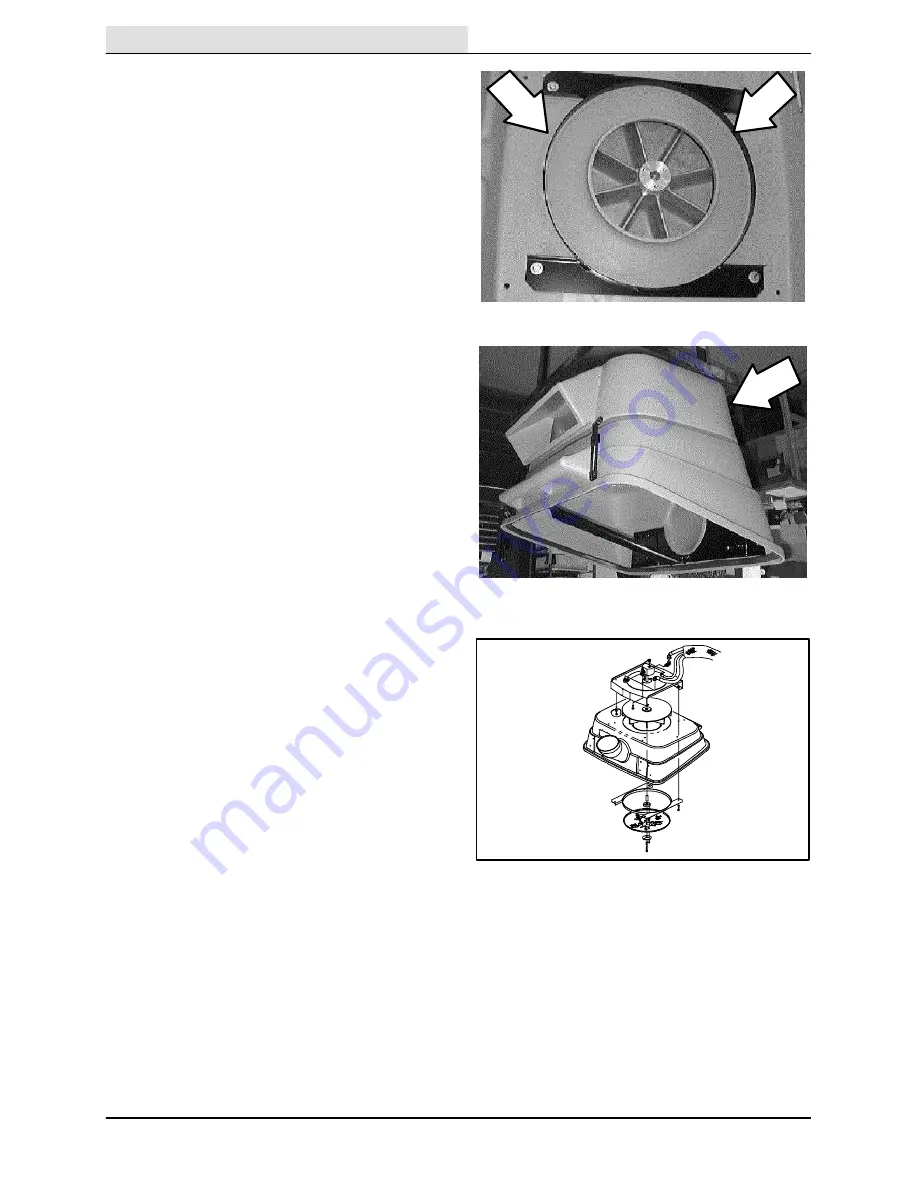
HYDRAULICS
5-14
ATLV 4300 330495 (10--98)
19. After the screen has been tighten down,
center the string guard (on the retainer
plate) around the outside of the screen.
Tighten the four screws to 18 -- 24 Nm
(15 -- 20 ft. lb).
20. Reinstall cover assembly onto the hopper
plenum.
21. Reinstall six hex screws holding the cover
assembly to the hopper plenum. Tighten the
screws to 18 -- 24 Nm (15 -- 20 ft. lb). Use
blue loctite (242) on the threads of this
hardware.
NOTE: Observe hydraulic cleanliness
requirements when opening hydraulic lines.
22. Reconnect the hydraulic lines leading to the
vacuum fan motor. See hydraulic schematic
in this section.
23. Reinstall the six screws holding the vacuum
fan motor cover plate to the top of the
plenum assembly on top of the hopper
cover. Tighten the screws to 18 -- 24 Nm
(15 -- 20 ft. lb).
24. Tilt the hopper forward and close the cover.
25. Operate the machine and check the vacuum
fan for proper operation.
Summary of Contents for ATLV 4300
Page 1: ...330495 Rev 03 5 02 Service Manual ATLVt t t t 4300 330495 ...
Page 4: ...GENERAL INFORMATION 1 2 ATLV 4300 330495 8 94 ...
Page 11: ...GENERAL INFORMATION 1 9 ATLV 4300 330495 12 01 ...
Page 20: ...GENERAL INFORMATION 1 18 ATLV 4300 330495 12 01 ...
Page 22: ...CHASSIS 2 2 ATLV 4300 330495 10 98 ...
Page 48: ...CHASSIS 2 28 ATLV 4300 330495 12 01 ...
Page 50: ...VACUUMING 3 2 ATLV 4300 330495 10 98 ...
Page 68: ...VACUUMING 3 20 ATLV 4300 330495 10 98 ...
Page 70: ...ELECTRICAL 4 2 ATLV 4300 330495 10 98 ...
Page 85: ...ELECTRICAL 4 17 ATLV 4300 330495 6 01 ELECTRICAL SCHEMATIC 352281 ...
Page 86: ...ELECTRICAL ATLV 4300 330495 6 01 4 18 ELECTRICAL SCHEMATIC 352281 ...
Page 87: ...ELECTRICAL 4 19 ATLV 4300 330495 6 01 WIRE HARNESS ...
Page 88: ...ELECTRICAL ATLV 4300 330495 6 01 4 20 WIRE HARNESS ...
Page 89: ...ELECTRICAL 4 21 ATLV 4300 330495 6 01 WIRE HARNESS ...
Page 90: ...ELECTRICAL ATLV 4300 330495 6 01 4 22 WIRE HARNESS ...
Page 91: ...ELECTRICAL 4 23 ATLV 4300 330495 6 01 WIRE HARNESS ...
Page 92: ...ELECTRICAL ATLV 4300 330495 6 01 4 24 WIRE HARNESS ...
Page 98: ...ELECTRICAL 4 30 ATLV 4300 330495 10 98 ...
Page 100: ...HYDRAULICS 5 2 ATLV 4300 330495 10 98 ...
Page 119: ...HYDRAULICS 5 21 ATLV 4300 330495 10 98 STEERING CYLINDER BREAKDOWN ...
Page 122: ...HYDRAULICS 5 24 ATLV 4300 330495 10 98 ...
Page 123: ...HYDRAULICS 5 25 ATLV 4300 330495 6 01 HYDRAULIC SCHEMATIC ...
Page 124: ...HYDRAULICS ATLV 4300 330495 6 01 5 26 HYDRAULIC HOSE GROUP ...
Page 130: ...HYDRAULICS 5 32 ATLV 4300 330495 10 98 ...
Page 141: ...11 2000 Series Disc Valve Motors Notes ...
Page 161: ...19 Model 70160 Notes ...
Page 169: ...7 Power Steering 2 Series Steering Control Units ...