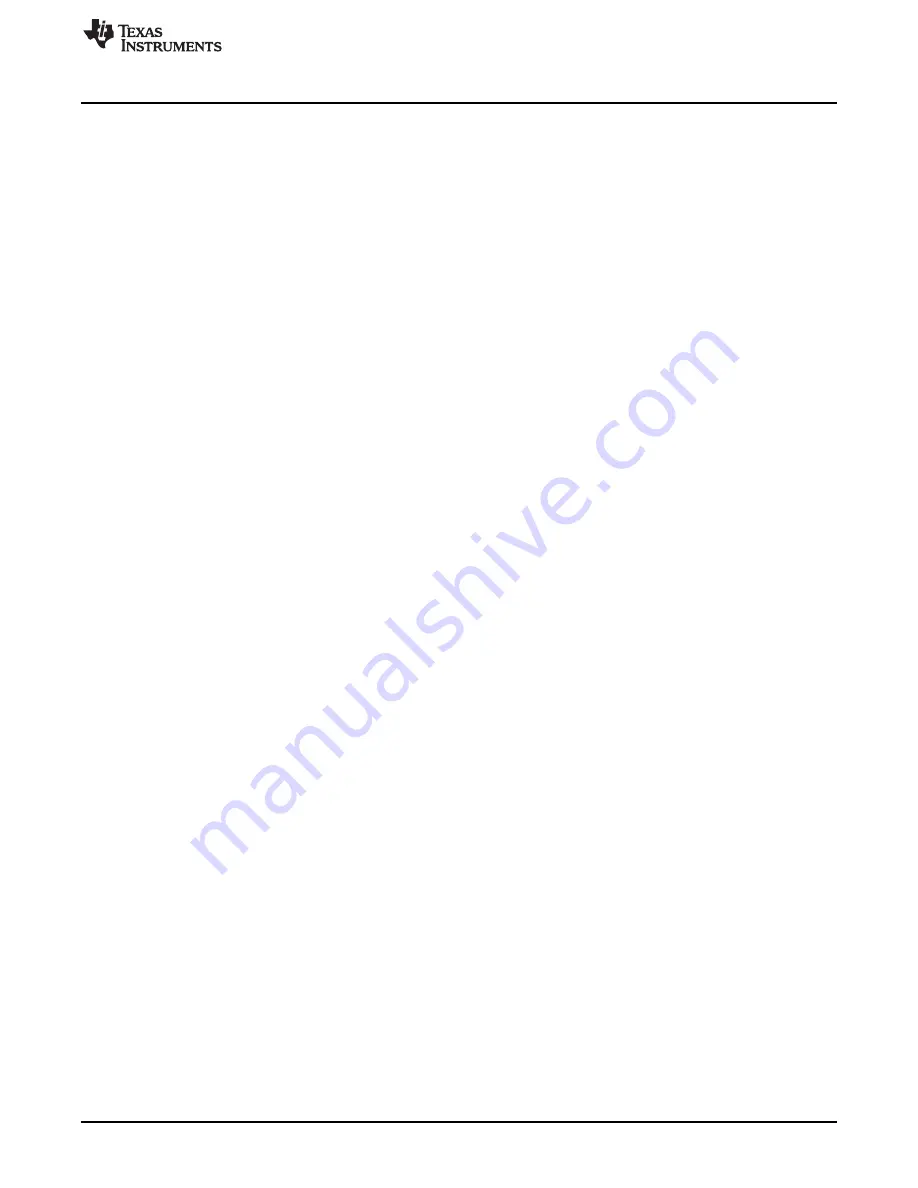
Software
25
SLDU031 – December 2017
Copyright © 2017, Texas Instruments Incorporated
PGAxxxEVM-037 Pressure Sensor Signal Conditioner Evaluation Module
One of the key features of the PGA302 pressure sensor signal conditioner is the preprogrammed firmware
which includes linearization and temperature compensation algorithms to provide reliable results from a
variety of pressure sensors in real world systems. To maximize the effectiveness of these algorithms,
calibration of the PGA302 device for each sensor is critical. The PGA302 Linearity Calibration panel
provides a simple interface to calibrate the input and output stages of the PGA302 device with minimal
external equipment. The following example procedure will walk the user through the calibration process by
using the onboard resistive bridge to simulate a pressure sensor.
4.12.1
PGA302 Linearity Calibration Procedure
1. Follow the
PGAxxxEVM-037 Quick Start Procedure
) to power up the EVM and establish
communication with the PGAxxx device. Make sure that the jumpers are set to their default position as
shown in
2. Place the microcontroller in
Reset
by clicking the
Microcontroller State
field.
3. Select the
Calibration Model
you wish to use. For this example, select “3 Pressure, 1 Temperature”
4. Click
START
at the bottom of the page, and follow the prompts from the message center below the
START
button.
5. Update the desired output voltage for Pressure 1 and click
NEXT
when finished. Repeat this process
for Pressure 2 through Pressure 4. In this case (3 Pressure, 1 Temperature), Pressure 3 is not
accessible for updating.
6. Update the desired DAC Code for Pressure 1 and click
NEXT
when finished. Repeat this process for
Pressures 2 and 4.
7. Click
NEXT
again. Check the value in the Vout 1 row under the column Temp 2. This value will be
automatically populated with the Vout voltage output associated with the DAC code entered in the
previous step. The voltage is measured by the ADC in the MSP430 microcontroller on the
PGAxxxEVM-037. If you wish to verify the voltage with an external voltage meter, measure the voltage
on the VOUT_SENT test point on the EVM. The voltage value can be left as is, or an updated value
can be manually entered by the user. Once the value is set, click
NEXT
. Repeat this process for Vout
2, and Vout 4.
8. Before continuing, set the number of
Average Samples
to use in the
Advanced Settings
section of the
page. This value can range from 1 to 128 and will average the number of samples selected to
generate the ADC value populated in the calibration algorithm. Increasing the number of samples
averaged will increase the amount of time it takes for the ADC value to populate. For this example, the
default value of 8 will be selected.
9. Set the resistive bridge leg resistance to the desired value using the
Resistive Bridge Configuration
panel. For this example use "5.0850k" as the Pressure 1 value. Click
NEXT
when finished. The cell will
be populated automatically with the value read by the ADC. If the value does not populate properly, or
if the value does not seem correct, the
Data Monitor
page (see
) can be used to help
debug by reading the ADC values in real time. The value in the cell can be manually entered at any
time by clicking the
Full Manual Data Entry
checkbox.
10. Set the resistive bridge leg resistance to the second pressure value. For this example, use "5.0806k".
Once complete, click
NEXT
to populate the ADC value in the cell. Repeat this process for the third and
final pressure point, using a resistive bridge leg resistance of "5.0713k".
11. After completing the pressure readings, click
NEXT
to populate the temperature cell. The cell will be
automatically populated with the ADC value read from the internal temperature sensor of the PGA302.
Click
NEXT
again.
12. The VDD Supply Voltage field will now be automatically populated with the value measured by the
ADC of the MSP430. If desired, the
VDD Supply Voltage
can be measured externally from the test
point labeled
VDD
on the EVM, and entered manually into the calibration page. Click
NEXT
again.
13. Now the desired
VDD Supply Voltage
field will be populated. Click
NEXT
again.
14. Click
CALCULATE
. This will use the data generated through the calibration procedure to calculate the
coefficient values for linearity and temperature compensation and display them in the message center
at the bottom of the page. Click
PROGRAM
to program the values to the EEPROM.
15. Navigate to the
PGA302 EEPROM Settings
page to verify the coefficients have been populated in the
Linearity Calibration Parameters
section of the page. While on this page, click the
UPDATE
button to
correct the EEPROM CRC value. The PGA302 device is now fully calibrated.