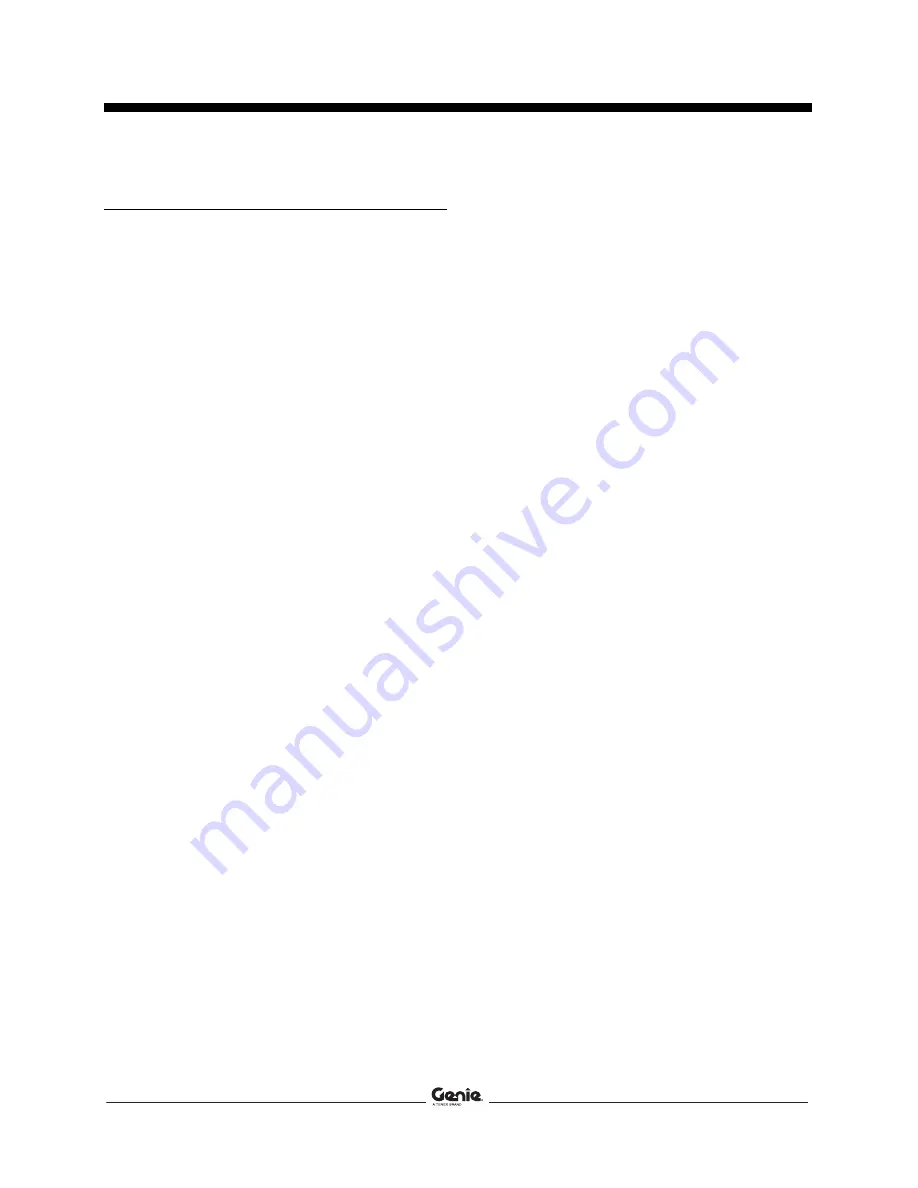
Second Edition • First Printing
Operator's Manual
Inspections
Part No. 1297733GT
QS
™
-12W • QS
™
-15W • QS
™
-20W 23
Pre-operation Inspection
Be sure that the operator’s, safety, and
responsibilities manuals are complete, legible
and in the storage container located in the
platform.
Be sure that all decals are legible and in place.
See Inspections section.
Check for hydraulic oil leaks and proper oil
level. Add oil if needed. See Maintenance
section.
Check for battery fluid leaks and proper fluid
level. Add distilled water if needed. See
Maintenance section.
Check the following components or areas for
damage, improperly installed, or missing parts and
unauthorized modifications:
Electrical components, wiring, and
electrical cables
Hydraulic power unit, reservoir, hoses,
fittings, cylinders and manifolds
Battery pack and connections
Drive motors
Tires and wheels
Ground strap
Limit switches, alarms and horn
Beacons (if equipped)
Nuts, bolts and other fasteners
Platform entry mid-rail or gate
Sequencing cables and pulleys
Wear pads
Pothole guards
Lanyard anchorage points
Work trays and bike racks (if equipped)
Brake release components
Battery cover
Mast columns and counterweight
Platform control joystick
Platform overload components
Check entire machine for:
Cracks in welds or structural components
Dents or damage to machine
Excessive rust, corrosion or oxidation
Verify that all structural and other critical
components are present and all associated
fasteners and pins are in place and properly
tightened.
Note: If the platform must be raised to inspect the
machine, make sure that the battery cover is in
place to prevent the mast sections and platform
from coming down. See Operating Instructions
section.
Summary of Contents for Genie QS-12W
Page 57: ......