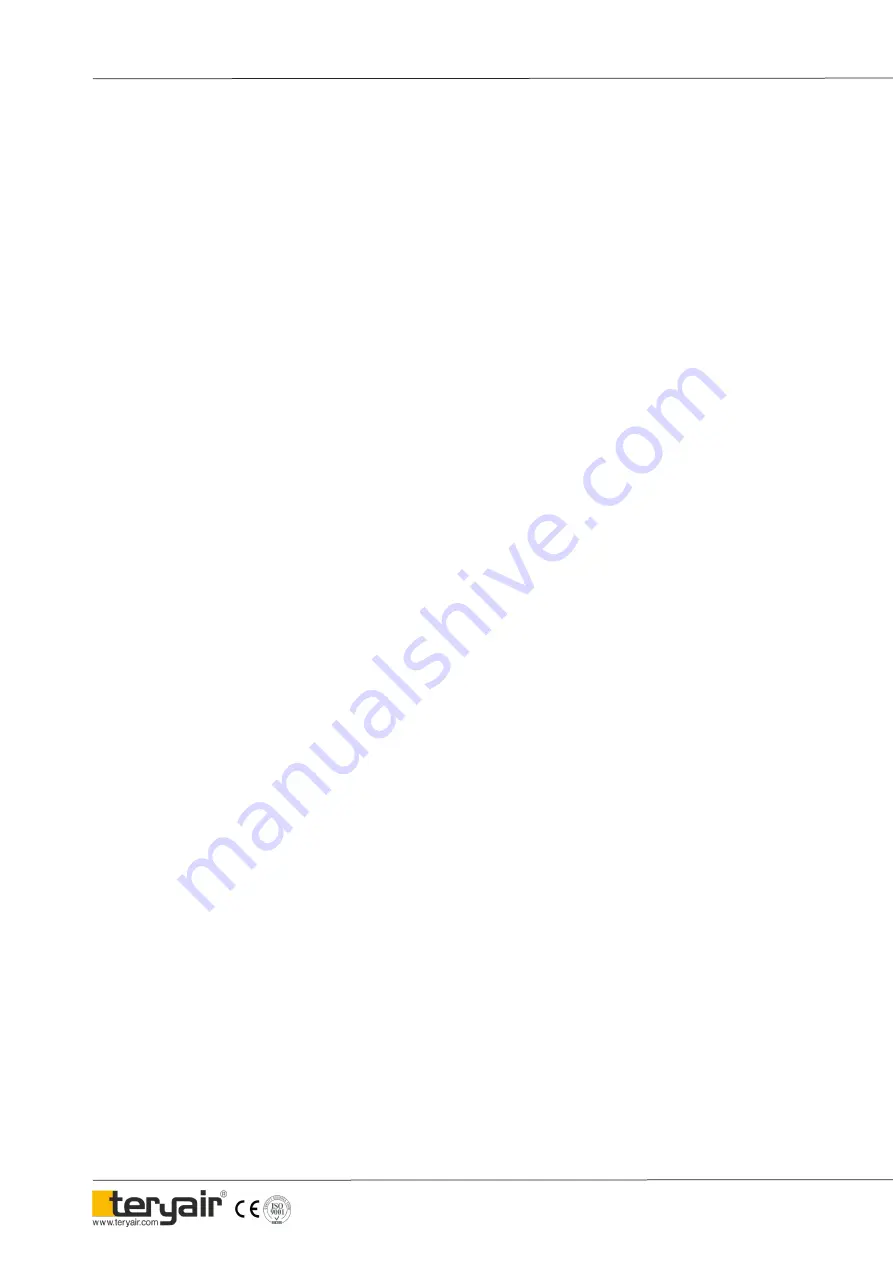
FF-MM-407-REV - 00
Page 4
Operation and Maintenance Guide Pneumatic Angle Grinder
Daily Before Operation
Disconnect and pour in 1 to 2 ounces of
recommended oil into the air inlet and recon-
nect hose after blowing out any accumulated
dirt in the hose line before connection. Tighten
both spindle nuts properly
Air Supply
To enable the tool to function satisfactorily ,it is
essential that a constant 80 PSI pressure of clean
dry air issupplied to the Inlet Nipple. A short
leader hose of 9.5 mm I.D. should be attached
to the tool and length of the hose should be
less than 12 meters. The installation of air line
separator, a filter to purify and dry the air supply
(FRL unit ) recommended and should be con-
nected as close to the tool as operation allows.
Maintenance
1. Disconnect air supply and remove inlet con-
nection from Air inlet nipple (26) Unscrew
and remove air inlet nipple (26) with help
of allen key, unscrew and remove four nos
socket head screws (15) along with spring
washers (4) Hold side handle (35) in one
hand and pull out rotor housing (25) along
with complete drive assembly. Keep aside
assy. In spindle housing (13) Now pull out
drive assy. By holding pinion gear (17) Tap
out ball bearing (11) at rear end of rotor so
that rear end plate (24) will also come out .
Slide out cylinder (22) but take care not to
fall down rotor blade (21) keep aside rotor
blades (21) Now hold some flat in ithe slot
of rotor (20) and with help of wheel spanner
(33) unlock pinion gear and remove it. Tap
gently on to front end plate (18) so that it
will come out along with two ball bearings
(11) Remove bearing spacer (19) If neces-
sary tap out roll pin (32) so that lever (31)
will come out. Unscrew valve cap (27) and
press from other side valve steam (30) and
valve spring (28)
2. Now to dismantle driven side assy.- Unscrew
spindle nut (1) with help of wrench (34) out
take out grinding wheel (2) Unscrew and
remove socket head screws four nos for
wheel guard (5) along with four spring
washers (4) and remove wheel guard (5)
3. Now rest faced ball bearing (8) by
keeping same space between two jaws of
vice so that spindle (6) will
4. remain free within keep aside spacer
(12). Take a solid pin and rest it on face
of spindle and tap it so that
5. bearing (11) on spindle end will come
out .
6. Now with help of circlip piler take out
circlip (10) and again tap an end of
spindle (6) so that bevel gear (9)
7. and bearing (8) will come out . Pull out
Woodruff key (7)
8. Clean all metal parts in light solvent and
inspect carefully for signs of wear.
Replace components that
9. appear worn out or damaged . Coat parts
with recommended light oil and
reassemble carefully in the reverse
sequence.