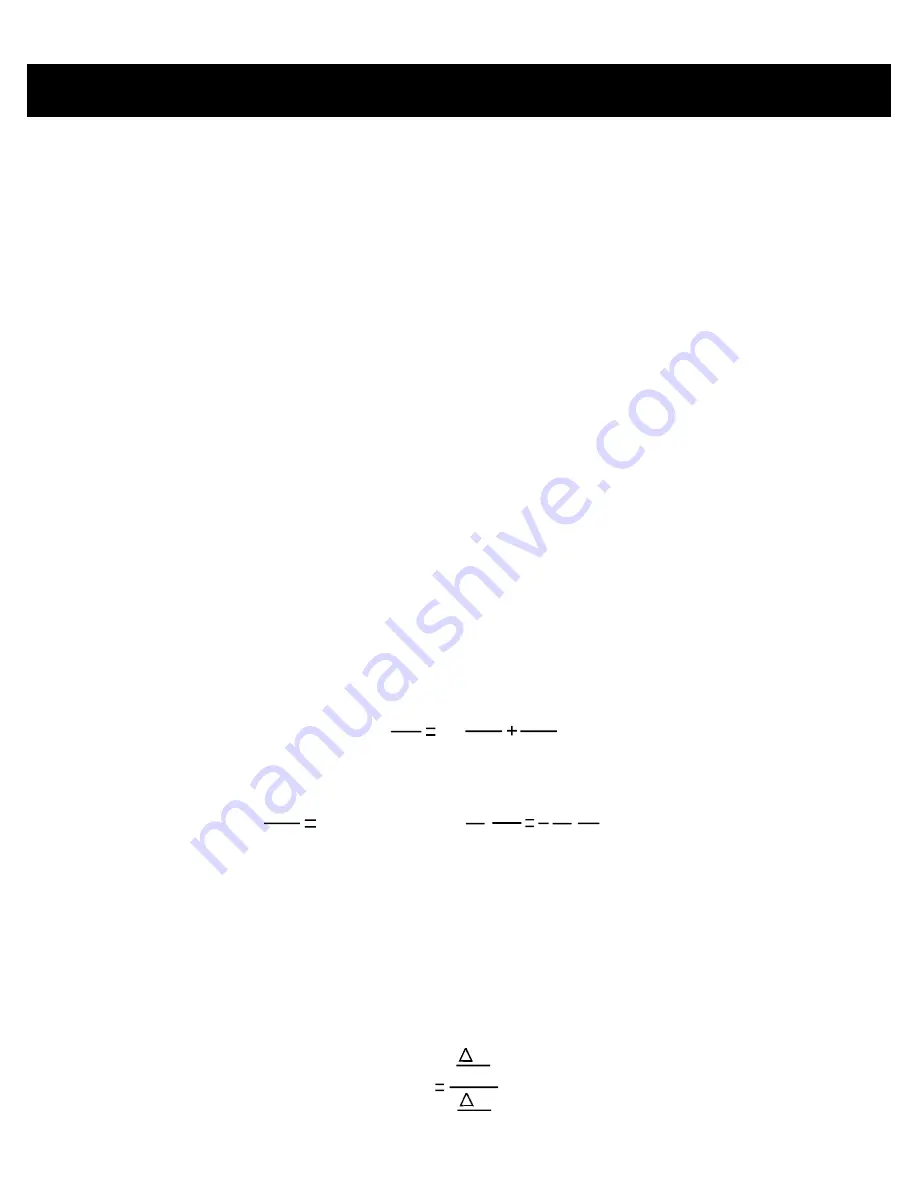
page 19
Theory of Operation
SECTION 5
The Model 2002 transducer is comprised of two very different sensors which provide a span of
measurement extending from 1000 Torr down to less than 1x10
-4
Torr. The piezoresistive device is
a direct force sensor which provides pressure indication from 1000 Torr down to less than 1 Torr.
The thin film Pirani device is a thermal conductivity sensor that provides pressure indication from
100 Torr down to less than 1x10
-4
Torr. The two decade overlap in measurement range is conve-
nient for smooth transition either descending or ascending in pressure. Both sensors are small
micromachined die that are bonded to a Au coated Al
2
O
3
preform (stress isolation) which in turn is
bonded to a TO-8 header. The header is resistance welded into a 316 stainless steel envelope as
shown in Figure 5.1.
5.1 Piezoresistive Sensor
Figure 5.2 shows a typical schematic of a B implanted Wheatstone bridge network in a Si dia-
phragm inverted box type geometry. The inside of the box is evacuated during anodic bonding to
a Pyrex substrate. The membrane has maximum deflection at atmosphere (or higher pressure) and
the membrane resistances change value as the differential pressure is decreased during pumpdown.
The resulting differential output is
V
o
= SPV+V
1
where
S is the sensitivity
P is the pressure
V is the applied bridge voltage
V
1
is the no load output voltage
Since the sensitivity changes so dramatically with temperature, some correction is required for
compensation. The change in output voltage
To insure temperature invariance,
G9
G7 3
6G9
G7
9G6
G7
which requires for any change in sensitivity to be countered by an equal but opposite change in
applied voltage. The temperature compensation is a network of temperature dependent resistive
components and fixed temperature compensation current source compensation, TCR = -TCS.
Sensitivity of the sensor is proportional to the sensor factor (K), the strain gauge positioning of the
diaphragm (
f
) and the diaphragm geometery (
q
) thus S
µ
K
fq
. Once the defining geometry of the
resistive film and piezo membrane have been established, the sensor factor is dependent on the
crystal orientation of the membrane material, the doping level and diffusion parameters, and the
strain gauge geometry. The sensor factor is essentially the change in resistance for a change in
strain or,
.
5
/
5
/
G9
G7
G9
G7
9
6
G6
G7
therefore
Summary of Contents for HASTINGS 2002
Page 1: ...page 1 MODEL 2002 VACUUM GAUGE HASTINGS INSTRUCTION MANUAL ...
Page 17: ...page 17 Figure 4 2 MODEL 2002 Analog Output VDC volts vs Pressure Torr ...
Page 18: ...page 18 ...
Page 26: ...page 26 ...
Page 38: ...page 38 ...
Page 39: ...page 39 Diagrams and Drawings SECTION 10 ...
Page 44: ...page 44 ...
Page 45: ...page 45 ...
Page 46: ...page 46 ...
Page 47: ...page 47 ...
Page 48: ...page 48 ...
Page 49: ...page 49 ...