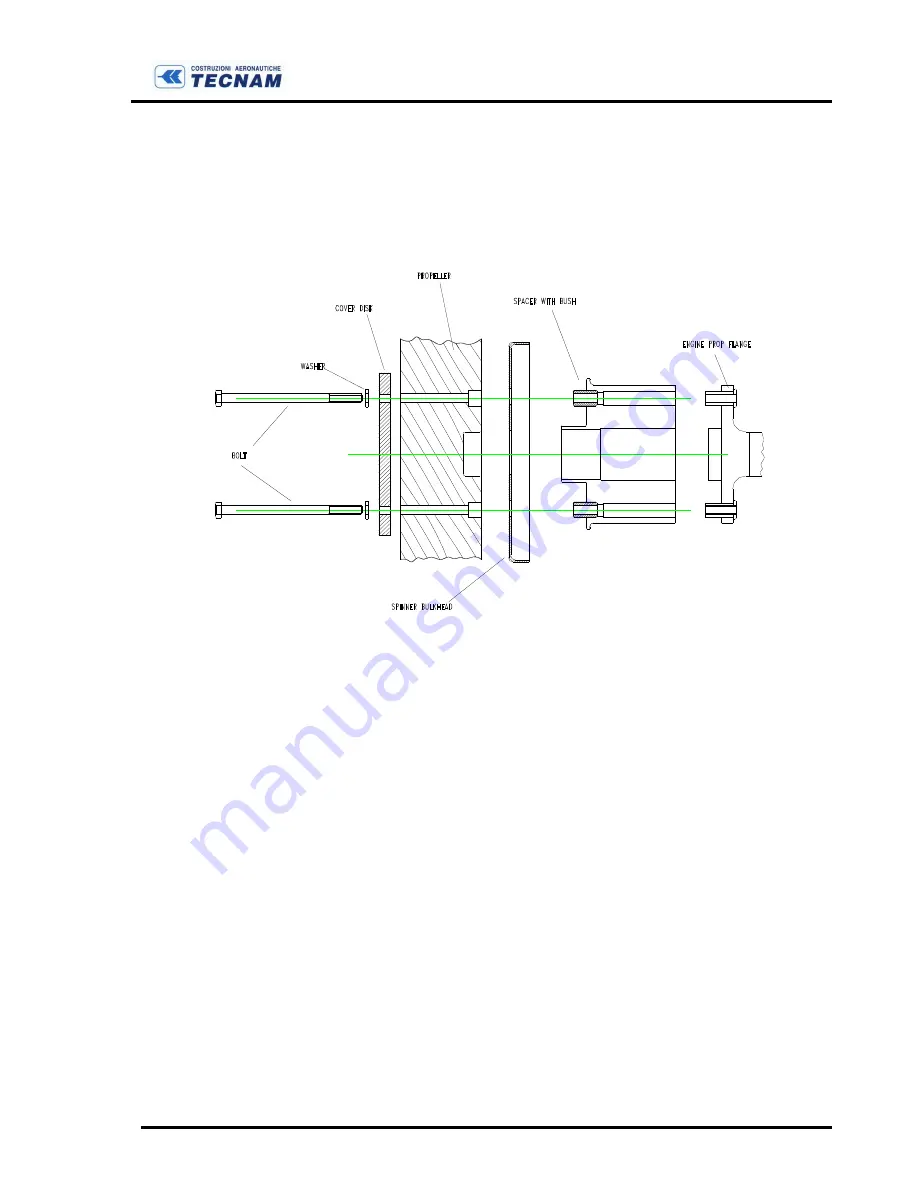
2
st
Edition, April 22
th
, 2008
P2002 Sierra
M A I N T E N A N C E M A N U A L
SECTION D
POWERPLANT
pag.
D-5
After correct installation of propeller and before takeoff, let the engine
run for a few minutes and, after turning it off, carry out further inspection
(tightness, overall state, etc.).
F
IGURE
D-3
P
ROPELLER INSTALLATION
3.3 PERIODIC INSPECTION
Refer to specific subsection in Periodic Inspection Schedule of Section B.
For further information refer to “Owner’Manual” furnished by the
manufacturer