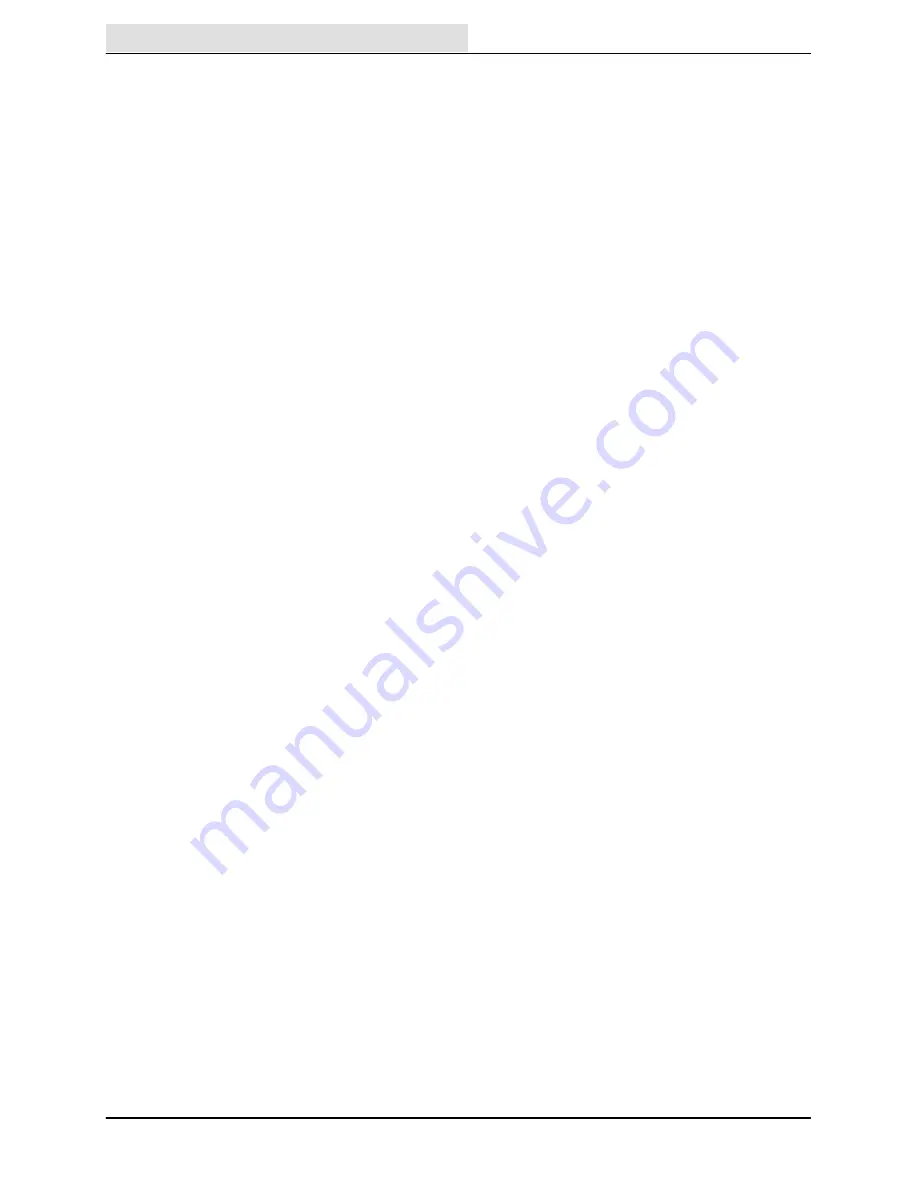
ELECTRICAL
4-2
7400 MM428 (9--01)
Page
HYDRAULIC (HIGH) PRESSURE
INDICATOR LIGHT WILL NOT TURN
ON OR OFF (SCHEMATIC)
4-65
. .
HYDRAULIC (HIGH) PRESSURE
INDICATOR LIGHT WILL NOT TURN
ON (FLOW CHART)
4-66
. . . . . . . .
HYDRAULIC (HIGH) PRESSURE
INDICATOR LIGHT WILL NOT TURN
OFF (FLOW CHART)
4-66
. . . . . . .
ENGINE OIL PRESSURE WARNING
LIGHT WILL NOT TURN ON OR
OFF (SCHEMATIC)
4-67
. . . . . . . . .
ENGINE OIL PRESSURE WARNING
LIGHT WILL NOT TURN ON
(FLOW CHART)
4-68
. . . . . . . . . . . . .
ENGINE OIL PRESSURE WARNING
LIGHT WILL NOT TURN OFF
(FLOW CHART)
4-68
. . . . . . . . . . . . .
RECOVERY TANK FULL LIGHT WILL
NOT TURN ON OR OFF
(SCHEMATIC)
4-69
. . . . . . . . . . . . . . .
RECOVERY TANK FULL LIGHT WILL
NOT TURN ON (FLOW CHART)
4-70
.
RECOVERY TANK FULL LIGHT WILL
NOT TURN OFF (FLOW CHART) 4-70
FUEL GAUGE (GAS AND DIESEL)
(SCHEMATIC)
4-71
. . . . . . . . . . . . . . . . .
FUEL GAUGE (GAS AND DIESEL)
(FLOW CHART)
4-72
. . . . . . . . . . . . . . . .
FUEL GAUGE (LPG) (SCHEMATIC) 4-73
.
FUEL GAUGE (LPG) (FLOW CHART) 4-74
Summary of Contents for 7400
Page 1: ...7400 Service Manual MM428 Rev 04 3 02 ...
Page 4: ...GENERAL INFORMATION 1 2 7400 MM428 6 01 ...
Page 24: ...CHASSIS 2 2 7400 MM428 12 98 ...
Page 38: ...SCRUBBING 7400 MM428 12 98 3 2 ...
Page 68: ...SCRUBBING 3 32 7400 MM428 12 98 ...
Page 80: ...ELECTRICAL 4 12 7400 MM428 6 01 SHEET 2 GAS LPG ELECTRICAL SCHEMATIC ...
Page 82: ...ELECTRICAL 4 14 7400 MM428 6 01 SHEET 4 DIESEL ELECTRICAL SCHEMATIC ...
Page 86: ...ELECTRICAL 4 18 7400 MM428 6 01 SHEET 8 GAS LPG WIRE HARNESS GROUP OPTIONS ...
Page 144: ...HYDRAULICS 5 2 7400 MM428 12 98 ...
Page 177: ...HYDRAULICS 5 35 7400 MM428 6 01 A B C D E F G H I HYDRAULIC SCHEMATIC ...
Page 178: ...HYDRAULICS 5 36 7400 MM428 6 01 S 14 A B C D G H I F E HYDRAULIC SCHEMATIC ...
Page 185: ...HYDRAULICS 5 43 7400 MM428 12 98 ...
Page 189: ...HYDRAULICS 5 47 7400 MM428 12 98 ...
Page 195: ...HYDRAULICS 5 53 7400 MM428 12 98 ...
Page 203: ...HYDRAULICS 5 61 7400 MM428 12 98 ...
Page 207: ...HYDRAULICS 5 65 7400 MM428 12 98 ...
Page 234: ...18 18 Model 70142 70144 and 70145 Notes ...
Page 235: ...19 19 Model 70142 70144 and 70145 Notes ...
Page 249: ......
Page 250: ......
Page 251: ......
Page 252: ......
Page 253: ......
Page 254: ......
Page 255: ......
Page 256: ......
Page 263: ...7 Power Steering 2 Series Steering Control Units ...
Page 266: ...ENGINE GAS LP 6 2 7400 MM428 12 98 ...