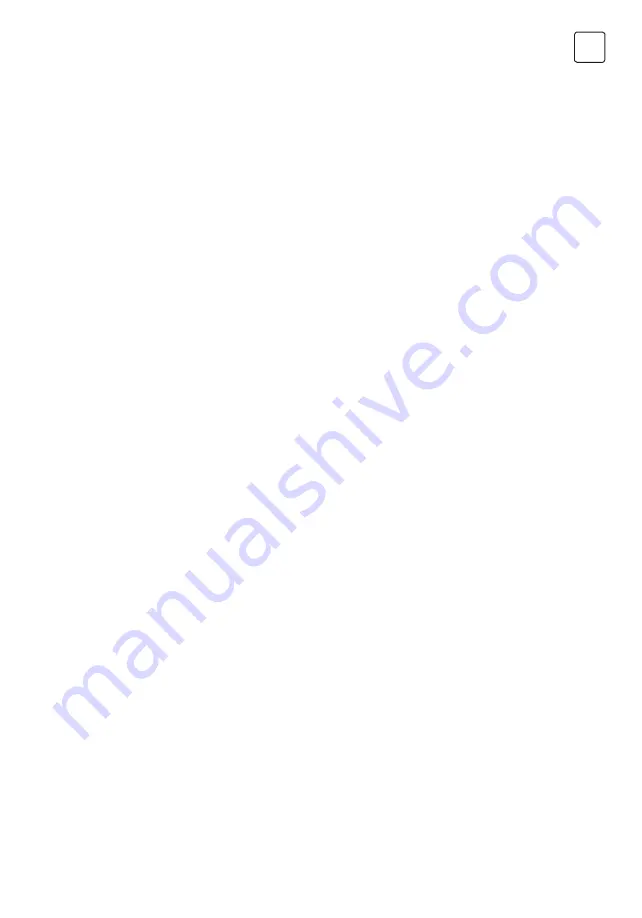
43
ENG
Replace components only with parts specified by the manufacturer. Other parts may result in the ignition of
refrigerant in the atmosphere from a leak.
19.
Cabling
Check that cabling will not be subject to wear, corrosion, excessive pressure, vibration, sharp edges or any
other adverse environmental effects. The check shall also take into account the effects of aging or continual
vibration from sources such as compressors or fans.
20.
Detection of flammable refrigerants
Under no circumstances shall potential sources of ignition be used in the searching for or detection of
refrigerant leaks. Ahalide torch (or any other detector using a naked flame) shall not be used.
21.
Leak detection methods
The following leak detection methods are deemed acceptable for systems containing flammable refrigerants.
Electronic leak detectors shall be used to detect flammable refrigerants, but the sensitivity may not be
adequate, or may need re-calibration. (Detection equipment shall be calibrated in a refrigerant-free area.)
Ensure that the detector is not a potential source of ignition and is suitable for the refrigerant used. Leak
detection equipment shall be set at a percentage of the LFL of the refrigerant and shall be calibrated to the
refrigerant employed and the appropriate percentage of gas (25 % maximum) is confirmed.
Leak detection fluids are suitable for use with most refrigerants but the use of detergents containing chlorine
shall be avoided as the chlorine may react with the refrigerant and corrode the copper pipe-work.
If a leak is suspected, all naked flames shall be removed/ extinguished.
If a leakage of refrigerant is found which requires brazing, all of the refrigerant shall be recovered from the
system, or isolated (by means of shut off valves) in a part of the system remote from the leak. Oxygen free
nitrogen (OFN) shall then be purged through the system both before and during the brazing process.
22.
Removal and evacuation
When breaking into the refrigerant circuit to make repairs or for any other purpose conventional procedures
shall be used. However, it is important that best practice is followed since flammability is a consideration. The
following procedure shall be adhered to:
- Remove refrigerant;
- Purge the circuit with inert gas;
- Evacuate;
- Purge again with inert gas;
-Open the circuit by cutting or brazing.
The refrigerant charge shall be recovered into the correct recovery cylinders. The system shall be flushed
with OFN to render the unit safe. This process may need to be repeated several times. Compressed air or
oxygen shall not be used for this task.
Flushing shall be achieved by breaking the vacuum in the system with OFN and continuing to fill until the
working pressure is achieved, then venting to atmosphere, and finally pulling down to a vacuum. This process
shall be repeated until no refrigerant is within the system. When the final OFN charge is used, the system shall
be vented down to atmospheric pressure to enable work to take place. This operation is absolutely vital if
brazing operations on the pipe-work are to take place.
Ensure that the outlet for the vacuum pump is not close to any ignition sources and there is ventilation
available.
23.
Decommissioning
Before carrying out this procedure, it is essential that the technician is completely familiar with the equipment
and all its detail. It is recommended good practice that all refrigerants are recovered safely. Prior to the task
being carried out, an oil and refrigerant sample shall be taken in case analysis is required prior to re-use of
reclaimed refrigerant. It is essential that electrical power is available before the task is commenced.
a. Become familiar with the equipment and its operation.
b. Isolate system electrically.
c. Before attempting the procedure, ensure that:
- mechanical handling equipment is available, if required, for handling refrigerant cylinders;
- all personal protective equipment is available and being used correctly;
- the recovery process is supervised at all times by a competent person;
- recovery equipment and cylinders conform to the appropriate standards.
d. Pump down refrigerant system, if possible.
e. If a vacuum is not possible, make a manifold so that refrigerant can be removed from various parts of the
system.
f. Make sure that cylinder is situated on the scales before recovery takes place.
g. Start the recovery machine and operate in accordance with manufacturer’s instructions.
h. Do not overfill cylinders. (No more than 80 % volume liquid charge).
i. Do not exceed the maximum working pressure of the cylinder, even temporarily.
Summary of Contents for TM28AF21-0932IAW
Page 71: ...100 BG III 50 cm 8...
Page 72: ...101 BG...
Page 73: ...102 BG...
Page 76: ...105 BG 2 LRO3 AAA 1 5V 1 2 C F 1 5 2 C F 3 5 1 2 3 4 1 m FAN COOL AUTO FAN...
Page 80: ...109 BG 2 5 3 ON OFF 1 2 4m2 3 4 4m2 5 6 7 8 9...
Page 81: ...110 BG 10 11 12 13 14 15 16 1 2 3 4 5 CO2 6 7...
Page 82: ...111 BG 8 9 17 1 2 18 19 20 21...
Page 83: ...112 BG LFL 25 OFN 22 OFN OFN OFN 23 a b c d e f g h 80 i j k 24 25...
Page 88: ...117 BG I II 2 1 2 1 3 4 5...
Page 90: ...119 BG 5 3 4 5 6 7 R32 1 2 3...
Page 91: ...120 BG 6 7 1 2 3 4 5 6 7 8 1 2 I II 8 1 2 3 4...
Page 92: ...121 BG 1 I II III IV 4 7 V VI VII 1 2 3 4 5 6 7 30cm 30cm 200cm 50cm 50cm...
Page 93: ...122 BG 2 3 4 1 2 3 1 2 3 4 4 5 1 2 3 4 4 4...
Page 94: ...123 BG 5 6 1 2 3 4 5 1 2 3 4 5 6 15 0 1 MPa 76 cmHg 7 8 5 0 005 MPa 9 1 4 5 10 11 12 13...
Page 95: ...124 BG e 3...
Page 97: ...126 BG 1 2 3...
Page 98: ...127 BG TIMER ON DISPLAY...
Page 99: ...128 BG https tesla info wp content uploads pdf TeslaTMWiFiapp pdf...
Page 101: ...130 24 13 12 TESLA 1 2 2 1 2 2 TESLA 2 3 2 4 2 5 2 6 2 7 2 8 2 9 2 10 2 11...
Page 102: ...131 2 12 3 4 5 6 7 8 112 115 119 112 1 2 1 2 3 113 1 2 3 2 114 4 5 114 1 113 1 2 2 3...
Page 103: ...132 115 4 115 1 2 1 3 1 1 10 02 9700970 02 9700971 9 30 19 00 10 00 16 00...
Page 104: ...133...
Page 105: ...134 GR 50 cm 8...
Page 106: ...135 GR...
Page 107: ...136 GR...
Page 110: ...139 GR 2 LRO3 AAA 1 5V 1 2 o C o F 1 5 2 o C o F 3 5 1 2 3 4 1 m COOL FAN...
Page 114: ...143 GR R32 1 2 4 m2 3 4 4 m2 5 6 7 8 9 10 11 12 13 14 15 16 1 ON OFF...
Page 115: ...144 GR 2 3 4 5 CO2 6 7 8 9 17 1...
Page 116: ...145 GR 2 18 19 20 21 LFL 25 OFN 22 OFN OFN OFN...
Page 117: ...146 GR 23 80 24 25...
Page 119: ...148 GR 1 2 3 1 2 R32 548 C 3 4 5 15 6 7...
Page 122: ...151 GR I II 2 1 2 1 3 4 5...
Page 123: ...152 GR 3 4 1 2 70 mm 3 70mm 5 mm 10 mm 4 1 1 3 2 5 10mm...
Page 124: ...153 GR 5 3 4 5 6 7 R32 1 2 3 teflon...
Page 125: ...154 GR 6 7 8 1 2 3 4 5 6 7 8 1 2 1 2 3 4 I II...
Page 126: ...155 GR 1 I II III IV 4 7 V VI VII 1 2 3 4 5 6 7 A H A 30cm 30cm 200cm 50cm 50cm...
Page 127: ...156 GR 2 3 4 1 2 3 1 2 3 4 4 5 1 phillips 2 3 4 4...
Page 128: ...157 GR 5 6 1 2 3 4 5 6 1 2 3 4 5 6 15 0 1 MPa 76 cmHg 7 8 5 0 005 MPa 9 1 4 5 10 11 12 13...
Page 129: ...158 GR 3...
Page 131: ...160 GR 1 2 3...
Page 132: ...161 GR...
Page 133: ...162 GR SmartWiFi https tesla info wp content uploads pdf TeslaTMWiFiapp pdf...
Page 135: ...164 7 service TESLA TESLA 8 9 TESLA 10 email warranty gr comtrade com...
Page 136: ...165 1 Service 2 Service 3 Service 4 Service 5 Service 6 Service 7 Service 8 Service 9 Service...
Page 169: ...www tesla info...