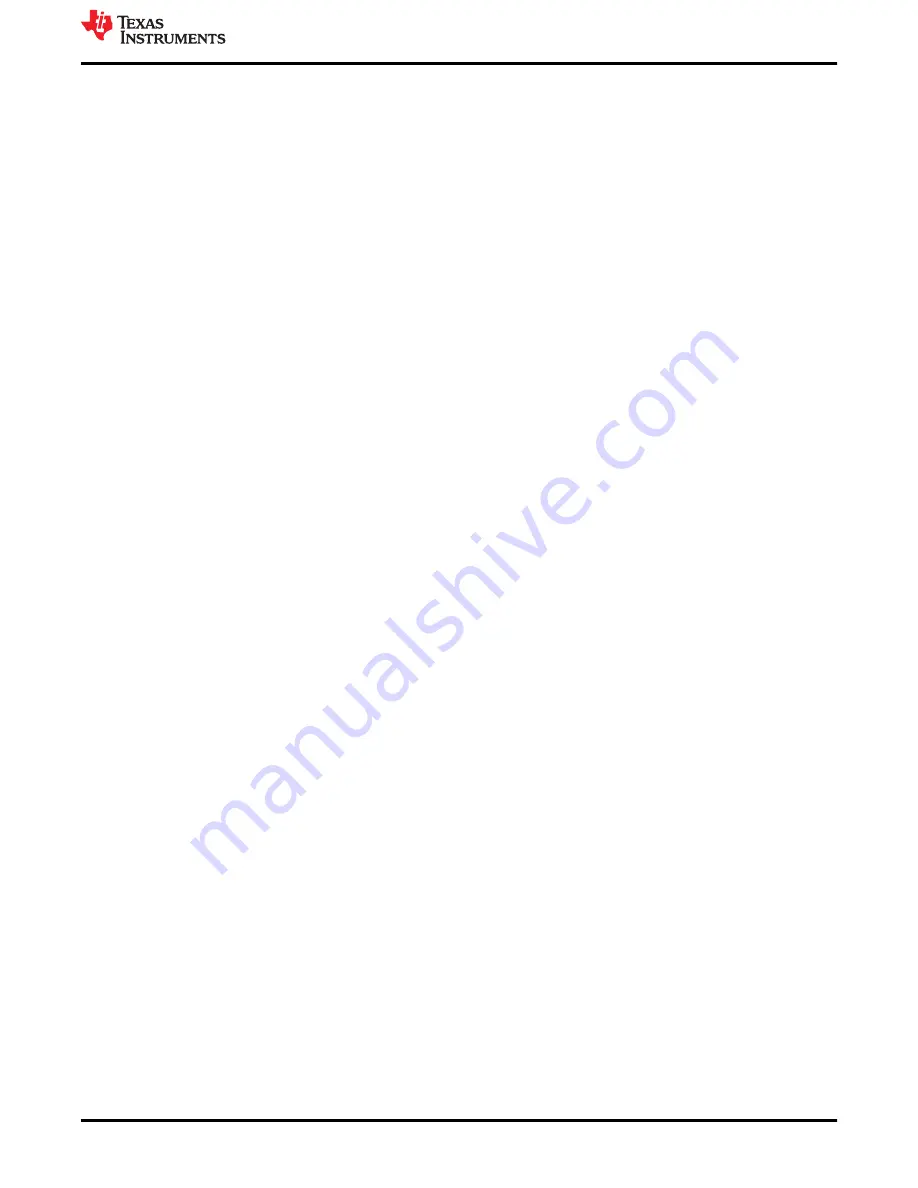
6 Operation of the EVM
6.1 Dual Motor Operation
This mode allows for up to two motors to be controlled independently. The DRV821xDSG are the only devices
that can support dual motor operation.
Use the following steps to operate the EVM with up to two loads with single direction speed control:
1. Make sure only one driver is populated and no power is being supplied to the EVM.
2. Connect a DC motor across OUT1 and GND. If desired, connect an additional DC motor across OUT2 and
GND. See
below for a diagram.
3. Adjust the potentiometer, EN/IN1 PWM and PH/IN2 PWM, to minimum voltage by turning the wheel counter-
clockwise all the way. This minimizes the motor speed of the motor connected across OUT1. If using a
second motor, perform this process with potentiometer IN2 PWM as well.
4. Remove the jumper from the MODE/nSLEEP header (J2) so the MODE pin is Hi-Z.
5. Apply power to J1 header.
6. Turn potentiometer, EN/IN1 PWM, clockwise and the motor connected across OUT1 will begin to turn.
Continue adjusting, as desired, until the maximum speed is reached. If using a second motor perform this
process with potentiometer PH/IN2 PWM as well.
7. The direction of the motor turning can be reversed by removing the connection from GND to the motor and
connecting the motor to VM. If this is done, the potentiometer associated with controlling the motor will
operate in reverse and thus should be turned all the way clockwise before powering on the board and then
slowly turned counter-clockwise to speed up the motor.
Use the following steps to operate the EVM with outputs paralleled to decrease the overall RDS(on) by half and
accommodate larger current requirements:
1. Make sure only one driver is populated and no power is being supplied to the EVM.
2. Short EN/IN1 and PH/IN2 pins on J4 with a jumper. See
.
3. Short OUT1 and OUT2 at connector J3 with an unexposed small wire or short the OUT1 and OUT2 test
points with a small cable with clips. Make sure the wire is low resistance and can support at minimum 4-A
continous peak current. Connect one end of the motor or desired load on either OUT1 or OUT2 on connector
J3 and the other end on either VM (for low-side driving) or GND (for high-side driving). See
4. Adjust the potentiometer, EN/IN1 PWM and PH/IN2 PWM, to minimum voltage by turning the wheel all the
way counter-clockwise (if one end of the motor is connected to GND) or clockwise (if one end of the motor is
connected to VCC). This minimizes the speed of the motor connected across OUT1 and OUT2.
5. Remove the jumper from the MODE/nSLEEP header (J2) so the MODE pin is Hi-Z.
6. Apply power to J1 header.
7. Turn potentiometer, EN/IN1 PWM, clockwise and the motor connected across OUT1 will begin to turn.
Continue adjusting, as desired, until the maximum speed is reached. Make sure to not move PH/IN2 PWM
potentiometer.
8. The direction of the motor turning can reversed by removing the connection from GND to the motor and
connecting the motor to VM and vice-versa. If this is done, the potentiometer associated with controlling the
motor will operate in reverse and thus should be turned all the way clockwise (if motor originally connected to
GND) or counter-clockwise (if motor originally connected to VCC) before powering on the board and then
slowly turning the EN/IN1 PWM potentiometer in the opposite direction to increase the motor speed.
Operation of the EVM
SLOU540A – NOVEMBER 2020 – REVISED DECEMBER 2020
DRV821xEVM and DRV8220EVM User's Guide
11
Copyright © 2020 Texas Instruments Incorporated