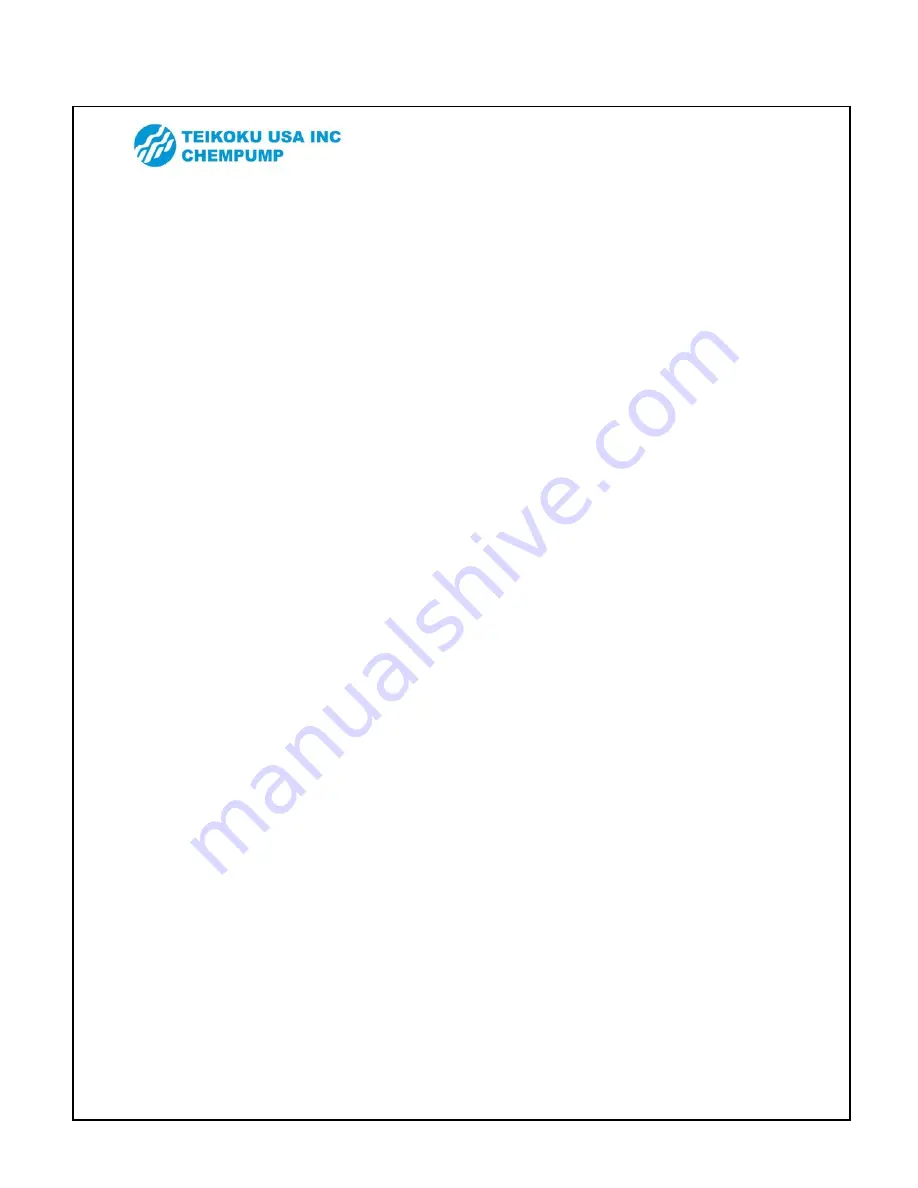
Teikoku USA | Chempump
Instruction Manual NC-Series 0620
35
DECONTAMINATION CERTIFICATION
AND FLUSHING PROCEDURE
Page
2
of
3
REV.
4-
17-20
FLUSHING PROCEDURES FOR TEIKOKU
USA PRODUCTS
THE FOLLOWING FLUSHING PROCEDURES ARE REQUIRED TO ALLOW FOR MAXIMUM
REMOVAL OF PROCESS FLUIDS.
A. COMPLETE PUMPS AND PARTS
Pumps and parts that are returned for service are to be thoroughly decontaminated and free of
process and flushing fluids.
Some pumps handle a fluid that may solidify and cannot be removed by flushing the pump.
These pumps should be fully disassembled for removal of all traces of fluids to avoid solidification
of the fluids in the pump.
SUGGETIONS FOR DECONTAMINATION
1. With the suction flange down, introduce an appropriate neutralizing fluid through the discharge
flange. Flush the pump in this manner for a sufficient time to allow for the removal of all process
fluid.
2. Introduce an appropriate neutralizing fluid to the rear of the pump for a sufficient time to allow for
the removal of all process fluid. The method of fluid insertion depends on the pump design.
Access may be through a circulation line, vent, drain or flush connection. In some cases, the rear
bearing housing needs to be removed to thoroughly flush the pump internals.
Remove as much of the neutralizing fluid as possible using compressed air or inert gas.
For pumps with shaft sleeves, complete disassembly will be required to remove trapped fluid.
Flush all auxiliary tubing, piping and equipment such as heat exchangers.
For any questions on decontamination, contact your Teikoku service representative.
See sections "B" through "D" for stator assembly decontamination requirements where a liner
breach is suspected. Pumps with the TRG bearing wear monitor will have a wear meter visible
on the pump terminal box.
B. G series without TRG and J-series stator assembly (if equipped with a relief valve).
If a stator liner rupture is suspected, follow this section to flush the stator cavity.
Caution:
if this
step is followed, the motor must be rewound.
Remove the relief valve. Insert a screwdriver into the relief valve adapter and pry the Lisk filter to
one side. Remove the connection box from the lead nipple and chip away the potting compound
from the lead nipple.
Position the stator assembly with the lead nipple down and introduce an appropriate neutralizing
fluid to the relief valve adapter. The fluid will exit through the lead nipple. Flush the stator cavity in
this manner for a sufficient time to allow for the removal of all process fluid and stator oil.
Remove as much of the neutralizing fluid as possible by purging the stator cavity with
compressed air or inert gas for 3 - 5 minutes.
If the connection box is to be returned, assure that all components have been decontaminated.
Decontamination Form pg. 2