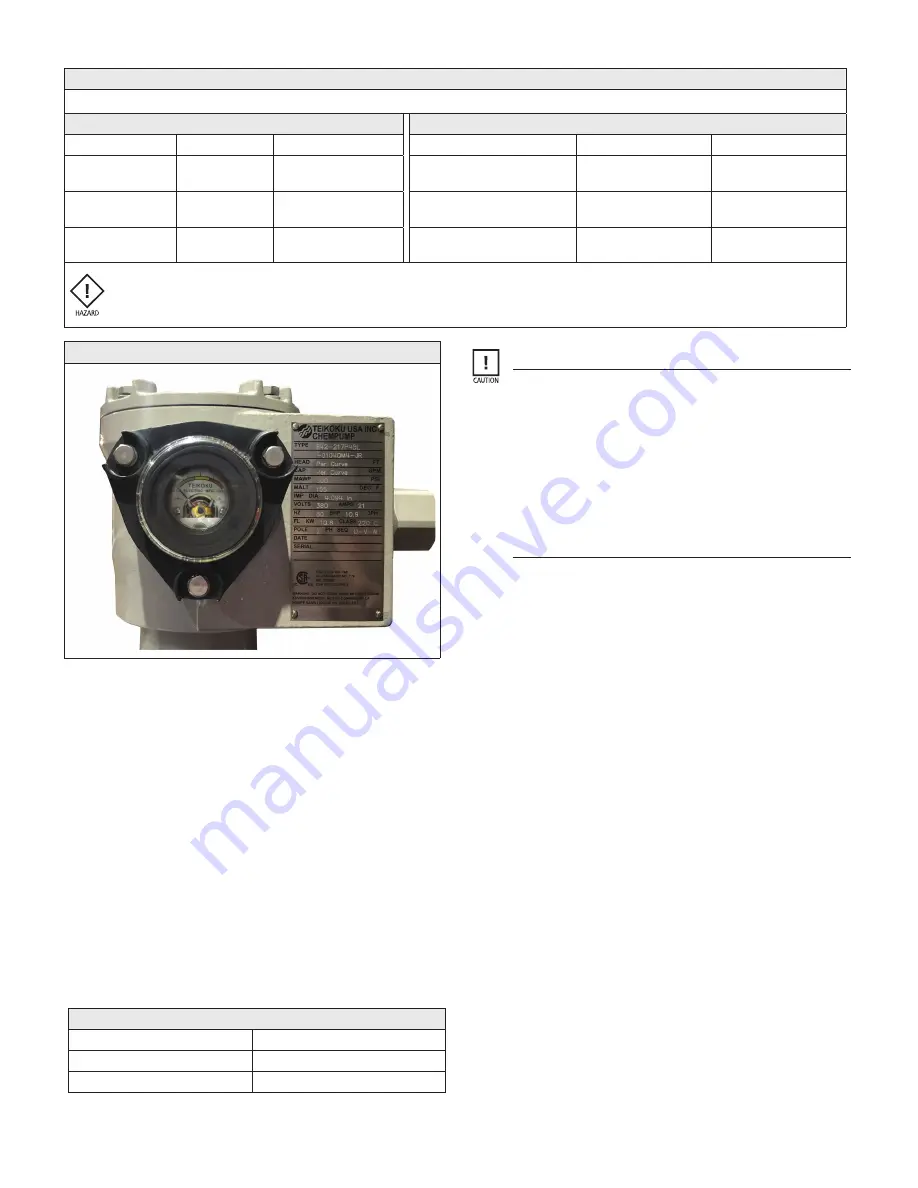
Teikoku USA | Chempump
Instruction Manual G-Series
11
Figure 2-2. Teikoku TRG Bearing Wear Monitor
Table 2-1. Conditions Indicated on the TRG Meter
The TRG meter has a colored scale which is divided into three zones: Green (0 to 0.5), Yellow (0.5 to 0.75), Red (0.75 to 1)
AT TRIAL OPERATION
DURING OPERATION
Indication
Condition
Solution
Indication
Diagnosis
User Actions
Full scale
incorrect wiring
change power cable
connection
Green
Good
No action
Yellow to Red
phase failure
check connection of
cables
Yellow or scale increase of
> 0.3 from initial indication
Bearings worn to
caution level
Plan routine
maintenance
Green
normal
connection is correct
Red or scale increased of
> 0.5 from initial indication
Immediate
maintenance required
Shutdown immediately
and replace worn parts
Hazard!
Do not operate if TRG meter condition is RED.
using the TRG meter, use the color change (Green, Yellow, Red)
as a reference. If the increase of TRG readings is 0.3 or more, stop
the pump and check bearings.
The Teikoku Rotary Guardian (TRG) signal is affected by motor
load. Changes in operating frequency or hydraulic load may in-
crease or decrease signal.
Keeping records of the TRG meter reading in conjunction with
motor amp readings will provide a good indication of when the
pump will require maintenance.
2.3.2 Thermal Cutout
Unless otherwise specified, all G-Series pumps are fitted with
thermal cutouts. The cutout is a heat-sensitive bimetallic switch,
mounted in intimate contact with the stator windings. It is to be
wired in series with the holding coil in the starter box. Refer to
Table 2-2
for TCO maximum holding coil currents.
Table 2-2. TCO Maximum Coil Currents
115 Volt
3.1 Amps
230 Volt
1.6 Amps
460 Volt
0.8 Amps
Caution!
The thermal cutout switch does not provide protection
against fast heat buildup resulting from locked rotor con-
ditions, single phasing, or heavy overloads. This protection
must be provided for by the current overload relay heaters
in the magnetic starter. The rating of the heaters should
be high enough to avoid nuisance cut outs under running
loads, but must not be oversized. Refer to
Table 2-3
for
starting and running electrical characteristics. It is recom-
mended that “quick trip”, class 10 or less, type heaters
be used.
2.3.3 Starting Equipment
Motor starters (normally not supplied with G-Series pumps)
should be sized to handle the load required per the National Elec-
trical Code (NEC). Start KVA, Full Load KW, Full Load amps and
Full Load KVA data are listed in
Table 2-3
.
Thermal overload protective devices in the starters should be sized
for the amperage shown on the product nameplate. DO NOT size
the thermal overload protective device in excess of 10% of full
load amp rating. In order to provide complete protection for G-
Series motors under all conditions, it is recommended that “quick
trip” (Class 10) type thermal overload protective devices be used
in the starters where available. Standard type thermal overload
protective devices can be used if these “quick trip” type thermal
overload protective devices are not available. Standard thermal
overload protective devices provide adequate protection for G-
Series motors under starting or normal running conditions, but
require a greater length of time than “quick trip” type thermal
overload protective devices to cut out. This may not protect the
meter if the motor is subject to locked rotor or overload condi-
tions. Also, see
Tables 2-3, 2-4, 2-5,
or
2-6
for additional electrical
wiring data for the most common G-Series motor sizes to assist in
the electrical installation of the unit.
2.3.4 Variable Frequency Drive (VFD) Power Supply
G-Series pumps can be operated with a VFD power supply. The
VFD should be a Pulse Width Modulated Drive selected for the
appropriate voltage class of the motor, i.e. 400V class for 460V
motors, and suitable to handle the full load current of the motor.
The VFD should always be sized based on full load nameplate