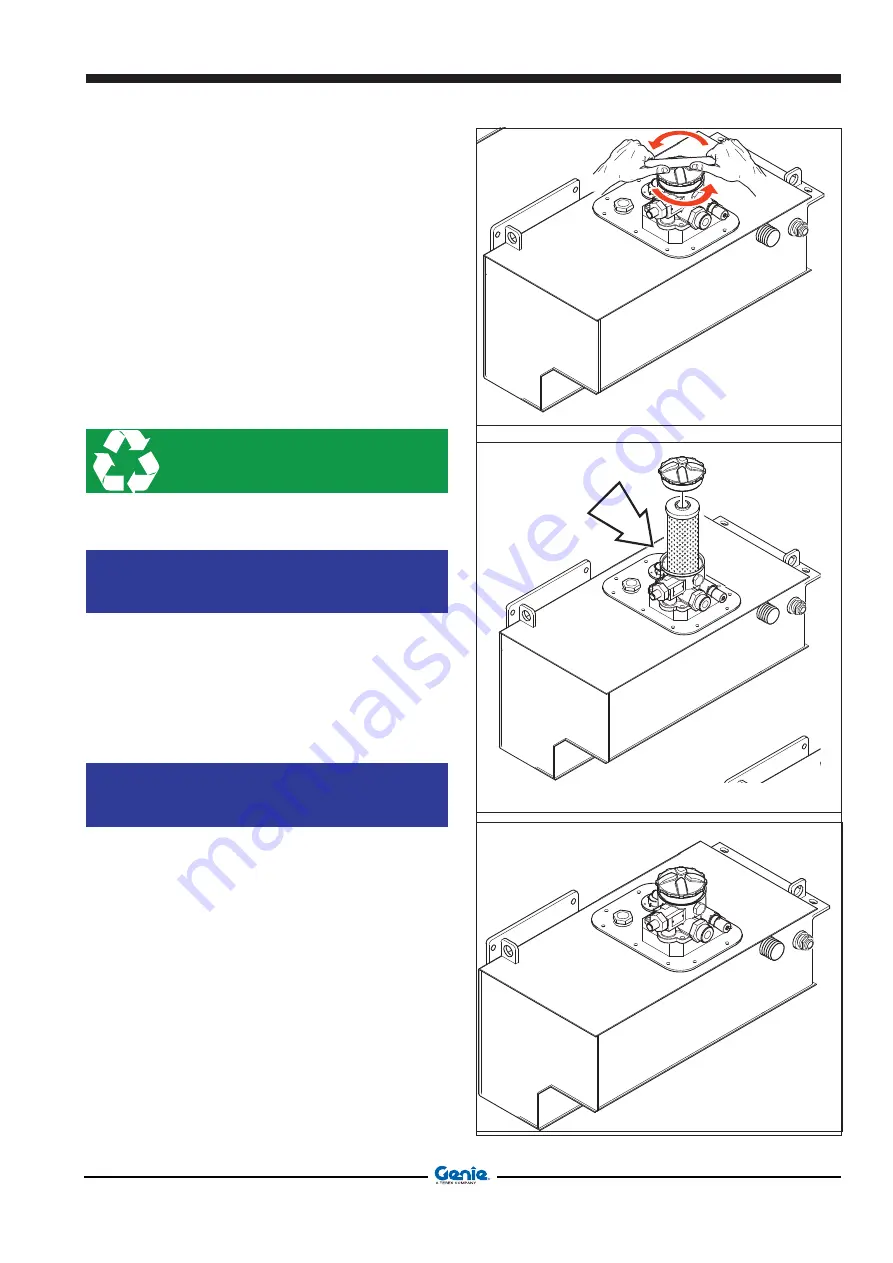
Document 57.0009.0427
47
GTH-4017EX GTH-4514EX GTH-4013EX
November 2008
Section 4 - Maintenance Procedures
TABLE
D
D-5 CHANGE THE HYDRAULIC OIL FILTER
CARTRIDGE (GTH-4013EX)
To change the hydraulic oil filter element, proceed as
follows (GTH-4013EX):
- Stop the machine on a level ground and engage the
parking brake.
- Place a container of suitable size under the filter to
collect any oil leaks.
- Remove the filter cover
B
to check the cartridge
C
.
- Change the filter element
C
, then, before fitting a
new one, thoroughly clean and grease both seat and
gasket.
- Refit and tighten the filter cover.
PROTECT THE
ENVIRONMENT
Handling and disposing of used oils may be ruled by
local or national regulations. Address to authorised
waste centres.
NOTICE
Hydraulic oil filter canisters cannot be cleaned or
washed and refitted.
They must be replaced with new ones of the type
recommended by the manufacturer:
Flow rate l/1’ = 150
Filtering = 10
π
Attachment = 1” 1/4 BSP
NOTICE
When changing the oil, drain it when it is still hot and
the polluting substances are in suspension.
C