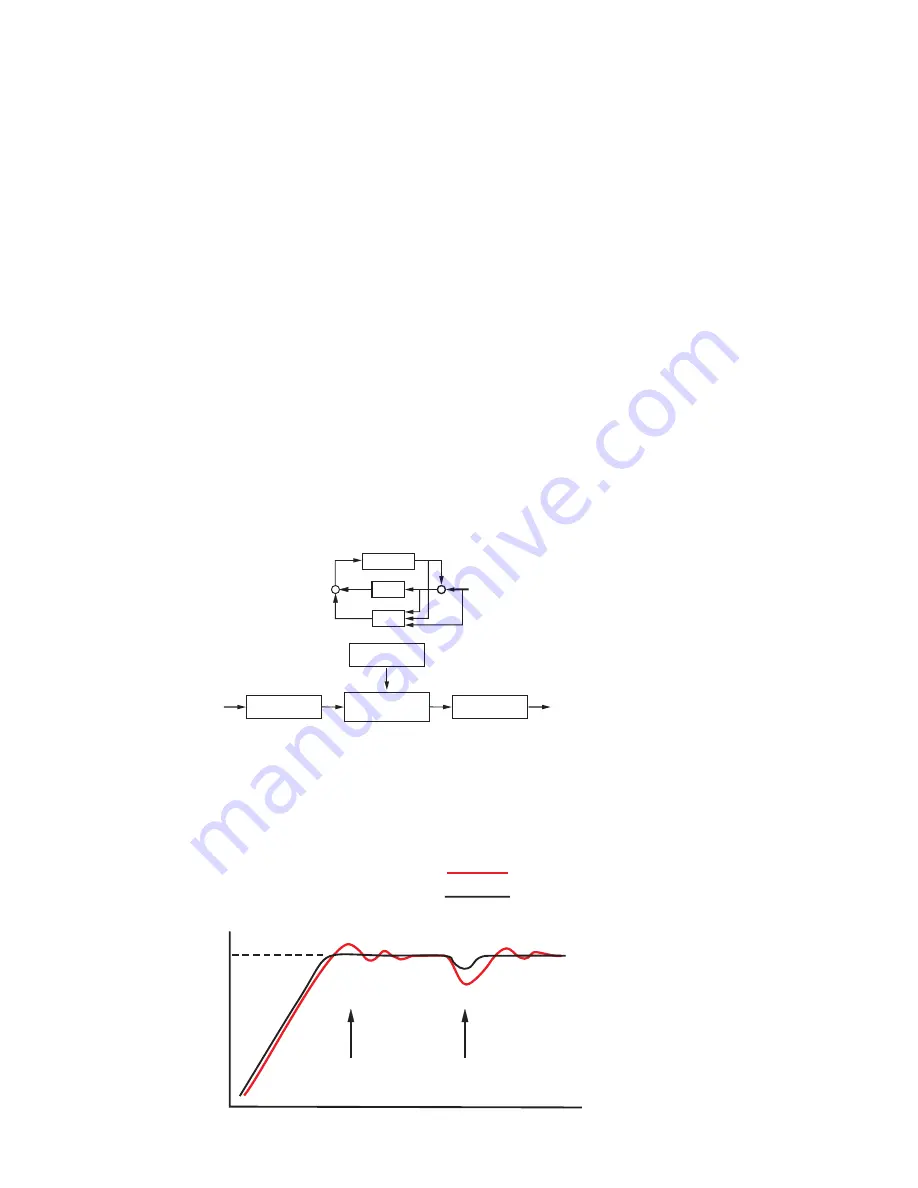
1. Introduction
TEC-9200 Fuzzy Logic plus PID microprocessor-based controller incorporates a bright, easy to read, 4-digit LED display which indicates
the process value. Fuzzy Logic technology enables a process to reach a predetermined set point in the shortest time, with the minimum
of overshoot during power-up or external load disturbance. The units are housed in a 1/16 DIN case, measuring 48mm x 48mm with
75mm behind-panel depth. The units feature three touch keys to select the various control and input parameters. Using a unique function,
you can determine which parameters are accessible by the user. You can also put up to five parameters at the front of the user menu by
using SEL1 to SEL5 found in the setup menu. These are particularly useful to OEM's as it is easy to limit access and configure the menu
to suit the specific application.
TEC-9200 is powered by 20–32 or 90–264VAC supply, incorporating a 3 amp control relay output and dual 3 amp alarm relay outputs as
standard with a second alarm that can be configured in the second output for cooling purposes or as a dwell timer. Alternative output options
include SSR drive, triac, 4–20mA and 0–10 volts. TEC-9200 is fully programmable for PT100, thermocouple types J, K, T, E, B, R, S, N,
0–20mA, 4–20mA, and voltage signal input, with no need to modify the unit.
Digital communications format RS-485 or 4–20mA retransmission are available as an additional option. These options allow the TEC-
9200 to be integrated with supervisory control systems and software, or alternatively to drive remote displays, chart recorders, or data
loggers.
For nearly a hundred years, PID control has been used and has proven to be an efficient controlling method by many industries, yet
PID has difficulty dealing with some sophisticated systems such as second and higher order systems, long time-lag systems, during set
point changes and/or load disturbances, etc. The PID principle is based on a mathematical model which is obtained by tuning the
process. Unfortunately, many systems are too complex to describe precisely in numerical terms. In addition, these systems may vary
from time to time. In order to overcome the imperfections of PID control, Fuzzy Technology was introduced. What is Fuzzy Control? It
works like a good driver. Under different speeds and circumstances, he can control a car well based on previous experience, and does
not require knowledge of the kinetic theory of motion. Fuzzy Logic is a linguistic control which is different from numerical PID control. It
controls the system by experience and does not need to simulate the system precisely as a PID controller would.
The function of Fuzzy Logic is to adjust PID parameters internally in order to make manipulation of output value MV more flexible and
adaptive to various processes.
The Fuzzy Rule may work like this:
If the temperature difference is large, and the temperature rate is large, then
∆
MV is large.
If the temperature difference is large, and the temperature rate is small, then
∆
MV is small.
PID+Fuzzy Control has been proven to be an efficient method to improve control stability as shown by the comparison curves below:
3
PROCESS
PID
FUZZY
MV
PV
_
+
SV
+
+
Fuzzy Rule
Fuzzy Inference
Engine
Defuzzifier
Fuzzifier
Digital
information
Language
information
Digital
information
Figure 1.1
Fuzzy PID System Block
Figure 1.1
Fuzzy PID System Block
PID + FUZZY CONTROL
Warm Up
Load Disturbance
PID control with properly tuned
PID + Fuzzy control
Set point
Temperature
Time
Figure 1.2 Fuzzy PID
Enhances Control
Stability
Figure 1.2 Fuzzy PID
Enhances Control
Stability