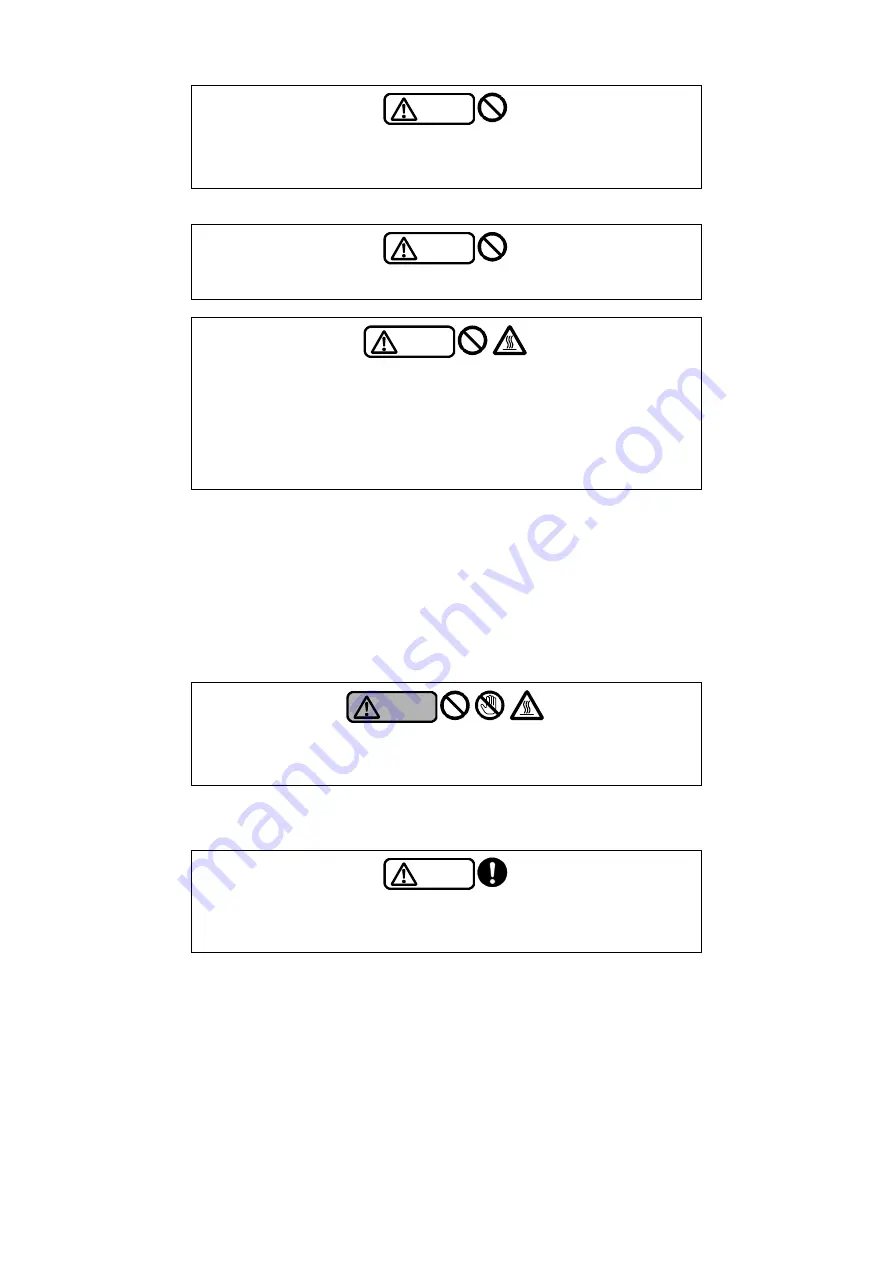
4-3
Caution
Do not check the rotational direction by the idling of the pump. Running the
pump dry even for a short time may cause damage of the sliding parts (e.g.
mechanical seals and bearings) in the pump, leakage or unusual noise.
Caution
Avoid reverse rotation because it may cause failures.
Caution
Do not run the pump dry, and do not allow air or a large amount of foreign
matter to get into the pump. Failure to observe this may cause damage of
the sliding parts (e.g. mechanical seals and bearings) in the pump,
pumping disabled, leakage or unusual noise. Moreover, the pump heats up
and causes the operator to suffer a burn. After installing the pump, release
air through the air vent, and then supply liquid in the pump above the
minimum level.
(2) If the air vent valve is installed on the pump, slightly open the air vent valve at the time of startup,
and confirm that the liquid is discharged. After the confirmation, close the air vent valve securely.
(3) Turn on the power to start the pump.
(4) Do not perform the zero-discharge operation. Failure to observe this may increase the liquid
temperature in the pump and damage the mechanical seals. If the zero-discharge operation is not
avoidable, allow a small amount of liquid to flow (3L/min), for example, by providing a bypass
circuit. If you no longer use the liquid, stop the pump. If the liquid temperature rises to a certain
level, it may reduce the service lives of the motor and pump parts.
Warning
Avoid running the pump in zero-discharge condition. Failure to observe this
may increase the liquid temperature in the pump, resulting in an
unexpected failure.
(5) When initially circulating the liquid by pump operation, gradually open the sluice valve on the
discharge side to perform circulation cleaning at the flow rate (flow velocity) used or higher.
Caution
Before restarting the pump, be sure to check that the pump has stopped
completely. Turning on the power while the pump is still rotating causes an
excessive torque on the pump and may cause failures.
(6) Adjust the sluice valve on the discharge side to the specified pressure.
(7) When the liquid level is too low, the pump may take air in and decrease the discharge rate, thus
making it impossible to pump the liquid. Keep the liquid level above the minimum liquid level
indicated in the outline drawing. Note that, however, this liquid level changes depending on
viscosity and liquid surface condition. For safety, set the liquid level high enough, but at a level
below the "maximum liquid level" indicated in the outline drawing.
(8) Limit the startup and stop frequencies to 60 times per hour as a guide.