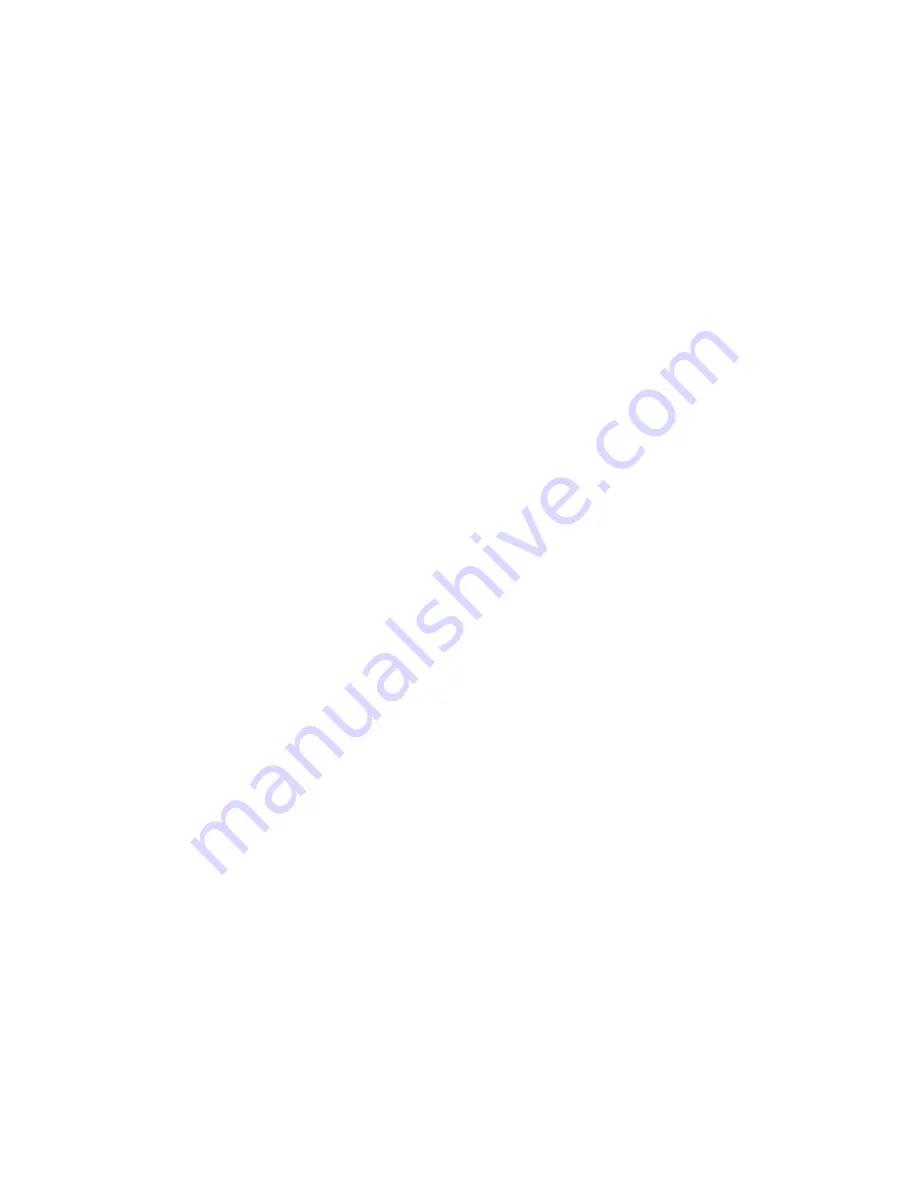
TM 11-6625-3145-14
Maintenance: Troubleshooting-318/338 Service
The words, WA, WB, and WC are set to 01
hex
, 02
hex
and 03
hex
respectively. Then full trigger sequence, 5*WA FLW’D
BY:WB RESET ON:WC is selected with 16 clocks of delay to stop after the trigger recognition.
The data AAAXBCAAXAAAXABXABCXABCXABCXABC is supplied to the WR on the A01 and the A02 boards and to the
ACQ Memories on the A04 ACQ MEMORY board. SYSCLK is generated by the MPU by writing at I/O address 4A
hex
,
which is into the Time Base U140 on the A04.
The operation of the Trigger Sequencer is observed by the MPU by reading the interrupt and the ACQ status. The MPU
checks these conditions on every clock pulse, and if there are any unexpected events the MPU displays an error message.
After the end of the acquisition (all flags are detected at certain clocks), the MPU reads the data from the ACQ Memories
on the A04 board, and compares them with the word sequence applied. An error message is displayed if there are
differences.
338S1 SERIAL ANALYSIS/RS232C/NVM
14.
BATTERY TEST
Program: TSTBTT
Function:
Power on - TSTBTT checks the battery voltage to see if it is more or less than 2.2 Volts.
Troubleshooting - None
Description - Detected battery voltage status is shown in the option status register at bit 07. TSTBTT reads this bit from
I/O address 80. (Refer to option I/O function list)
Battery voltage is detected by Q170, and battery status is applied to bit #7 of the status register by U32.
U30 decodes option I/O addresses.
15.
NON-VOLATILE MEMORY TEST
Program: TSTNV1 (power on), TSTNV2 (Troubleshooting)
Function:
Power on - The NVM has a check-sum word that is used for checking non-volatile memory data. The TSTNV1 program
calculates the check sum by reading NVM data and comparing it with the NVM check sum.
Troubleshooting - The TSTNV2 diagnostic program includes twelve test programs. For all of these tests, the method is
read data after write. (Refer to the failure code list for check data format.)
All NVM data is cleared after the diagnostic has run.
7-122
Summary of Contents for 318
Page 119: ...318 VERIFICATION AND ADJUSTMENT PROCEDURES ...
Page 182: ...338 VERIFICATION AND ADJUSTMENT PROCEDURES ...
Page 253: ...318 ___________________ TROUBLESHOOTING TREES ...
Page 344: ...338 TROUBLESHOOTING TREES ...
Page 517: ...TM 11 6625 3145 14 318 338 4434 923 318 Block Diagram ...
Page 518: ...TM 11 6625 3145 14 318 338 4434 924 338 Block Diagram ...
Page 519: ...TM 11 6625 3145 14 318 338 4434 925 318 Acquisition Module Wiring Diagram ...
Page 520: ...TM 11 6625 3145 14 318 338 4434 926 318 338 Mainframe Wiring Diagram ...
Page 521: ...TM 11 6625 3145 14 318 338 4434 926 338 Acquisition Module Wiring Diagram ...
Page 522: ...TM 11 6625 3145 14 318 338 4434 928 Figure 9 1 318 A01 Input A Board Component Locations ...
Page 526: ...TM 11 6625 3145 14 ...
Page 528: ...TM 11 6625 3145 14 Figure 9 3 318 338 A03 ACQ Control Board Component Locations ...
Page 532: ...TM 11 6625 3145 14 ...
Page 536: ...TM 11 6625 3145 14 ...
Page 538: ...TM 11 6625 3145 14 ...
Page 539: ...TM 11 6625 3145 14 ...
Page 540: ...TM 11 6625 3145 14 ...
Page 541: ...TM 11 6625 3145 14 ...
Page 542: ...TM 11 6625 3145 14 Figure 9 8 318 338 A10 CRT Board Component Locations ...
Page 544: ...TM 11 6625 3145 14 Figure 9 9 318 338 A11 Inverter Board component Locations ...
Page 546: ...TM 11 6625 3145 14 Figure 9 10 318 338 A12 Regulator Board Component Locations ...
Page 551: ...TM 11 6625 3145 14 Figure 9 12 338 A01 Input A Board Component Locations ...
Page 553: ...TM 11 6625 3145 14 318 338 SERVICE ...
Page 554: ......
Page 555: ...PIN 058584 ...