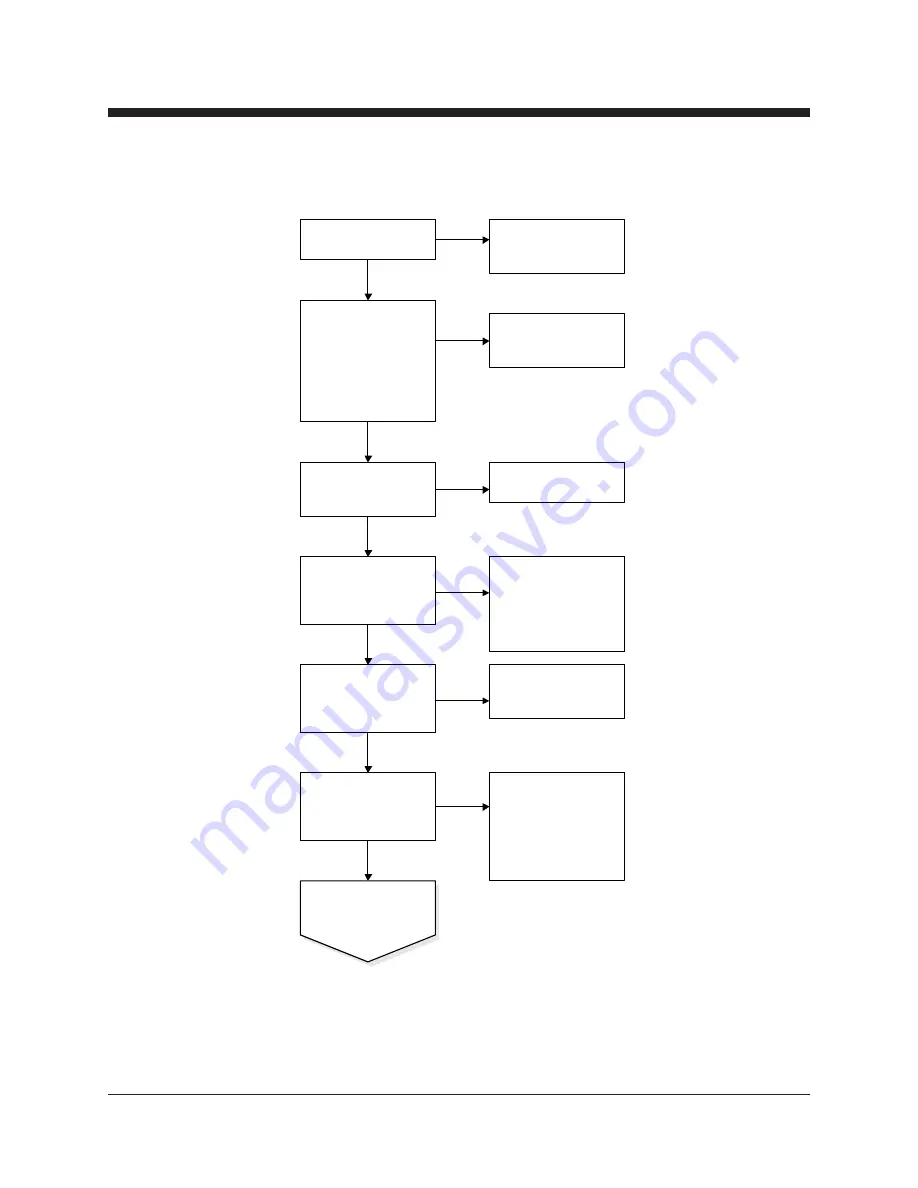
Part No. 40462
DPL-25S • DPL-30S • DPL-35S Super Series
5 - 3
September 2016
Section 5 - Troubleshooting Flow Charts
Power Light Will
Not Turn On -
AC Models
Be sure the keyswitch is
in the appropriate
position.
Be sure the Emergency
Stop buttons are pulled
up to the
ON
position.
Be sure the ground
control box PC board
fuse is not blown.
Chart 1
Check the power supply
with a voltage meter.
0V AC
Plug into a different
power supply and
recheck the voltage.
110V AC
Check the voltage at
terminal 3 on the key
switch N.O. contact. Put
Pos. lead of voltage
meter on terminal 3 and
Neg. lead on the white
wire from the AC power
cord.
0V AC
Repair or replace the AC
power cord and/or the 12/
3 cable.
Check the voltage at
terminal 4 on the key
switch N.O. contact.
Check the voltage at
terminal 2 on the
Emergency Stop button
N.C. contact.
Replace the key switch
N.O. contact.
Check the voltage at
terminal 1 on the
Emergency Stop button
N.C. contact.
Trace the black wire from
terminal 1 on the
Emergency Stop N.C.
contact back to the key
switch N.O. contact and
repair open in wire.
Replace the Emergency
Stop button N.C.
contact.
Check the voltage at the
black transformer wire
where it connects to the
brown transformer wire.
Repair open in the yellow
transformer wire between
the Emergency Stop
button and the
transformer OR replace
the transformer because
of a faulty thermal fuse.
110V AC
0V AC
110V AC
0V AC
0V AC
110V AC
0V AC
Continued on the next
page.
110V AC
110V AC