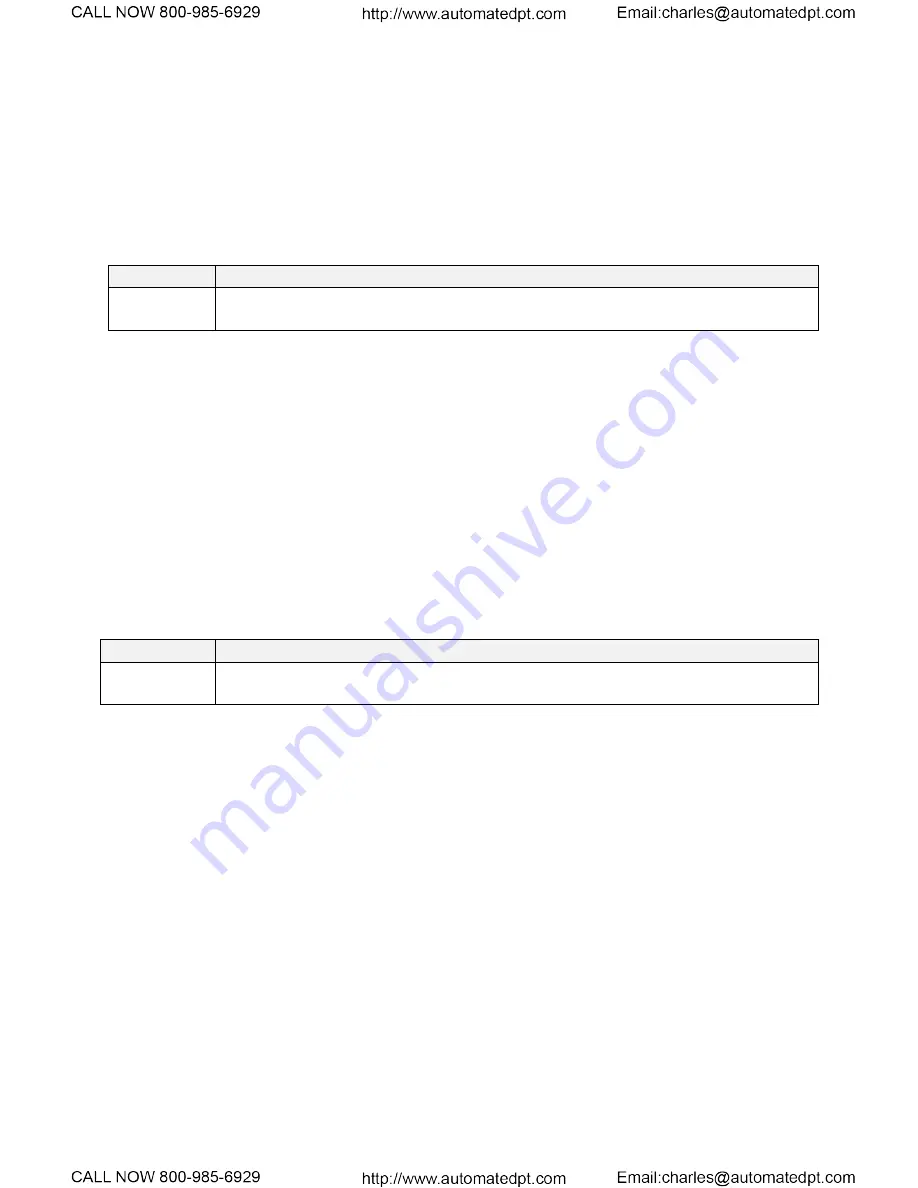
A1-7
■
08-05 Motor Overload Protection Selection
The inverter has an electronic overload protection function (OL1) based on time, output current, and output
frequency, which protects the motor from overheating. The electronic thermal overload function is
UL-recognized, so it does not require an external thermal overload relay for single motor operation.
This parameter selects the motor overload curve used according to the type of motor applied.
08-05
Selection for motor overload protection (OL1)
Range
0:
Disabled
1:
Enabled
Sets the motor overload protection function in 08-05 according to the applicable motor.
08-05 = 0:
Disables the motor overload protection function when two or more motors are connected to a
single inverter. Use an alternative method to provide separate overload protection for each motor such as
connecting a thermal overload relay to 1he power line of each motor.
08-05 = 1:
The motor overload protection function should be set to hot start protection characteristic curve
when the power supply is turned on and off frequently, because the thermal values are reset each time
when the power is turned off.
■
08-06 Motor Overload Operation Selection
08-06
Start-up mode of overload protection operation (OL1)
Range
0:
Coast-to-Stop After Overload Protection is Activated
1:
Drive Will Not Trip when Overload Protection is Activated (OL1)
08-06=0:
When the inverter detects a motor overload the inverter output is turned off and the OL1 fault
message will flash on the keypad. Press RESET button on the keypad or activate the reset function
through the multi-function inputs to reset the OL1 fault.
08-06=1:
When the inverter detects a motor overload the inverter will continue running and the OL1 alarm
message will flash on the keypad until the motor current falls within the normal operating range.