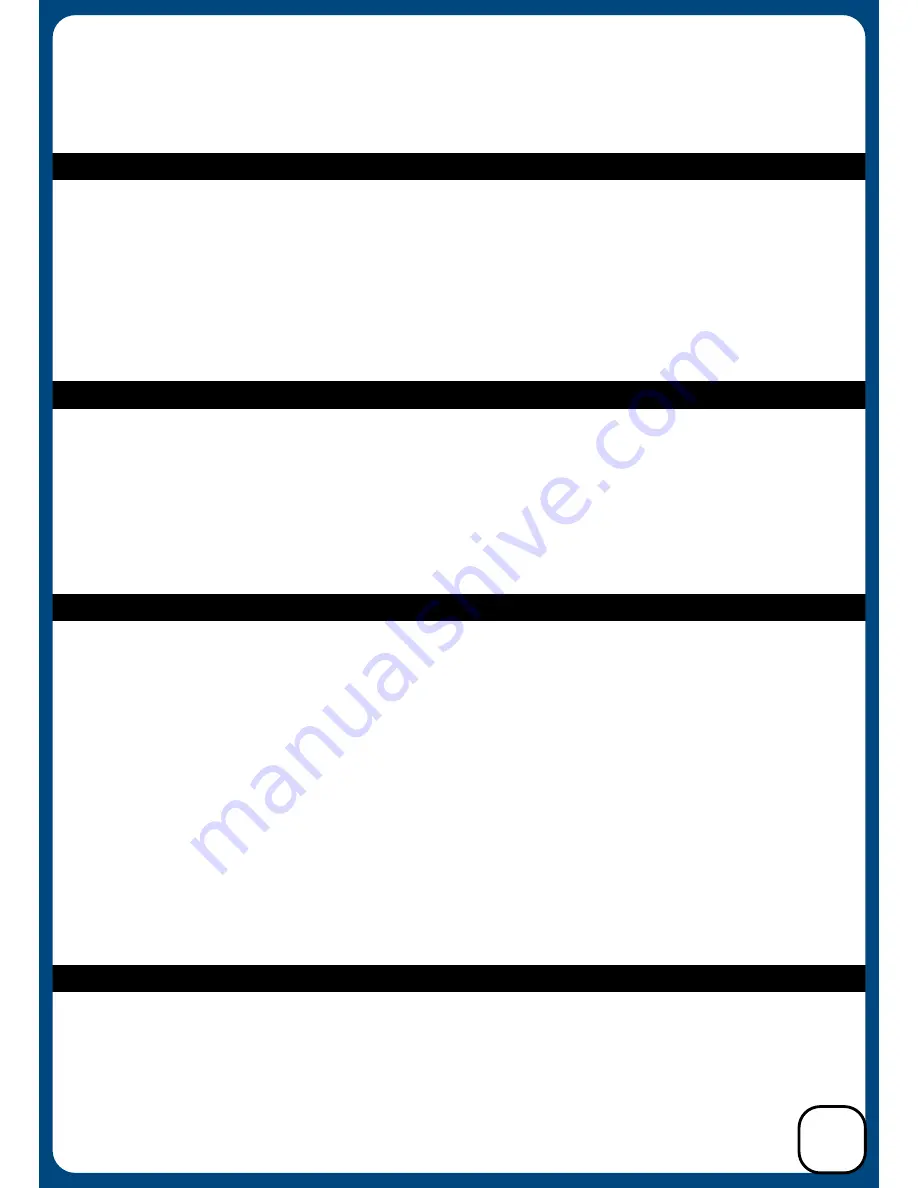
Bearing Maintenance:
Performing regular maintenance will greatly improve your on track consistency and also extend the life of your vehicle.
Going through critical areas of the vehicle regularly will also allow you to find possible issues before they become a
problem that may cost you a race. Follow the guidelines below for maximum performance.
Bearings should always be smooth and free in order to preform their function. We recommend inspecting and cleaning
each bearing on a regular basis. It will be necessary to break down parts of the vehicle in order to inspect them properly.
The procedures below should be done every couple of weeks or prior to an important race.
1. Inspect the outer seals for any visible damage and check the rolling resistance of each bearing.
2. If any bearing does not spin freely, then take the following steps to clean them.
3. Spray the bearing with motor spray and spin it again to remove any debris trapped inside. Repeat if necessary. If
the bearing does not start to spin freely after cleaning, then they may need to be replaced.
4. Allow the clean bearing to dry or blow into the bearing with compressed air to speed up the drying process.
5. Oil each bearing with a proper bearing lubricant. One or two drops is enough.
Shock Maintenance:
When comparing the left and right shocks of the front end, they should feel identical. Same goes for the rears.
The procedures below should be done every race day to make sure they are leak free and operating correctly.
1. After removing the shocks from the vehicle, remove the springs and inspect each shock for visible leaks (build up of
debris at the bottom of the shock shaft or visible oil).
2. If the shock binds when pushing the shaft through its stroke, then the shaft may be bent and will need to be replaced.
3. If the shocks from left to right do not feel consistent when compared to each other, or have built up too much air
inside (feel empty when pushing the shaft through its stroke), then you will need to rebuild them following the steps
outlined on page 19 of this manual.
Properly maintained differentials are essential for a smooth operating vehicle. Check all three diffs regularly to make
sure they are filled and operating as designed.
1. Remove each diff and verify the differential action is happening and is smooth. If there is any notchy feel to them,
follow the steps below to rebuild them.
2. Open the diff and pour out the oil. Remove the gears and pins to release the outdrives, then remove the
seals. Inspect everything to make sure there are no damaged parts. If the seals are old or show any signs
of degradation, replace them immediately. Re-lubricate the seals and outdrives, then rebuild the diff
following the steps on page 3 and 4.
Hinge Point & Drive Line Maintenance:
Differential Maintenance:
Checking the hinge points while the shocks are removed from the vehicle is the best time to inspect these parts. The
other items to inspect are the camber links, steering links and drive shafts. Follow the steps below every couple of
weeks in order to keep the vehicle preforming at the maximum level.
1. With the shocks off the vehicle, check the movement of the arms, hubs, and spindle carriers. They should move
freely. If there is a bind, then the inner or outer hinge pin may be bent and would need to be replaced. The arms
should not have any play when twisted or moved in any direction against the hinge points. If there is excessive
slop present, then the arms or hubs may be worn and will need to be replaced.
2. Remove the camber links, steering links and servo link from the vehicle. Check the movement of the spindles to see
if they turn freely. If they don’t, then check the kingpin shoulder screws to see if they are tightened down too far.
Also, check for slop. If there is excessive slop present, then the spindle carriers may need to be replaced.
3. Check the steering rack to make sure it moves freely. If it binds, then the screws holding the Ackermann or the
steering posts could be too tight. If they still bind, then check the bearings and follow the steps above to clean them.
4. After re-installing the camber links, steering links and servo link, check the movement of the rod ends on the ball
studs. If they have excessive slop or are binding, then they may need to be replaced.
5. Check the drive shafts by rotating them. Look for any wobbles. If they are bent, replace them immediately.
6. With the drive shafts removed, check for slop in the CV area. If it is present, then reposition the CV pin to another
fresh hole, re-lubricate and install back into the vehicle.
Maintenance:
28
Summary of Contents for ET410
Page 1: ......
Page 31: ......
Page 32: ...Tekno RC 10755 Scripps Poway Pkwy 598 San Diego CA 92131 USA...