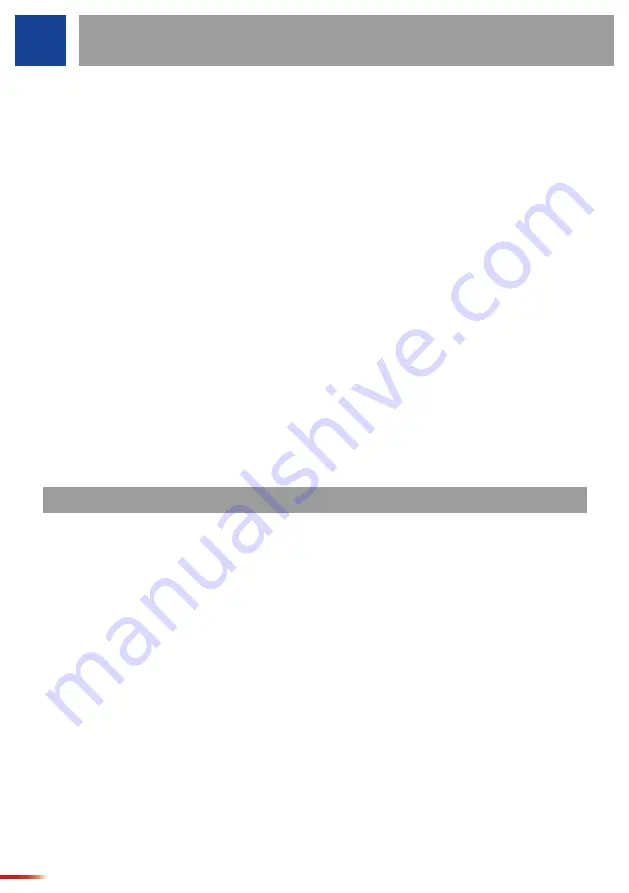
18
for the legibility of the product labelling! The use of damaged components or components sub-
jected to a fall must be discontinued at once. If there is only the slightest doubt, the product
needs to be retired or subjected to testing and by a competent person.
When using the equipment in occupational health and safety to EN 365, it must be checked at
least every 12 months by a duly qualified person strictly observing the instructions, or else by
the manufacturer, and it must, whenever necessary, be replaced. These inspections must be
documented (documentation of equipment; cf. attached Inspection Sheet). Refer to national
regulations for inspection intervals.
Such inspections must comprise:
Check general state: age, completeness, discolouration, correct assembly
Check all individual parts for mechanical damage such as: cuts, cracks, indentations,
abrasion, formation of ribs, kinks, crushing.
Check all individual parts for thermal or chemical damage such as: fusing, hardening.
Check metal components for corrosion and deformations.
Check condition and completeness of stitching
Systems damaged or subjected to a fall must be retired immediately.
If there is the slightest doubt about the suitability of the product to perform its required task,
the product must to be retired.
The actual useful life depends solely on the condition of the product, which in turn is influenced
by various factors (see below). Extreme influences may shorten service life to a single use only
or to even less if the equipment is damaged prior to its first use (e.g. in transport).
Mechanical wear and other influences such as the impact of sunlight will decrease the life span
considerably. Bleached or abraded fibres, discoloration, and hardened spots are certain indica-
tors that the product needs to be retired.
It is clearly not possible to offer a general statement about the product’s service life, as such
life span depends on various factors, e.g. UV light, type and frequency of use, handling, cli-
matic influences such as ice or snow, environments such as salt, sand, battery acid etc., heat
contamination (above normal climatic conditions), mechanical deformation and/or distortion, …
(incomplete list!),
In general, the following rule applies:
If the user, for whatever reason – however insigni-
ficant it may seem – is uncertain whether or not the product meets all the necessary criteria,
either (s)he shall reject it from service and render unusable, or place in quarantine and label it
in an obvious manner so that it cannot be used by mistake. The product may only be returned
to service following the written authorisation of a competent person.
Withdraw equipment from service if it has been used to arrest a fall.
SERVICE LIFE
REGULAR CHECKS / SERVICE LIFE
Summary of Contents for antiSHOCK
Page 9: ...35 NOTES ...