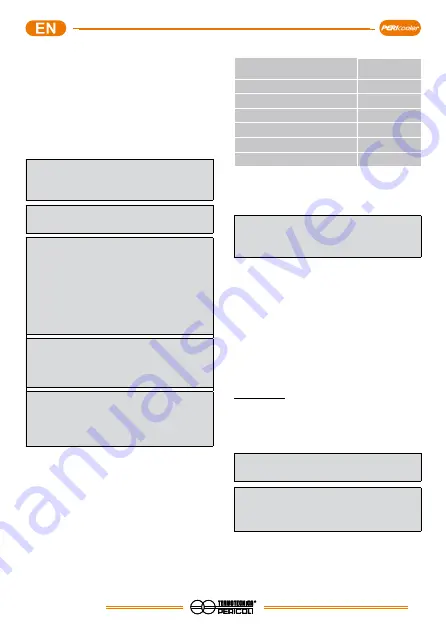
33
PERIcooler_U171200
The table below specifies the periodic ordinary checks that the
user must perform to maintain the machine in good condition
.
INTERVENTION
PERIODICITY
WATER CHANGE
weekly
MACHINE CLEANING
weekly
FILTER CLEANING
weekly
RECIPIENT CLEANING
every 15 days
CHECK OF SCREWS
quarterly
CLEANING OF HYDRAULIC SYSTEM
when needed
7.2 EQUIPMENT CLEANING
WARNING
D
o not perform cleaning operations when the cooler is running.
Even for external cleaning disconnect the machine from the
electrical supply.
Observe the following provisions, which shall be carried out
periodically to ensure proper cleaning and therefore better
functioning of the product.
• Regularly clean the motor housing with a brush or compressed
air (not blasted with water or steam)
Regular cleaning of the engine is particularly important when
the machine is working in extremely dusty or dirty environments
because the engine must be able to dissipate the heat
generated.
• The propeller blades do not require special care because they
clean themselves automatically.
• When using high pressure water for cleaning, never direct the
water or steam directly to the engine or the electric panel.
Change of water
We recommend weekly water discharge; for the correct use
of the cooler, it is appropriate to maintain a pH between 6 and
8 and not exceed the minimum 5 and maximum 9 to avoid any
problems of chemical aggression on the evaporation panel. It is
recommended, furthermore, not to exceed the hardness of 250
ppm CaCO
3
.
ATTENTION
Do not use hot water for the supply (T> 45°) in order not to create
problems to the panels, the hydraulic system and the pump body.
ATTENTION
Do not use oxidizing agents added to the water, as they can
create problems to the paper, or generally try to use a very small
amount (up to 1 ppm) in case of long-term treatment or (max. 5
ppm) in case of single treatment.
7.1 MAINTENANCE PRESCRIPTIONS
The products made by TERMOTECNICA PERICOLI S.r.l.
are
designed and made for a long duration even in very severe
working conditions.
We remind you, however, that machines with moving parts need
to be checked regularly
.
It is recommended, therefore, to implement a preventive
maintenance program, which is entrusted to specialized and
skilled staff
.
Daily inspection must be made to prevent any damage due to
harmful effects of the working environment, such as temperature,
humidity, dust, dirt, vibrations and other factors.
ATTENTION
Before performing any maintenance, make sure that the cooler
is not connected to the power grid, where electricity supply is
present, disconnect the switch or unplug from the power line.
ATTENTION
Maintenance has to be carried out only by qualified personnel in
accordance with the safety regulations.
ATTENTION
Protection against “biological risks” in the case of
maintenance:
Recycled water may contain chemical or biological pollutants
that may be harmful to health if inhaled or swallowed, therefore
the staff who is directly exposed to the output airflow must wear
breathing protection (mask) approved by competent authorities or
pursuant to Directive 89/686/EC.
N.B.: It is recommended that the managers or people in charge
of maintenance refer to the Eurovent 9/5 guide to prevent
biological contamination in evaporation cooling systems.
ATTENTION
To ensure a high level of security, use only original parts available
from your own supplier. In case of using parts that are not original,
there is no guarantee of full functionality and compliance with EC
directives on electrical safety and electromagnetic compatibility.
AVVERTENZA
In case of intervention to the machine, it is necessary that all staff
should be aware of this.
In the case of maintenance intervention one must put a signaling
panel above the power switch to prevent any accidental action
from
another operator
.
Periodically, perform the following operations:
• Make sure the inlet and outlet openings of the air are clean and
without any objects in them.
• Check cable connections and connectors. In case of unsafe
connections, damaged cables or other abnormalities, immediately
stop the machine and contact specialized technicians or support.
• Check for loose or rusted bolts or nuts because of environmental
conditions. In case of detection strengthen or replace them.
• Check for any deposits inside the machine. In case of detection,
remove them using compressed air jet.